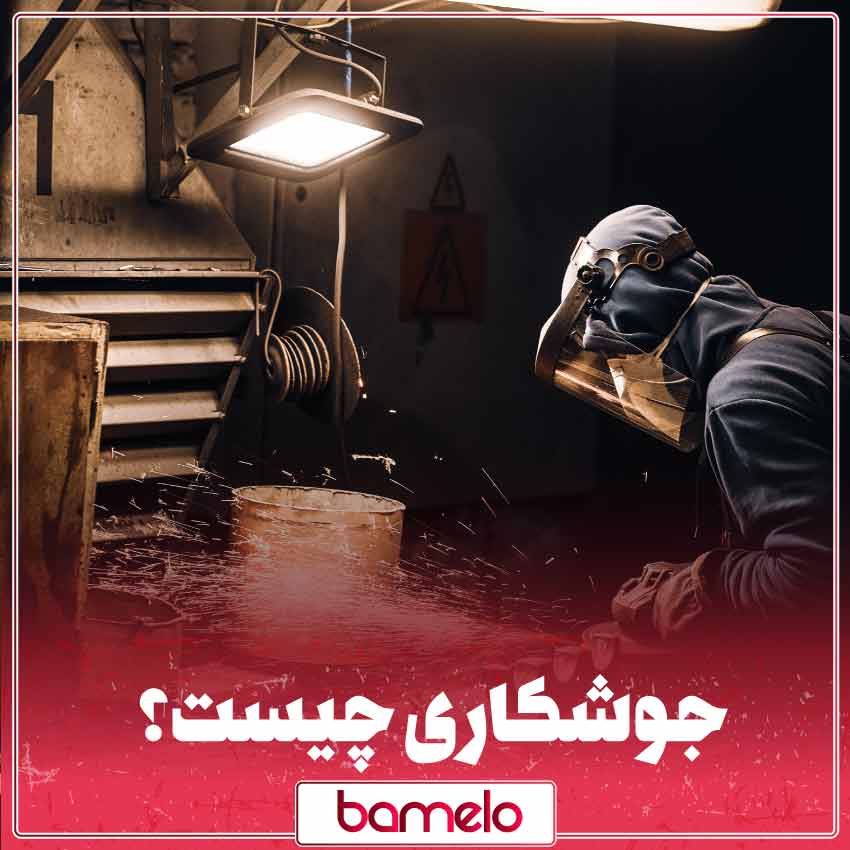
جوشکاری یا جوشدهی یکی از فرایندهای اساسی در صنایع مختلف است که برای ایجاد اتصال دائم و مستحکم بین قطعات فلزی مورداستفاده قرار میگیرد. این فرایند از طریق اعمال حرارت، فشار، جریان الکتریکی یا ترکیبی از آنها انجام میشود و استحکام و دوام بالایی را در اتصالات ایجاد میکند. جوشکاری در صنایع مختلفی مانند خودروسازی، ساختمانسازی، صنایع فلزی، لولهکشی، صنایع دریایی، هوافضا و بسیاری حوزههای دیگر نقش کلیدی دارد.
بستهبه نیازهای فنی و شرایط محیطی، روشهای گوناگونی برای جوشکاری وجود دارد که هر یک ویژگیها و کاربردهای خاص خود را دارند. این فرایند میتواند بهصورت دستی با ابزارهای ساده یا بهشکل خودکار با استفاده از ماشینآلات پیشرفته انجام شود. در جوشکاری، قطعات فلزی در نقاط تماس خود تحتتأثیر حرارت و فشار قرار میگیرد و پس از ذوب و سردشدن، یک اتصال یکپارچه و مستحکم ایجاد میکنند. منابع حرارتی مورداستفاده در این فرایند شامل قوس الکتریکی، لحیمکاری و دیگر روشهای گرمایشی است که بستهبه نوع جوشکاری مورداستفاده قرار میگیرند.
در بسیاری از روشها، از گازهای محافظ برای جلوگیری از اکسیداسیون و بهبود کیفیت جوش استفاده میشود. در ساخت دکلهای مخابراتی و انتقال نیرو، انتخاب روش جوشکاری مناسب اهمیت ویژهای دارد. دکلهای مهاری و منوپل هرکدام نیاز به روشهای خاصی برای جوشکاری دارند که بسته به نوع سازه، میزان فشار و شرایط محیطی تعیین میشوند. انتخاب صحیح روش جوشکاری در این سازهها، علاوه بر افزایش استحکام و طول عمر، از بروز مشکلاتی مانند خوردگی و شکستگی جلوگیری میکند.
مزایای جوشکاری
مزایای جوشکاری عبارتند از:
- ایجاد اتصال قوی و ماندگار بین اجزا
- امکان اتصال اجزا با شکلها و اندازههای مختلف
- قابلیت اتصال مواد مختلف با یکدیگر
- کارآیی بالا و سرعت بالا در انجام عملیات
- عدم نیاز به استفاده از اتصالات جداگانه مانند پیچومهره
بااینحال، جوشکاری همچنین ممکن است مشکلاتی همچون تغییر خواص مکانیکی مواد، تغییر شکل قطعات و مشکلاتی مرتبط با حرارت و تنش ایجاد کند. برای رفع این مشکلات، فرایندهای پس از جوشکاری مانند تغذیه، سختکاری و آزمونهای غیرمخرب نیز استفاده میشوند.
انواع جوشکاری
جوشکاری در انواع مختلفی وجود دارد. بهطور کلی به دو دسته ذوبی و غیرذوبی تقسیم میشود. هر کدام از این دو دسته، زیرمجموعههای مرتبط با خود را دارد که در ادامه با آنها آشنا میشوید.
جوشکاری ذوبی
جوشکاری ذوبی (Fusion Welding) یکی از روشهای اصلی جوشکاری است که در آن قطعات فلزی با استفاده از حرارت و ذوبشدن نواحی مشخص، به یکدیگر متصل میشوند. در این فرایند، مواد پایه فلزی با بهرهگیری از یک منبع حرارتی مانند قوس الکتریکی یا لیزر تا دمایی بالاتر از نقطه ذوب خود گرم و پس از ذوبشدن، اتصال مستحکمی بین آنها ایجاد میشود.
جوشکاری ذوبی در صنایع متعددی از جمله خودروسازی، صنایع دریایی، هوافضا، نفت و گاز و ساختمانسازی کاربرد دارد. این روش بهدلیل توانایی در اتصال قطعات فلزی با اشکال و ابعاد مختلف، از محبوبیت بالایی برخوردار است و اتصالاتی با استحکام و چگالی بالا ایجاد میکند.
انواع جوشکاری ذوبی
- شامل جوشکاری با پرتوی الکترونی (Electron Beam Welding)
- جوشکاری اکسیگاز (Oxy-Fuel Welding)
- جوشکاری قوسی (Arc Welding)
- جوشکاری با پرتو لیزری (Laser Beam Welding) است
هر یک بستهبه شرایط و نیازهای صنعتی، کاربرد خاص خود را دارند.
جوشکاری با پرتو الکترونی (EBW)
جوشکاری با پرتو الکترونی (EBW) یک فرایند جوشکاری است که در آن از پرتو های الکترونی برای ایجاد اتصالات جامد بین قطعات فلزی استفاده میشود. در این فرایند، الکترونها با سرعت بالا بهعنوان یک پرتو متمرکزشده ارسال میشوند و در نقطه مورد نظر روی قطعه تابیده میشوند.
این الکترونها در اثر برخورد با قطعه، انرژی خود را از دست میدهند و این انرژی تبدیل به گرما میشود. وقتی پرتو الکترونی روی قطعه تابیده میشود، انرژی حرکتی الکترون ها بهصورت حرارت منتقل میشود و باعث محلولشدن و ذوبشدن قسمتی از قطعه میشود. سپس، قطعهها به هم فشرده میشوند و جوشکاری نهایی انجام میشود.
این روش معمولاً برای جوشکاری قطعات فلزی پیچیده، اتصالاتی با شکلها و ضخامتهای مختلف و همچنین در برخی موارد برای جوشکاری فلزات با خواص خاص مورد استفاده قرار میگیرد.
مزایای جوشکاری با پرتو الکترونی (EBW)
- عمق نفوذ بالا: جوشکاری با پرتو الکترونی (EBW) قادر است باانرژی بسیار زیاد، به عمقهای بیشتری در مقایسه با سایر روشهای جوشکاری نفوذ کند. این ویژگی باعث میشود که این روش برای جوشکاری قطعات ضخیم، چندلایه یا موادی که نیاز به استحکام بالای اتصال دارند، بسیار کارامد باشد.
- ذوبکنندگی کمتر: در مقایسه با سایر روشهای جوشکاری، جوشکاری با پرتو الکترونی میزان کمتری از ماده را ذوب میکند. این ویژگی کمک میکند که تغییرات ابعادی قطعه بهحداقل برسد و از تغییرات ناخواسته در ساختار و مورفولوژی فلز جلوگیری شود.
- دقت بالای عملکرد: در این روش، پرتو الکترونی را میتوان بادقت زیادی روی محل جوش متمرکز کرد. این ویژگی باعث میشود جوشکاری بادقت بالا و حداقل میزان خطا انجام شود. علاوهبراین، چون در این روش هیچگونه تماس فیزیکی بین تجهیزات جوشکاری و قطعه وجود ندارد، احتمال آلودگی و تأثیر ناخالصیهای خارجی بسیار کاهش مییابد.
- نیاز کمتر به عملیات پسپردازش: بهدلیل کیفیت بالای جوش و کنترل دقیق فرایند، نیازی به مراحل اضافی مانند تمیزکاری، صافکاری و اصلاح جوش نیست. این موضوع باعث کاهش هزینههای تولید و صرفهجویی در زمان میشود.
- مناسب برای جوشکاری مواد حساس به حرارت: برخی از فلزات و آلیاژها مانند تیتانیوم و آلومینیوم نسبت به حرارت حساس هستند و در فرایندهای جوشکاری معمولی ممکن است دچار تغییرات نامطلوب در ساختار کریستالی شوند. جوشکاری با پرتو الکترونی بهدلیل کنترل دقیق دما، امکان اتصال این مواد را بدون ایجاد ترک، اعوجاج یا تخریب ساختار فراهم میکند.
تجهیزات جوشکاری با پرتو الکترونی (EBW)
- منبع تولید الکترون: دستگاهی که الکترونها را تولید و بهسمت قطعه کار هدایت میکند. این الکترونها با سرعت بالا به سطح فلز برخورد و انرژی موردنیاز برای ذوب و اتصال را تأمین میکنند.
- کانون جوشکاری: شامل سیستمهایی است که پرتو الکترونی را در یک نقطه مشخص متمرکز و امکان جوشکاری دقیق را فراهم میکنند. این بخش برای افزایش تمرکز انرژی و بهحداقلرساندن اتلاف حرارتی بسیار حیاتی است.
- جدول جوشکاری: برای قرارگیری و حرکت دقیق قطعات فلزی در حین جوشکاری استفاده میشود. این جدول معمولاً قابلیت چرخش و حرکت در چندین جهت را دارد تا امکان جوشکاری در زوایای مختلف فراهم شود.
- سیستم کنترل: شامل مجموعهای از سختافزار و نرمافزار است که فرایند جوشکاری را نظارت و تنظیم میکند. این سیستم امکان تغییر پارامترهایی مانند شدت پرتو، سرعت جوشکاری و موقعیت قطعات را به کاربر میدهد.
- سیستم خنککننده: از آب یا هوا برای کاهش دمای قطعات و جلوگیری از تغییر شکل یا آسیب حرارتی استفاده میشود. این سیستم برای حفظ کیفیت جوش و افزایش طول عمر تجهیزات ضروری است.
- سیستم ایمنی: شامل تجهیزاتی مانند محافظهای مخصوص برای جلوگیری از انتشار تشعشعات الکترونی و کاهش خطرات احتمالی برای اپراتور و محیط کار است.
جوشکاری اکسی گاز (Oxy-Fuel Welding – OFW)
فرایند جوشکاری: در این روش از ترکیب اکسیژن و یک گاز سوختی (مانند استیلن، پروپان یا هیدروژن) برای ایجاد شعلهای پرحرارت استفاده میشود که قطعات فلزی را ذوب و به هم متصل میکند.
ساختار شعله: ترکیب صحیح اکسیژن و گاز سوختی باعث تولید شعلهای با دمای بالا میشود که میتواند فلزات را تا نقطه ذوب گرم کند و جوشکاری را امکانپذیر سازد.
کاربردها: این روش بهدلیل سادگی تجهیزات و قابلیت حمل بالا، برای تعمیرات، جوشکاری ورقهای نازک، لولهکشی، صنایع خودروسازی و ساختوساز استفاده میشود.
انواع جوشکاری اکسی گاز
- جوشکاری با گاز پروپان: از پروپان بهعنوان گاز سوختی استفاده میشود.
- جوشکاری با گاز و فشار: در این روش، فشار گاز برای کنترل شعله و میزان حرارت استفاده میشود.
- جوشکاری هوا – استیلن: از ترکیب هوا و استیلن برای ایجاد شعله استفاده میشود که نسبتبه اکسیژن – استیلن دمای پایینتری دارد.
- جوشکاری اکسیژن – استیلن: رایجترین روش OFW که شعلهای با دمای بالا تولید میکند و برای جوشکاری فلزات مختلف مناسب است.
- جوشکاری اکسیژن – هیدروژن: از ترکیب اکسیژن و هیدروژن برای تولید شعلهای با دمای بالا استفاده میشود که برای جوشکاری فلزات خاص کاربرد دارد.
جوشکاری با گاز پروپان
جوشکاری با گاز پروپان یک روش جوشکاری است که در آن از گاز پروپان بهعنوان منبع حرارت استفاده میشود. گاز پروپان یکی از سوختهای فسیلی است که در صنعت برای تأمین حرارت در فرایندهای مختلف مورداستفاده قرار میگیرد، و جوشکاری یکی از این فرایندهاست.
برای جوشکاری با گاز پروپان، ابتدا یک فشار قوی از گاز پروپان و اکسیژن بههمراه منبع آتش درست میکنند. سپس این مخلوط گازی بهعنوان منبع حرارت برای ذوب قطعات موردنیاز استفاده میشود. ذوب قطعات میتواند با استفاده از شعله مستقیم یا با استفاده از پیستونهای هوای گرم نتیجه شود.
جوشکاری با گاز پروپان در فرایندهای مختلفی مانند جوشکاری فلزات، برش فلزات، گرمکردن و تغییر شکل قطعات فلزی و حتی جوشکاری لولههای پلاستیکی استفاده میشود. بههرحال، در هر روش جوشکاری، نکات ایمنی بسیار مهم هستند و باید دقت و احتیاط لازم را در استفاده از گاز پروپان و ابزارهای مربوطه رعایت کرد. همچنین، برای جوشکاری حرفهای و دقیق با گاز پروپان، میتوانید به آموزشهای مربوطه مراجعه کنید و یا با صنعتگران و کارشناسان مجرب از جمله باملو مشورت نمایید.
مزایای جوشکاری با گاز پروپان
این روش دارای مزایای زیادی است که شامل موارد زیر می شود؛
- همراهی با هزینه کمتر: استفاده از گاز پروپان در جوشکاری باعث کاهش هزینه های انرژی میشود؛ زیرا گاز پروپان در مقایسه با سایر گازهای جوشکاری مانند استیلن، آرگون و CO2، هزینه کمتری دارد.
- قابلیت استفاده در محیط های متنوع: گاز پروپان در محیط های مختلف و در شرایط متفاوت مانند فضای باز، دماهای مختلف و محیط های خشک و مرطوب، قابلاستفاده است. این ویژگی باعث میشود که جوشکاری با گاز پروپان برای زمینههای مختلف از جمله ساختوساز، تعمیرات، صنعت خودروسازی و صنایع فلزی، بسیار مناسب باشد.
- سهولت حملونقل: گاز پروپان در مقایسه با برخی دیگر انواع گازها، بهعنوان یک گاز فشرده و قابلحمل، آسانی در حملونقل را دارد. این مزیت برای کاربرانی که نیاز به جوشکاری در محلهای مختلف دارند، بسیار مهم است.
- قابلیت کنترل حرارت: گاز پروپان، با قابلیت تنظیم شدت و دمای شعله، به جوشکاران امکان میدهد تا در طول عملیات جوشکاری، حرارت مورد نیاز را کنترل کنند. این ویژگی بهعنوان یکی از مزیتهای مهم در جوشکاری با گاز پروپان محسوب میشود.
- آسانی استفاده: استفاده از جوشکاری با گاز پروپان بسیار آسان است و نیاز به تجهیزات پیچیده تری نسبتبه روشهای دیگر ندارد. این امر باعث میشود که حتی کاربران مبتدی نیز بتوانند با استفاده از گاز پروپان بهراحتی جوشکاری کنند.
جوشکاری با گاز و فشار چیست؟
جوشکاری با گاز و فشار یک روش اتصال قطعات فلزی است که در آن از حرارت و فشار گاز برای ایجاد اتصال بین قطعات استفاده میشود. در این روش، دو قطعه فلزی که قرار است به هم متصل شوند، با استفاده از حرارت و فشار گاز به حالت گدازه (محلول جامد و مذاب فلز) تبدیل میشوند و به یکدیگر متصل میشوند.
مزایای جوشکاری با گاز و فشار
- قابلیت جوشکاری قطعات با ضخامتهای مختلف: این روش برای جوشکاری فلزات نازک تا ضخیم کاربرد دارد و بهویژه برای قطعات سنگین و صنعتی مناسب است.
- اتصال قوی و بادوام: استفاده از فشار بالا و حرارت متمرکز منجر به ایجاد اتصالات محکم و مقاوم در برابر ضربه، تنش و ارتعاش میشود.
- کنترل دقیق دما و حرارت: امکان تنظیم دمای جوشکاری باعث بهبود کیفیت جوش و کاهش مشکلات ناشی از تغییرات حرارتی میشود.
- عدم نیاز به مصرف الکترود: برخلاف روشهای جوشکاری الکتریکی، در این روش نیازی به استفاده از الکترود نیست که هزینهها را کاهش میدهد.
- صرفهجویی در زمان و هزینه: سرعت بالای جوشکاری و کنترل بهینه فرایند، باعث کاهش مصرف مواد و افزایش بهرهوری میشود.
تجهیزات جوشکاری با گاز و فشار
- سیستم جوشکاری: این سیستم شامل یک محفظه گاز است که میتواند گازهای مختلفی مانند آرگون، هلیوم، ازوت و… را شامل شود. گاز بهعنوان محیط حمله در این روش استفاده میشود.
- سیستم فشار: در جوشکاری با گاز و فشار، فشاری بهقدرکافی روی قطعات فلزی وارد میشود تا آن ها را به هم فشرده کند و در نتیجه اتصال محکمی بین آنها ایجاد شود. این فشار میتواند بهصورت هیدرولیکی، پنوماتیک یا مکانیکی اعمال شود.
- حرارت: برای جوشکاری با گاز و فشار، قطعات فلزی به دمایی بالا (نزدیک به نقطه ذوب) گرم میشوند. این حرارت می تواند از طریق فنهای گازی، الکترودهای نیمهخودکار یا لولههای حرارتی به قطعات اعمال شود.
- زمان: برای ایجاد اتصال محکم، قطعات فلزی تحت فشار و حرارت قرار میگیرند و بهمدت زمانی مشخص (ممکن است به چند دقیقه برسد) در این شرایط نگهداشته میشوند تا اتصال بهخوبی شکل بگیرد.
جوشکاری هوا استیلن
جوشکاری هوا استیل یا بهعبارتدیگر جوشکاری فولاد ضدزنگ، فرایندی است که در آن قطعات فلزی از جنس فولاد ضدزنگ، که معمولاً از آلیاژهای فولادی با حداقل ۱۰.۵٪ کروم ساخته میشوند، به یکدیگر متصل میشوند.
فولاد ضد زنگ به دلیل خواصی که دارد، از جمله مقاومت در برابر زنگ زدگی، اکسیداسیون و خوردگی، در برخورد با شرایط محیطی سخت مورد استفاده قرار می گیرد. به طور کلی، جوشکاری هوا استیلن نیازمند مهارت و تخصص بالا است و برای اطمینان از کیفیت و قوت اتصال، بهتر است توسط کارگران ماهر و با استفاده از تجهیزات مناسب انجام شود.
مزایای جوشکاری هوا استیلن
در زیر تعدادی از اصلیترین مزایای جوشکاری هوا استیل را بررسی میکنیم؛
- مقاومت در برابر زنگ زدگی: هوا استیل مشهور به مقاومت بسیار بالا در برابر زنگزدگی است. با جوشکاری صحیح هوا استیل، میتوانیم این ویژگی مقاومت در برابر زنگزدگی را در اتصالات جوشی حفظ کنیم.
- قدرت مکانیکی بالا: هوا استیل دارای قدرت مکانیکی بسیار بالا است. با استفاده از روشهای جوشکاری مناسب، میتوان اتصالات جوشی با قدرت مکانیکی بالا و مقاومت در برابر تنشهای مختلف را ایجاد کرد.
- امکان شکلدهی: هوا استیل قابلیت شکلپذیری بسیار بالایی دارد. با استفاده از جوشکاری، میتوان اتصالات پیچیده و شکلپذیر را در هوا استیل ایجاد کرد و به طرحها و نیازهای خاص صنعتی پاسخ داد.
- مقاومت در برابر درجه حرارت: هوا استیل دارای مقاومت بالا در برابر درجه حرارت است. با استفاده از روشهای جوشکاری مناسب، میتوان اتصالات جوشی را در برابر درجه حرارتهای بالا و تغییرات حرارتی متنوع حفظ کرد.
- ظاهر زیبا: هوا استیل دارای ظاهری زیبا و جذاب است. با استفاده از جوشکاری هوا استیل، میتوان اتصالات جوشی را بهطور صحیح و زیبا ایجاد کرد و از ظاهری جذاب در محصولات و سازهها برخوردار شد.
- مقاومت شیمیایی: هوا استیل دارای مقاومت بسیار خوبی در برابر عوامل شیمیایی است. با جوشکاری هوا استیل، میتوان اتصالاتی با مقاومت شیمیایی بالا در برابر اکسیداسیون، خوردگی و تاثیرات محیطی دیگر ایجاد کرد.
تجهیزات جوشکاری هوا استیل
- ماشینهای جوشکاری مقاومتی: برای جوشکاری قطعات هواستیل به همدیگر از ماشینهای جوشکاری مقاومتی میتوان استفاده کرد. این ماشینها عموماً شامل دستگاههایی با الکترودهای کوتاه و دائمی هستند.
- لیزر جوشکاری: از لیزرهای قدرتمند برای جوشکاری قطعات هواستیل نیز استفاده میشود. در این روش، انرژی لیزر بهصورت دقیق روی قسمتهای مورد نظر متمرکز میشود و باعث جوشکاری محلی و دقیق میشود.
مزایای جوشکاری با اکسیژن استیلن
- ایجاد حرارت بالا: شعله حاصل از ترکیب اکسیژن و استیلن دمایی تا حدود ۳۵۰۰ درجه سانتیگراد تولید میکند که برای ذوب بسیاری از فلزات مناسب است.
- قابلیت جوشکاری فلزات مختلف: این روش برای جوشکاری فولاد کربنی، فولاد ضدزنگ، آلومینیوم، مس و برخی آلیاژها کاربرد دارد.
- قابلیت کنترل شعله: شدت و ترکیب شعله را میتوان تنظیم کرد تا متناسب با نوع و ضخامت فلز موردنظر باشد.
- عدم نیاز به برق: برخلاف جوشکاری الکتریکی، این روش نیازی به منبع برق ندارد و میتوان از آن در محیطهای بیرونی و مناطق دورافتاده استفاده کرد.
- مقرونبهصرفهبودن تجهیزات: ابزارهای موردنیاز برای این روش نسبتاً ساده و ارزان هستند و نگهداری آنها نیز آسان است.
- امکان برشکاری و لحیمکاری: علاوه بر جوشکاری، از این روش برای برش فلزات و لحیمکاری سخت نیز استفاده میشود.
مزایای جوشکاری با استفاده از اکسیژن استیلن
جوشکاری با استفاده از اکسیژن استیلن مزایای زیادی دارد که در ادامه آنها را معرفی میکنیم؛
- امکان جوشکاری قطعات با ضخامت مختلف
- قابلیت جوشکاری در محل و در محیطهای بیرونی
- قابلیت استفاده در تعمیرات و تعمیرات فوری
- هزینه نسبتاً پایین نسبتبه روشهای جوشکاری پیچیده تر
تجهیزات جوشکاری با استفاده از اکسیژن استیلن
- دستگاه جوشکاری استیلن: دستگاهی که برای ایجاد لهجه حرارتی بالا و آتش برای جوشکاری استفاده میشود. این دستگاه معمولاً شامل یک تورچ استیلن، بخاری، و اجزای دیگر برای تأمین سوخت و اکسیژن استیلن است.
- بطریهای گاز: برای تأمین سوخت و اکسیژن استیلن، بطریهای گاز مخصوصی استفاده میشود. این بطریها حاوی سوخت استیلن و اکسیژن هستند و با استفاده از رگولاتورها و شیرهای کنترل، فشار و دبی گاز را تنظیم میکنند.
- لوازم ایمنی: همانند هر فرایند جوشکاری دیگر، استفاده از لوازم ایمنی مناسب از جمله عینک جوشکاری، لباس محافظ، دستکشهای مقاوم در برابر حرارت و سایر لوازم محافظ جوشکاری بسیار مهم است.
- جوشکاران ماهر: جوشکاران ماهری که تجربه و آموزش لازم را در زمینه جوشکاری با استفاده از اکسیژن استیلن دارند، برای انجام عملیات جوشکاری بهخوبی و با کیفیت لازم احتیاج است.
جوشکاری اکسیژن هیدروژن
جوشکاری اکسیژن هیدروژن یا بهعبارتیدیگر جوشکاری HHO، روشی است که در آن از ترکیب گازهای هیدروژن و اکسیژن استفاده میشود تا در فرایند جوشکاری بهعنوان منبع حرارت و انرژی استفاده شود.
در این فرآیند، گاز هیدروژن و اکسیژن به نسبت 2:1 تولید و میسوزند تا آتش و جرقهای بزرگ و بسیار گرم تولید شود. جوشکاری اکسیژن هیدروژن بهدلیلداشتن خصوصیات خاص، میتواند در برخی از برنامههای جوشکاری مفید باشد.
مزایای جوشکاری اکسیژن هیدروژن
جوشکاری اکسیژن هیدروژن مزایای زیادی دارد که در ادامه برخی از آنها را معرفی میکنیم.
- حرارت بالا: جوشکاری اکسیژن هیدروژن دارای دماهای بسیار بالاست که می تواند منجر به ذوب و اتصال قطعات فلزی باشد. این حرارت بالا بهدلیل احتراق مخلوط هیدروژن و اکسیژن است که نیازی به منبع خارجی برقی یا گازی ندارد.
- عدم تشکیل ذرات پرت: با استفاده از جوشکاری HHO، از دست دادن مواد جامد یا پرتی های ذرات فلزی بهصورت قابل توجهی کاهش می یابد. این امر می تواند در برخی کاربردهای دقیق و حساس مانند جوشکاری قطعات الکترونیکی مفید باشد.
- محیط زیستی: در هنگام احتراق هیدروژن و اکسیژن، تنها محصول تولیدشده آب است. بهعبارتیدیگر، این فرایند صفر گازهای گلخانهای و آلودگی هوا تولید میکند و بسیار کمترین تأثیر بر محیط زیست دارد.
- کاربرد گسترده: جوشکاری اکسیژن هیدروژن در صنایع مختلفی از جمله خودروسازی، ساختوساز، تولید انرژی، جوشکاری لولهها و… مورد استفاده قرار می گیرد.
تجهیزات جوشکاری اکسیژن هیدروژن
- مولد هیدروژن و اکسیژن: این دستگاه برای تولید هیدروژن و اکسیژن در نسبت صحیح برای جوشکاری استفاده میشود. معمولاً از فناوری الکترولیز برای تفکیک آب به هیدروژن و اکسیژن استفاده میشود.
- لولهها و خطوط تامین گاز: هیدروژن و اکسیژن تولیدشده توسط مولد به کمک لولهها و خطوطی به جوشکار منتقل میشوند.
- سوزن و قلم جوشکاری: سوزن جوشکاری بهطور معمول از جنس مس است و در آن جرقه برقی میان هیدروژن و اکسیژن تشکیل میشود. قلم جوشکاری برای اتصال قطعات مورد نظر با استفاده از حرارت و لحیمکاری استفاده میشود.
- سیستم کنترل و ایمنی: این سیستم شامل سوئیچها، شیرها، صمامها و دستگاههای کنترلی است که جریان گاز را کنترل و از نظر ایمنی اطمینان حاصل میکند.
جوشکاری قوسی
جوشکاری قوسی یک روش جوشکاری است که در آن جرقههای الکتریکی بین قطبهای مثبت و منفی یک الکترود تشکیل می شود. این جرقهها یک دمای بسیار بالا و یک ماده یونیزهشده بهنام پلاسما ایجاد میکنند که باعث انجام فرایند جوشکاری میشود.
در جوشکاری قوسی، قوس الکتریکی بین دو الکترود تشکیل میشود. یک الکترود بهنام الکترود مثبت (آنود) و دیگری بهنام الکترود منفی (کاتود) است. این الکترودها به روشنشدن الکترودها یا با استفاده از جریان برق مستقیم یا جریان متناوب باعث ایجاد قوس الکتریکی می شوند.
قوس الکتریکی تولیدشده در جوشکاری قوسی بسیار داغ است و مواد قابلجوشکاری را به دماهای بالا میرساند. این دماهای بالا باعث ذوبشدن مواد قابلجوشکاری میشوند و با استفاده از مواد جوشکاری مثل سیم جوشکاری، قطعات جوشکاری میشوند.
جوشکاری قوسی در صنایع مختلفی مانند خودروسازی، ساختوساز، صنعت فضایی و صنایع فلزی استفاده میشود. این روش جوشکاری نسبتاً سریع و اقتصادی است و بهطور گسترده ای در صنعت مورد استفاده قرار میگیرد. جوشکاری قوسی در انواع مختلفی وجود دارد که عبارتند از؛
- جوشکاری قوسی با الکترود دستی روکش دار (SMAW)
- جوشکاری قوسی با گاز محافظ و الکترود فلزی (MIG/MAG یا GMAW)
- جوشکاری قوسی با گاز محافظ و الکترود تنگستنی (GTAW یا TIG)
- جوشکاری قوس پلاسما (PAW)
- جوشکاری قوسی زیر پودری (SAW)
- جوشکاری قوسی توپودری (FCAW)
- جوشکاری اتمی هیدروژن
- جوشکاری قوسی کربنی (CAW)
جوشکاری قوسی با الکترود دستی روکش دار (SMAW)
جوشکاری قوسی با الکترود دستی روکش دار (SMAW) یکی از روشهای شایع جوشکاری فلزات است که با استفاده از الکترودهای قوسی کار میکند. در این روش، قوس الکتریکی بین الکترود و قطعه کار ایجاد میشود که باعث ذوبشدن الکترود و تشکیل حوضچه جوش میشود.
در SMAW، الکترود دستی شامل قسمت مرکزی (از فلز جوشکاریشده تشکیل شده است) و روکش حفاظتی است که قوس جوش را از هوا و عناصر خارجی محافظت میکند. روکش حفاظتی از موادی مانند مس یا فریت تشکیل شده است که هنگام جوشکاری ذوب میشود و پوششی حاکم بر سطح جوش ایجاد میکند.
این پوشش بهعنوان یک لایه محافظ عمل میکند و از مخلوطشدن قوس جوش با هوا، اکسیژن و نیتروژن جلوگیری میکند که میتواند به تشکیل شکستگیها و ناهمواریهای سطحی در جوش منجر شود.
فرایند SMAW برای جوشکاری فلزات مختلف از جمله فولاد، آهن، آلومینیوم و فلزات غیرآهنی استفاده میشود. این روش جوشکاری قابلاجرا در شرایط خارج از کارگاهی و در محیطهای باز است و بهعلت استفاده از الکترود دستی برای جوشکاری، بهطور گستردهای در صنعت ساختمانی، خودروسازی، تعمیرات و ساختوساز استفاده میشود.
جوشکاران ماهر برای انجام SMAW باید دقت کافی را در تنظیم جریان جوش، نوع و قطر الکترود، نوع وضعیت جوشکاری (عمودی، افقی و…) و تکنیکهای موجود در این روش داشته باشند.
مزایای جوشکاری قوسی با الکترود دستی روکش دار (SMAW)
- قابلیت استفاده در شرایط دشوار: جوشکاری SMAW می تواند در شرایط فضای باز و در محیطهای خارجی با شرایط آبوهوایی متفاوت انجام شود. علاوهبراین، این روش در محیطهای با امکانات محدود و محیط های دسترسی محدود نیز قابل استفاده است.
- امکان استفاده در جوشکاری توده ای: با استفاده از الکترودهای قوی و قطر بزرگ، جوشکاری SMAW قادر است به جوشکاری تودههای ضخیم و قطعات سنگین بپردازد. این امکان در برخی روشهای دیگر جوشکاری وجود ندارد.
- انعطاف پذیری مواد جوشکاری: جوشکاری SMAW قابلیت جوشکاری انواع مواد فلزی متفاوت را داراست، از جمله فولاد، آلومینیوم، استیل و… . همچنین، میتوان با انتخاب الکترودهای متناسب با نوع فلز، خواص مکانیکی جوش را تنظیم کرد.
- هزینه کم: ابزارهای مورد نیاز برای جوشکاری SMAW ساده و ساخت آنها ارزان است. این روش نیاز به تجهیزات پیشرفتهتر مانند گاز محافظ و دستگاههای پیچیده را ندارد؛ هزینه کمتری برای جوشکاری بههمراه دارد.
- قابلیت استفاده در محل: یکی از مزایای بزرگ جوشکاری SMAW، امکان استفاده در محل است. این روش قابلیت انجام جوشکاری در محلهای مختلف را فراهم میکند، از جمله در تعمیرات در محل، ساختوساز در محیطهای خارجی و تعمیرات اضطراری.
تجهیزات جوشکاری الکترود دستی
- الکترودها: الکترودها معمولاً شامل قطب مثبت و منفی هستند. قطب مثبت بهعنوان الکترود اصلی استفاده میشود و قطب منفی بهعنوان مقطع کار مورداستفاده قرار میگیرد. الکترودها براساس نوع مواد جوش، قطر و نوع پوشش خارجی طبقه بندی میشوند.
- منبع برق: برای جوشکاری الکترود دستی، منبع برقی قدرتمندی که قادر به تأمین جریان الکتریکی لازم برای جوشکاری است، لازم است. منابع برق معمولاً شامل ترانسفورماتورهای جریان مستقیم (DC) یا ترانسفورماتورهای جریان متناوب (AC) هستند. همچنین، برخی از منابع برق قابلحمل بودند و برای کارهای میدانی مناسب هستند.
- لبهها و فریمها: جهت نگهداری الکترود و قطعات فلزی، لبهها و فریمهای جوشکاری استفاده میشود. این تجهیزات می توانند برای تثبیت قطعات فلزی و جلوگیری از حرکت غیرضروری در حین جوشکاری مفید باشند.
- لباسهای ایمنی: جوشکاری الکترود دستی ممکن است با خطراتی همچون ذرات فلزی مذاب، اشعه UV و خطرات حرارتی همراه باشد. لباسهای ایمنی مانند عینکهای ایمنی، لباسهای ضدحرارت، دستکشهای محافظ و کاپشنهای آتشنشانی برای حفاظت از جوشکاران بسیار مهم هستند.
- ابزارهای جانبی: برخی از ابزارهای جانبی مورد نیاز برای جوشکاری الکترود دستی شامل قیچی جوشکاری، خرطوم جوشکاری، برس سیمان و قیچی فلزات است.
جوشکاری قوسی با گاز محافظ و الکترود فلزی (MIG/MAG یا GMAW)
جوشکاری قوسی با گاز محافظ و الکترود فلزی (MIG/MAG یا GMAW) یک روش جوشکاری است که در آن الکترود فلزی بهعنوان منبع جوشکاری استفاده میشود. این روش معمولاً برای جوشکاری فلزات آهنی و غیرآهنی استفاده میشود و در صنعت و ساختوساز بسیار رایج است.
در جوشکاری MIG/MAG، الکترود فلزی بهصورت پیوسته وارد منطقه جوشکاری میشود و توسط جریان قوس الکتریکی ذوب میشود. درهمینحین، گاز محافظی مانند آرگون یا مخلوطی از آرگون و دی اکسید کربن از طریق نازل الکترود به منطقه جوشکاری پخش میشود.
این گاز محافظ برای حفظ و محافظت از منطقه جوشکاری و جوشکاری از تاثیر جوی و اکسیژن هوا استفاده میشود و همچنین بهعنوان یک پوشش محافظ برای جوشکاری و جامعه جوشکاری عمل میکند.
روش MIG/MAG یا GMAW بسیار محبوب است؛ زیرا سرعت بالا، کیفیت بالا و امکانات خوبی در جوشکاری لحیم و انتقال گرمای جوشکاری دارد. همچنین، این روش قابلیت اتوماسیون و خودکارسازی را دارد که امکان جوشکاری در خطوط تولید صنعتی را فراهم میکند.
مزایای جوشکاری قوسی با گاز محافظ و الکترود فلزی (MIG/MAG یا GMAW)
جوشکاری قوسی با گاز محافظ و الکترود فلزی (MIG/MAG یا GMAW) یکی از روشهای پرکاربرد جوشکاری است و دارای بسیاری از مزایا است. در زیر تعدادی از این مزایا آمده است؛
- سرعت بالا: جوشکاری MIG/MAG یکی از روشهای سریع و کارامد جوشکاری است. استفاده از الکترود فلزی و جریان قوسی مستقیم در این روش به جوشکار امکان میدهد با سرعت بالا جوشکاری را انجام دهد و بهطور مداوم الکترود را پیشروی دهد.
- کارایی بالا: با استفاده از گاز محافظ در جوشکاری MIG/MAG، امکان خنککردن الکترود و منطقه جوش را فراهم میکند. این بهمعنی کاهش آلایندهها، پیشگیری از تشکیل شیارها و حفظ خواص مکانیکی قطعه جوش شده است. همچنین، استفاده از الکترود فلزی باعث کاهش آلایش با آلومینیوم و اکسید نیتروژن میشود.
- قابلیت جوشکاری خودکار: جوشکاری MIG/MAG بهخوبی برای جوشکاری خودکار مناسب است. این روش امکان استفاده از رباتهای جوشکاری را فراهم میکند که باعث افزایش سرعت و دقت جوشکاری میشود.
- قابلیت استفاده در انواع فلزات: جوشکاری MIG/MAG قابلیت استفاده در انواع مختلفی از فلزات را دارد؛ از جمله فولادهای کربنی، فولادهای ضدزنگ، آلومینیوم و فلزات دیگر. با تغییر الکترود و گاز محافظ، میتوان بهسادگی با مواد مختلف جوشکاری کرد.
- کم هدررفتن مواد جوش: در جوشکاری MIG/MAG بهدلیل استفاده از الکترود فلزی، هیچ بخشی از الکترود بهعنوان ضایعات از بین نمیرود. این باعث میشود هزینههای مربوط به جوشکاری، از جمله هزینه مصرف الکترود، کاهش یابد.
- کنترل آسان: جوشکاری MIG/MAG از دستگاههای کنترل آسانی استفاده میکند که به جوشکار امکان کنترل دقیق جریان قوس، سرعت الکترود و جریان گاز محافظ را میدهد. این کنترل دقیق باعث ایجاد جوشکاری باکیفیت و دقیقتر میشود.
- جوشکاری بهرهور: جوشکاری MIG/MAG بهدلیل سرعت بالا، کارایی بالا و کاهش ضایعات مواد جوش، از لحاظ اقتصادی بهرهور است. این روش امکان جوشکاری سریعتر و به میزان بیشتری را فراهم میکند که میتواند در تولید صنعتی بهبود قابلتوجهی داشته باشد.
تجهیزات جوشکاری قوسی با گاز محافظ و الکترود فلزی (MIG/MAG یا GMAW)
- بستر جوشکاری (Welding Power Source): این واحد تأمینکننده جریان الکتریکی برای جوشکاری است. آن را میتوان با استفاده از برق شهری یا سایر منابع برقی انرژی زا تغذیه کرد. بستر جوشکاری باید قابلیت تنظیم جریان، ولتاژ و سرعت پیشرانش را داشته باشد.
- سیم جوش (Welding Wire): سیم جوش فلزی بهعنوان الکترود در این روش جوشکاری استفاده میشود. سیم جوش ممکن است از جنسهای مختلفی مانند فولاد کربنی، فولاد ضدزنگ و آلیاژهای خاص ساخته شود. انتخاب سیم جوش صحیح براساس جنس قطعه کار و نیازهای جوشکاری مشخص میشود.
- سیم تغذیه (Wire Feeder): سیم تغذیه برای تغذیه سیم جوش بهطور مستقیم به نقطه جوشکاری استفاده میشود. این واحد سیم جوش را بهسرعت و جریان مورد نیاز برای جوشکاری منظم تغذیه میکند.
- گاز محافظ (Shielding Gas): گاز محافظ برای حفاظت فضای جوشکاری از هوا و آلایندهها استفاده میشود. نوع گاز محافظ بستهبه نوع فلز جوشکاری و شرایط جوشکاری ممکن است متفاوت باشد. برخی از محافظهای گازی شامل آرگون، دی اکسید کربن و مخلوطی از آرگون و دی اکسید کربن هستند.
- تورچ جوشکاری (Welding Torch): تورچ جوشکاری شامل سیم جوش، سیم تغذیه و خروجی گاز محافظ است. این تورچ قابلیت کنترل دقیق تغذیه سیم جوش، گاز محافظ و جریان الکتریکی را فراهم میکند. عملکرد صحیح تورچ جوشکاری توسط جوشکار بسیار مهم است.
جوشکاری قوسی با گاز محافظ و الکترود تنگستنی (GTAW یا TIG) چیست؟
جوشکاری قوسی با گاز محافظ و الکترود تنگستنی (GTAW)، بهطور عام با نام TIG (تونگستن بهمعنای الکترود Tungsten Inert Gas) نیز شناخته میشود، یک روش جوشکاری است که برای اتصال قطعات فلزی استفاده میشود.
در این روش، یک الکترود تنگستنی غیر مصرفی در دستگاه جوش قرار داده می شود که توسط جریان الکتریکی گرم میشود. همچنین، برای حفظ و تأمین یک محیط غیر فعال اطراف سوزن جوش، یک گاز محافظ (معمولاً آرگون و همچنین مخلوط آرگون و هلیم) از طریق نازل دستگاه جوش به منطقه جوشکاری تزریق میشود.
در این روش، جریان الکتریکی بین الکترود تنگستنی و قطعات فلزی ایجاد میشود که باعث تشکیل یک قوس الکتریکی بین آنها میشود. در نتیجه، قطعات فلزی بهدلیل حرارت تولیدشده توسط قوس الکتریکی، ذوب میشوند و با هم اتصال مییابند.
جوشکاری GTAW بهدلیل کنترل دقیق دما، اتصال قوی و کیفیت بالا، برای اتصال قطعات فلزی از جنسهای مختلف، بهخصوص فلزات آلیاژی حساس، استفاده میشود. این روش جوشکاری معمولاً در صنایع مختلفی مانند صنعت خودرو سازی، صنعت هواوفضا، صنعت دریایی، تولید لولهها و سیستمهای لولهکشی، تولید قطعات پزشکی و صنایع دیگر مورد استفاده قرار میگیرد.
مزایای جوشکاری قوسی با گاز محافظ و الکترود تنگستنی (GTAW یا TIG)
- کنترل دقیق: جوشکاری TIG برخلاف بسیاری از روشهای دیگر، امکان کنترل دقیق روی فرایند جوشکاری را فراهم میکند. این بهمعنای امکان تنظیم جریان الکتریکی، سرعت جریان گاز محافظ، سرعت تغذیه الکترود و دیگر پارامترهای فرایند است. این امکان به جوشکاران کمک میکند تا کنترل دقیقتری روی جوشکاری داشته باشند و نتایج بهتری را بهدست آورند.
- کیفیت بالا: با استفاده از جوشکاری TIG، میتوان کیفیت بالایی از نظر ظاهری و مکانیکی در جوشها بهدست آورد. این روش بهعلت استفاده از الکترود تنگستنی باعث تولید جوشکاری تمیز و دقیق میشود. جوشهای TIG بهطور معمول کمترین ناهمواریها، خزشها و خطوط لغزشی را نسبتبه سایر روشها دارند.
- عدم استفاده از ماده جانبی: در جوشکاری TIG، الکترود تنگستنی برای تولید قوس الکتریکی استفاده میشود و بهطور معمول ماده جانبی اضافی به فرایند اضافه نمیشود. این موضوع در بسیاری از کاربردها مفید است، بهخصوص زمانی که از آلیاژهای خاصی استفاده میشود که بهطور معمول نیاز به اضافهکردن ماده جانبی ندارند.
- قابلیت جوشکاری متناهی: جوشکاری TIG بهدلیل کنترل دقیق و عدم استفاده از ماده جانبی، برای جوشکاری قطعات بسیار نازک و حساس مناسب است. با استفاده از این روش میتوان قطعاتی را جوش داد که ضخامت بسیار کمی داشته باشند.
- استفاده در جوشکاری آلیاژهای خاص: GTAW معمولاً برای جوشکاری آلیاژهای خاصی مانند آلومینیوم، استیل ضدزنگ و آلیاژهای تیتانیوم استفاده میشود. این روش بهدلیل عدم اضافهکردن ماده جانبی و کنترل دقیق، در جوشکاری این نوع آلیاژها عملکرد بسیار خوبی دارد.
جوشکاری قوس پلاسما (PAW)
جوشکاری قوس پلاسما (Plasma Arc Welding یا PAW) یک روش جوشکاری پیشرفته است که از قوس پلاسما برای اتصال قطعات فلزی استفاده میکند. در این فرایند، قوس پلاسما توسط جریان الکتریکی بین یک الکترود منفی (کاتد) و قطعه کار (آند) ایجاد میشود.
قوس پلاسما، با تولید یک جریان الکتریکی بسیار بالا و ایجاد حرارت بسیار زیاد، گازهای اطراف را یونیزه و بهحالت پلاسما تبدیل میکند. در جوشکاری قوس پلاسما، از یک نوار فلزی با نقطه ذوب بالا برای جوشکاری استفاده میشود.
این نوار فلزی، بهعنوان الکترود کاتدی عمل میکند و توسط جریان الکتریکی از طریق آند گرم میشود. همچنین، گازهای محافظ نیز بهمنظور جلوگیری از تعامل قوس با جوی محیط استفاده میشوند.
قوس پلاسما در جوشکاری قوس پلاسما دما و انرژی بالایی دارد که امکان جوشکاری مواد با ضخامتهای بزرگتر را فراهم می کند. همچنین، بهدلیل دمای بالا و شدت حرارت قوس پلاسما، این فرایند میتواند با سرعت بالا انجام شود و اتصالات قوی و باکیفیتی را بهوجود آورد. PAW معمولاً در صنایع مختلفی مانند صنایع هواوفضا، خودروسازی، الکترونیک و ساختوساز استفاده میشود.
در مجموع، جوشکاری قوس پلاسما یک روش پیشرفته و کارامد برای اتصال قطعات فلزی است که با استفاده از قوس پلاسما، امکان جوشکاری مواد با ضخامت بالا و تولید اتصالات با کیفیت بالا را فراهم میکند.
مزایای جوشکاری قوس پلاسما (PAW)
- قدرت نفوذ بالا: در جوشکاری قوس پلاسما، قدرت نفوذ بالایی در اتصال جوش ایجاد میشود. این به معنی توانایی ایجاد اتصالات محکم و عمیق در ترکیبات فلزی ضخیم است. بهعلاوه، قدرت نفوذ بالا میتواند کاهش نیاز به طیف وسیعی از پردازشهای پیشرفته مثل چسباندن، مته نوکی و برش باشد.
- نیاز به تمیزکاری کم: PAW معمولاً نیازی به تمیزکاری یا حذف لایه اکسید از سطح قطعهها ندارد. این بهمعنی کاهش زمان و هزینههای مربوط به آمادهسازی سطح قطعهها قبل از جوشکاری است.
- آسانی استفاده: PAW قابلیت کنترل و استفاده آسان را فراهم میکند. تنظیماتی مثل جریان الکتریکی و گاز محافظ قابلتنظیم هستند که به جوشکاران اجازه میدهد پارامترهایی جوشکاری را براساس نیازهای خود تنظیم کنند. همچنین، عدم وابستگی بهجهت گرانش در فرایند PAW به اپراتورها اجازه میدهد بهراحتی در موقعیتهای مختلف قرار بگیرند و به جوشکاری دسترسی داشته باشند.
- کیفیت جوش بالا: PAW قابلیت ایجاد اتصالات جوش با کیفیت بالا را دارد. این روش بهدلیل امکان استفاده از گاز محافظ و جریان الکتریکی دقیق، کنترل دما و سرعت سردشدن جوش را فراهم میکند. نتیجه آن، جوشهای متناسب با استانداردهای کیفیت بالا و قابلقبول بین المللی است.
- امکان استفاده در محیطهای مختلف: PAW بهعنوان یک فرایند مبتنی بر قوس الکتریکی، امکان استفاده در محیطهای مختلف را دارد. می توان در فضای باز یا در محیطهای آبی از این روش استفاده کرد.
تجهیزات جوشکاری قوس پلاسما (PAW)
- منبع برق: منبع برق برای تولید جریان الکتریکی مورد نیاز برای ایجاد قوس پلاسما استفاده میشود. این منبع میتواند از نوع تکنولوژی ترانسفورماتور، روتاری یا مبدل الکترونیکی باشد.
- الکترودها: در جوشکاری قوس پلاسما، استفاده از الکترودهای مخصوصی که قابلیت تحمل جریان بالا و تابش پلاسمای قوی را داشته باشند، ضروری است. این الکترودها معمولاً از مواد مانند تنگستن یا تنگستن آلیاژی تهیه میشوند.
- تورچ جوشکاری: تورچ جوشکاری قوس پلاسما برای ایجاد قوس الکتریکی و انتقال جریان پلاسما به نقطهجوش استفاده میشود. تورچ بهصورت دستی در دسترس قرار میگیرد و دارای سیستم خنککننده است تا حرارت تولیدشده توسط جریان پلاسما را تا حداقلی کاهش دهد.
- گاز محافظ: برای حفاظت از منطقه جوشکاری و جلوگیری از تداخل با هوا و آلایندهها، از یک گاز محافظ استفاده میشود. گازهای متداول برای جوشکاری قوس پلاسما شامل آرگون، هلیم و نیتروژن میشوند.
- سیستم کنترل: تجهیزات جوشکاری قوس پلاسما معمولاً دارای یک سیستم کنترل هوشمند هستند که برای تنظیم جریان، شدت و دمای قوس و متغیرهای دیگر مورد استفاده قرار میگیرد. این سیستم کنترل میتواند از نوع دستی یا خودکار باشد.
جوشکاری قوسی زیرپودری (SAW) چیست؟
جوشکاری قوسی زیرپودری (Submerged Arc Welding)، مخفف SAW است، یک روش جوشکاری است که در آن قوس الکتریکی بین الکترود فلزی و قطعه کار بهوسیله یک پودر فلزی (بهعنوان الکترود فرقدهنده) در محیط زیرپودری تشکیل میشود. این روش بهعنوان یکی از روشهای جوشکاری غوطهور معروف است.
در جوشکاری قوسی زیر پودری، قوس الکتریکی بین الکترود و قطعه کار در یک محیط پودری تشکیل میشود. این پودر فلزی که بهعنوان الکترود فرقدهنده عمل میکند؛ بهطور مستقیم در قلب قوس قرار دارد و با حرارت قوس ذوب میشود. در اثر ذوبشدن پودر فلزی، قطرههای ذوبشده بهصورت زیرپودری به سطح جوش میریزند و جوش تشکیل میشود.
مزایای جوشکاری قوسی زیر پودری
- سرعت جوشکاری بالا: این روش بهدلیل استفاده از الکترود فلزی بزرگ و محیط زیر پودری، سرعت جوشکاری بالا و پوشش بزرگی را ارائه میدهد.
- عملکرد بهتر: جوشکاری قوسی زیرپودری میتواند به عملکرد مکانیکی و مقاومت در برابر خستگی قطعه کار کمک کند.
- کیفیت جوش بالا: با استفاده از این روش، جوشهایی با کیفیت بالا، اندازههای یکنواخت و خواص مکانیکی مطلوب تولید میشوند.
- توانایی جوشکاری در شرایط خاموش: بهدلیل استفاده از محیط زیرپودری، این روش قابلیت جوشکاری در شرایطی که قوس الکتریکی قابل رویت نیست را داراست.
- کارآیی بالا: باتوجهبه سرعت جوشکاری بالا و امکان استفاده از الکترود فلزی بزرگ، این روش کارآیی بالایی دارد.
تجهیزات جوشکاری قوسی زیر پودری (SAW)
منبع تغذیه الکتریکی: برای تولید قوس الکتریکی و تامین جریان لازم برای جوشکاری، نیاز به یک منبع تغذیه الکتریکی است. منبع تغذیه معمولاً از نوع ترانسفورماتوری یا اینورتری است و می تواند برای جریان مستمر یا جریان متناوب استفاده شود.
الکترود قوسی: برای جوشکاری قوسی زیر پودری از الکترود های قوسی خاصی استفاده می شود. این الکترود ها شامل هسته فلزی و پوشش معدنی هستند و عمدتاً از فولاد کربنی یا فولاد آلیاژی تشکیل شده اند.
دستگاه تغذیه الکترود: برای حرکت خودکار الکترود در طول جوشکاری، نیاز به یک دستگاه تغذیه الکترود و سیستم حرکتی دارید. این دستگاه الکترود را به طور پیوسته و تدریجی تغذیه می کند تا الکترود به صورت خودکار حرکت کند و طول قوس را حفظ کند.
دستگاه پودرزنی: برای تغذیه پودر معدنی زیر پودری، نیاز به یک دستگاه پودرزنی است. این دستگاه پودر را به صورت خودکار و به میزان دقیقی تغذیه می کند تا پوشش محافظ روی جوش تشکیل شود.
سیستم خنک کننده: در طول جوشکاری قوسی زیر پودری، دمای بالای الکترود و قطعه کار ممکن است باعث افزایش دمای تجهیزات شود. برای جلوگیری از آب گرفتگی و خرابی تجهیزات، نیاز به سیستم خنک کننده است که حرارت را از تجهیزات جوشکاری تخلیه می کند.
جوشکاری قوسی توپودری (FCAW) چیست؟
جوشکاری قوسی توپودری (FCAW) یک روش جوشکاری است که در آن الکترود مورد استفاده شامل یک سیم فلزی پر شده با پودر فلزی است. در این روش، قوس الکتریکی بین الکترود و قطعه کاری تشکیل میشود و درهمینحین، پودر فلزی بهصورت خودکار از داخل الکترود تغذیه میشود و در منطقه جوشکاری ذوبشده و با فلز پایه ترکیب میشود.
جوشکاری قوسی توپودری یک روش پیشرفته از جوشکاری قوسی با الکترود پر شده است. با استفاده از پودر فلزی درون الکترود، این روش میتواند بهنحوی باشد که از فرایندهای جوشکاری سنتی مثل جوشکاری MIG/MAG و جوشکاری تیگ استفاده میکند؛ اما از نظر کیفیت جوش و سرعت جوشکاری، بهتر عمل میکند.
مزایای جوشکاری قوسی توپودری
- سرعت بالا: این روش می تواند بهصورت مداوم جوش بزند و سرعت جوشکاری را افزایش دهد.
- اندازه جوشکاری: استفاده از الکترود پر شده باعث میشود تا بتوان در جوشکاریهای عمودی و افقی و حتی در موقعیتهای خاصی مانند جوشکاری سقفی نیز استفاده کرد.
- مقاومت بالا در برابر خوردگی: جوشکاری قوسی توپودری میتواند جوش هایی با خواص مقاومت بالا در برابر خوردگی تولید کند.
- کاربردهای گسترده: این روش در صنایع مختلفی مانند صنعت ساختوساز، صنعت خودروسازی، صنعت دریایی و… مورداستفاده قرار میگیرد.
تجهیزات جوشکاری قوسی توپودری (FCAW)
- منبع جوش: این شامل منبع تغذیه برق و دستگاه جوش است. در جوشکاری توپودری معمولاً از منبع جوشکاری قوسی با ولتاژ ثابت (DC) یا منبع جوشکاری قوسی با ولتاژ متغیر (AC) استفاده میشود.
- الکترود جوش: الکترودهای جوشکاری توپودری معمولاً شامل یک مهارکننده فلزی با پوشش پودر جوش هستند. پوشش پودر جوش شامل موادی است که باعث تولید گازهای محافظ و خاصیت پوششی روی حوضچه جوش میشوند.
- سیم فیدر: سیم فیدر یک دستگاه است که سیم جوش را بهصورت خودکار تغذیه میکند. این سیم جوش از طریق سیم فیدر به الکترود جوش متصل میشود و باعث تغذیه پودر جوش به الکترود میشود.
- دستگاه حفاظت گاز: در برخی از موارد، برای حفاظت از حوضچه جوش در جوشکاری توپودری از گازهای حفاظتی مانند آرگون یا مخلوطی از آرگون و دی اکسید کربن استفاده میشود. دستگاه حفاظت گاز، این گازها را بهصورت محافظ حول حوضچه جوش ارائه میدهد.
- لبه بردار: لبه بردار یا تمیزکننده سطح، برای تمیزکردن و آمادهسازی سطح جوش قبل از جوشکاری استفاده میشود. این ابزار میتواند شامل برس، دیسکهای سنگین، یا ابزارهای دیگری باشد که برای حذف آلودگیها و ایجاد سطحی صاف و تمیز استفاده میشوند.
جوشکاری اتمی هیدروژن چیست؟
جوشکاری اتمی هیدروژن یک فرایند جوشکاری است که در آن از انرژی تولیدشده توسط واکنش هستهای هیدروژن (معمولاً هیدروژن-دیوتریوم یا هیدروژن-تریتیوم) برای اتصال قطعات فلزی استفاده میشود. این فرایند از ترکیب انرژی هسته ای و توان جوشکاری که بهدلیل دمای بسیار بالا بهدست میآید، برای ایجاد اتصال قوی و محکم بین قطعات استفاده میکند.
در جوشکاری اتمی هیدروژن، انرژی هستهای در ناحیهای از فلزی که قرار است جوش داده شود، تولید می شود. این انرژی هستهای، باعث افزایش دما در ناحیه جوش میشود و باعث ذوب و اتصال قطعات فلزی به هم میشود. از آنجا که این فرایند به انرژی هستهای برای تولید گرما و جوش استفاده می کند، به آن «جوشکاری اتمی هیدروژن» گفته میشود.
مزایای جوشکاری اتمی هیدروژن
- کیفیت بالا: جوشکاری اتمی هیدروژن بهدلیل استفاده از گاز هیدروژن، باعث بهبود کیفیت جوش و خواص مکانیکی قطعات جوشکاری شده می شود. هیدروژن باعث کاهش میزان آلودگی هوای محیط و اکسیداسیون مواد فلزی میشود که نتیجه آن جوش با خواص مکانیکی بالا و عیب کمتر است.
- کارآیی بالا: استفاده از جوشکاری اتمی هیدروژن باعث افزایش سرعت و کارایی جوشکاری میشود. ترکیب هیدروژن با گازهای دیگر، امکان دستیابی به دمای بالا و سرعت جوشکاری بیشتر را فراهم میکند.
- عملکرد در دماهای بالا: یکی از مزایای جوشکاری اتمی هیدروژن این است که می توان در دماهای بالا جوشکاری را انجام داد. هیدروژن بهدلیل دارابودن نقطه جوش بسیار بالا (حدود ۲۵۰۰ درجه سانتی گراد)، امکان جوشکاری قطعاتی که نیاز به دماهای بالا دارند، فراهم میکند.
- کاهش میزان نفوذ آلایندهها: جوشکاری اتمی هیدروژن بهدلیل استفاده از محیط گازی، میزان نفوذ آلایندهها به مناطق جوشکاری را کاهش میدهد. این امر باعث کاهش نیاز به پاکسازی و پسجوشکاری بعد از جوشکاری می شود.
- محیط زیست و اقتصادی: جوشکاری اتمی هیدروژن بهدلیل کاهش آلایندهها و آسیب به محیط زیست کمتر، بهعنوان یک روش پایدار و دوستدار محیط زیست مطرح است. علاوبراین، با افزایش کارایی و کاهش هزینهها، از لحاظ اقتصادی نیز مزیت دارد.
جوشکاری قوسی کربنی (CAW) چیست؟
جوشکاری قوسی کربنی (CAW) به روشی اشاره دارد که در آن از قوس برقی برای ایجاد اتصالات میان قطعات فلزی استفاده می شود؛ اما با استفاده از گازهای بسیار خنککننده مانند هلیوم بهجای گازهای معمولی مانند آرگون. این روش برای جوشکاری فولادهای آلیاژی کربنی پیچیده مورداستفاده قرار میگیرد.
جوشکاری قوسی کربنی برای جوشکاری فولادهای آلیاژی با درصدهای کربن بالا که معمولاً در حدود ۰.۶ تا ۱.۵ درصد است، مناسب است. این فرآیند اغلب در صنایع نفتوگاز، صنایع خودروسازی و ساختوساز استفاده میشود.
با استفاده از جوشکاری قوسی کربنی، امکان جوشکاری قطعات فلزی با ضخامتها و شکلهای مختلف وجود دارد. همچنین، این روش قابلیت پیونددادن به فولادهای با کربن بالا را دارد و باعث ایجاد اتصالات با استحکام بالا و خواص مکانیکی مناسب میشود.
در جوشکاری قوسی کربنی، از منابع جوشکاری قوس الکتریکی مانند جوشکاری قوسی فلزی استفاده میشود. با اعمال جریان الکتریکی بین الکترود و قطعات فلزی، قوس برقی ایجاد میشود که میتواند دمای بسیار بالا را تولید کند.
درهمینحین، گازهای خنککننده مانند هلیوم در اطراف منطقه جوشکاری استفاده میشوند تا دمای منطقه جوشکاری را کاهش دهند و از اکسیداسیون و آلایش قطعات فلزی جلوگیری کنند.
جوشکاری قوسی کربنی یک فناوری پیشرفته و پیچیده است که تخصص و مهارت فنی بالایی برای اجرای صحیح آن نیاز دارد. علاوهبراین، مطالعه و اجرای روشهای مناسب برای کنترل دما و عوامل دیگر در جوشکاری قوسی کربنی بسیار مهم است تا اتصالات با کیفیت بالا و خواص مطلوب حاصل شود.
مزایای جوشکاری قوسی کربنی (CAW)
- سرعت بالا: جوشکاری قوسی کربنی بهدلیل امکان استفاده از جریان بالا، سرعت بالایی را برای اتمام عملیات جوشکاری فراهم میکند. این امر بهدلیل این است که جوشکاری CAW روی تمام ضخامتها امکانپذیر است و نیازی به استفاده از مواد اضافی ندارد.
- قابلیت جوشکاری انواع فلزات: جوشکاری قوسی کربنی میتواند روی انواع مختلف فلزات اعم از فولاد کربنی، فولاد ضدزنگ و آلیاژها اعم از آلومینیوم و مس انجام شود. این روش برای جوشکاری قطعات متفاوتی که از مواد مختلف ساخته شدهاند؛ بسیار مفید است.
- کیفیت بالا: جوشکاری قوسی کربنی باعث ایجاد جوش با کیفیت بالا و مقاومت مکانیکی قابل قبولی میشود. همچنین، زمانی که از فلزات با دماهای بالا استفاده میشود، خواص مکانیکی بهبود مییابد و ایجاد حرارت محدود می شود که باعث کاهش خطر تغییر ساختار فلزی میشود.
- عملیات ساده: جوشکاری قوسی کربنی نسبتبه روشهای دیگری مانند جوشکاری MIG و TIG کمترین نیاز را به آموزش و مهارت دارد. بهعلاوه، نیاز به تجهیزات پیچیده و هزینه بالا نیز کمتر است.
- کاربرد گسترده: جوشکاری قوسی کربنی در صنایع مختلفی از جمله خودروسازی، ساختوساز، تعمیرات صنعتی و تولید لولهها استفاده میشود. این روش برای اتصال قطعات فلزی بزرگ و تولید سازههای فلزی مناسب است.
تجهیزات جوشکاری قوسی کربنی (CAW)
- منبع برق: یک سیستم تأمین برق مورد نیاز برای ایجاد قوس الکتریکی استفاده میشود. این منبع برق میتواند از منابع مختلفی مانند باتریها، مولد جریان مستقیم (DC) یا مولد جریان متناوب (AC) تامین شود.
- الکترودها: دو الکترود با خاصیتهای مختلف استفاده میشوند. یک الکترود مثبت (آند) و یک الکترود منفی (کاتد) وجود دارد. جریان الکتریکی از الکترود مثبت به الکترود منفی جریان میکند و قوس الکتریکی را تشکیل میدهد.
- مواد پایه و جوش: فلزات مادرزادی که قرار است جوش داده شوند، در نقاط تماس خود آبشده میشوند و با خنکشدن اتصال جامد تشکیل میدهند. مواد پایه و جوش بستهبه نوع کاربرد و نیازهای جوشکاری ممکن است متفاوت باشند.
- سیستم خنککننده: بهدلیل دمای بالای قوس الکتریکی در جوشکاری قوسی کربنی، سیستم خنککننده برای خنککردن الکترودها و قطعات کار استفاده میشود. این سیستم معمولاً شامل یک پمپ خنککننده، مبدل حرارتی و یک مخزن آب است.
جوشکاری با پرتو لیزر (LBW) چیست؟
جوشکاری با پرتو لیزر (Laser Beam Welding یا به اختصار LBW) یک فرایند جوشکاری صنعتی است که در آن از پرتو لیزر برای اتصال قطعات فلزی استفاده میشود. در این فرایند، پرتو لیزر با تمرکز بالا و انرژی بالا روی یک منطقه کوچک از قطعات فلزی تابانده میشود.
انرژی لیزر، باعث ذوب و ذوب ناپذیرشدن قطعات فلزی میشود و با استفاده از این انرژی، قطعات با هم جوش میخورند. در جوشکاری با پرتو لیزر، پرتو لیزر از منابع لیزر قوی مانند لیزرهای فیبری، لیزرهای دیودی یا لیزرهای یاگ قدرتمند استفاده میشود. این پرتو لیزر بهصورت متمرکزشده و روی محل مورد نظر تابانده میشود.
تمرکز بالای انرژی لیزر باعث ایجاد یک لکه کوچک و شدیداً داغ در قطعات فلزی میشود که باعث ذوب و اتصال قطعات میشود. پس از تاباندن پرتو لیزر، قطعات تحت تأثیر نیروهای جوشکاری قرار میگیرند تا بخشهای ذوبشده به هم بچسبند و جامد شوند.
مزابای جوشکاری با پرتو لیزر (LBW)
- دقت بالا: پرتو لیزر بهطور دقیق بر روی منطقه مورد نظر تمرکز میشود و بههمیندلیل قابلیت دسترسی به نواحی دشوار و پیچیده را دارد.
- حرارت محدود: در این فرایند، حرارت به مناطق اطراف منتقل نمیشود و بههمیندلیل خطر آسیب به قطعات نزدیک به منطقه جوشکاری کمتر است.
- کنترل پارامترهای جوشکاری: با تنظیم قدرت و فاصله پرتو لیزر، میتوان بهطور دقیق کنترل دما و سرعت جوشکاری و برنامهریزی دقیقتری را در انجام جوشکاری داشت.
تجهیزات جوشکاری با پرتو لیزر (LBW)
- لیزر: انتخاب لیزر مناسب برای جوشکاری با پرتو لیزر بسیار مهم است. لیزرهای با توان و انرژی بالا معمولاً برای جوشکاری صنعتی استفاده میشوند.
- سیستم حوضچه و جدول: قطعات مورد جوشکاری روی سیستم حوضچه قرار میگیرند و توسط جدول محکمشده و در جای خود ثابت میمانند. این سیستمها باید بهمنظور تحمل حرارت و وزن قطعات مناسب باشند.
- سیستم تمرکز پرتو: پرتو لیزر باید بهطور دقیق روی نقطه جوشکاری تمرکز شود. سیستم تمرکز پرتو به این منظور طراحی شده است که بتواند پرتو را بهصورت دقیق روی نقطه مورد نظر تمرکز کند.
- سیستم تابش لیزر: این سیستم با استفاده از آینهها و عدسیها، پرتو لیزر را از منبع لیزر به سیستم تمرکز پرتو هدایت میکند.
- سیستم کنترل: یک سیستم کنترل پیچیده معمولاً برای کنترل پارامترهای جوشکاری مانند توان لیزر، سرعت جوشکاری و عمق حفره استفاده میشود.
- سیستم خنک کننده: بهدلیل ایجاد حرارت زیاد در فرآیند جوشکاری با پرتو لیزر، سیستم خنککننده برای خنککردن لیزر و تجهیزات مرتبط استفاده میشود.
جوشکاری غیر ذوبی چیست؟
جوشکاری غیر ذوبی یا جوشکاری فشاری، روشی است که در آن، اتصالات بین قطعات فلزی بهوسیلهی فشار، اصطکاک، امواج الکترو مغناطیسی یا گرما ایجاد میشود؛ اما ماده فلزی بهصورت مذاب نمیشود. در جوشکاری غیرذوبی، دما معمولاً زیر دمای ذوب نقطه مواد استفادهشده در اتصال قرار میگیرد.
مزیت اصلی جوشکاری غیرذوبی در مقایسه با جوشکاری ذوبی در این است که امکان استفاده از دماهای پایینتر و عدم نیاز به استفاده از مواد مذاب و مواد اضافی برای ایجاد اتصال وجود دارد. این روشها معمولاً برای جوشکاری قطعات با خواص مکانیکی خوب، عدم تغییر در ساختار میکروسکوپیک و حفظ ابعاد قطعات مناسب هستند.
بهعنوانمثال، در جوشکاری فرکشن، قطعات بهروشی مکانیکی در معرض فرکشن قرار میگیرند و با فشار و گرمای تولید شده به هم جوش میخورند. در جوشکاری اصطکاکی نیز، با استفاده از اصطکاک بین قطعه و ابزار جوشکاری، حرارت تولید شده موجب جوشکاری قطعات میشود.
جوشکاری غیرذوبی در صنایع مختلفی مانند خودروسازی، هواوفضا، ساختوساز و صنایع فلزی استفاده میشود. مزایای جوشکاری غیرذوبی شامل سرعت بالا، استفاده کمتر از حرارت و عدم تغییر ویژگیهای مکانیکی فلزات است. این روش برای اتصال قطعاتی با خواص مختلف و همچنین جوشکاری فلزاتی با نقاط ذوب پایین مفید است.
روشهای مختلفی برای جوشکاری غیر ذوبی وجود دارد که عبارتند از؛
- جوشکاری فراصوتی (UW)
- جوشکاری اصطکاکی (FW)
- جوشکاری مقاومتی (RW)
- جوشکاری انفجاری (EW)
جوشکاری التراسونیک یا فراصوتی (UW) چیست؟
جوشکاری التراسونیک یا فراصوتی (Ultrasonic Welding) یک فرایند جوشکاری است که در آن قطعات متصل را با استفاده از اصول اولتراسونیک به هم متصل میکند. در این روش، امواج صوتی با فرکانس بالا (بیشازحد صوت) از طریق قطعات قرار میگیرند و باعث ایجاد اصطکاک و انتقال حرارت بین سطوح متصل میشوند.
این انتقال حرارت به مقدار کافی برای ذوبشدن ناحیهای از قطعات منجر میشود و پس از خنکشدن و جامدشدن، قطعات به هم متصل میشوند. فرایند جوشکاری التراسونیک در بسیاری از صنایع، از جمله صنایع خودروسازی، الکترونیک، پزشکی، بستهبندی و تولید پلاستیک استفاده میشود.
مزایای جوشکاری التراسونیک یا فراصوتی (UW)
- سرعت بالا: جوشکاری التراسونیک فرایندی سریع است و می تواند در زمان کوتاهی قطعات را به هم متصل کند.
- عدم نیاز به مواد مصرفی: در این روش، هیچ نیازی به استفاده از مواد جوشکاری نظیر الکترودها یا لحیمها نیست.
- عدم تولید ذرات و گازهای مضر: در جوشکاری التراسونیک، هیچ ذرات مضر یا گازهای آلاینده تولید نمیشوند؛ بنابراین بهعنوان یک روش پاک و سبز شناخته میشود.
- اتصال قوی: جوشکاری التراسونیک بهدلیل ایجاد اصطکاک و اتصال مولکولی بین قطعات، اتصالات قوی و محکمی ایجاد میکند.
- قابلیت استفاده در قطعات ناهمسان: این روش قابلیت جوشکاری قطعات مختلفی با مشخصات متفاوت را دارد، از جمله قطعات ناهمسان و مختلف از نظر ضخامت و ماده ساختاری.
تجهیزات جوشکاری التراسونیک یا فراصوتی (UW)
- مولد التراسونیک: این تجهیز به امواج صوتی با فرکانس بالا نیاز دارد که توسط مولد تراسونیک تولید میشود. این مولد عموماً شامل یک ترانسدیوسر (تبدیلکننده انرژی) است که انرژی الکتریکی را به انرژی مکانیکی تبدیل میکند.
- هواپیمایی یا بوندر: قطعاتی که قرار است به هم جوش داده شوند، روی بوندر قرار میگیرند. بوندر نقش حفظ فشار و راهاندازی ارتعاشات را دارد.
- سونوترود: سونوترود در محل تماس با قطعات قرار میگیرد و امواج صوتی را به قطعات منتقل میکند. این ترد خارجی میتواند بهشکل استوانهای، مخروطی یا شکل دیگری باشد، بستهبه نیازهای جوشکاری.
- دستگاه فشار: قطعات با استفاده از دستگاه فشار به هم فشرده می شوند و جوش خود را شکل میدهند. دستگاه فشار باید قدرت کافی برای اعمال فشار لازم را داشته باشد.
جوشکاری اصطکاکی (FW) چیست؟
جوشکاری اصطکاکی (Friction Welding) یا بهاختصار FW، یک فرایند جوشکاری است که در آن قطعات فلزی بهوسیله اصطکاک و حرارت به هم متصل میشوند. در این فرایند، دو قطعه فلزی به هم فشرده میشوند و سپس بهصورت روان به یکدیگر نزدیک میشوند تا اصطکاک بین آنها تولید شود. اصطکاک موجب ایجاد گرما میشود و به تبدیل انرژی حرکتی به انرژی حرارتی منجر میشود.
با افزایش دما، قطعات فلزی به یکدیگر متصل میشوند و در نهایت در نقطه اتصالی سرد میشود و اتصال محکمی را تشکیل میدهند. بهدلیل اینکه در جوشکاری اصطکاکی نیازی بهاستفاده از مواد پر کاربرد نیست، میتوان انواع مختلف فلزات را بهیکدیگر جوش داد.
جوشکاری اصطکاکی برای اتصال قطعات با اندازهها و شکلهای مختلف استفاده میشود و بهطور گسترده در صنایع خودرو سازی، هواوفضا، ساختوساز، نفتوگاز و صنایع دیگر استفاده میشود.
این فرایند جوشکاری سریعتر و اقتصادیتر از بسیاری از روشهای جوشکاری سنتی است و میتواند بهکاهش زمان و هزینه تولید کمک کند. جوشکاری اصطکاکی در انواع مختلفی وجود دارد که عبارتند از؛
- جوشکاری اغتشاشی (FSW)
- جوشکاری دورانی یا چرخشی (FRW)
جوشکاری اغتشاشی (FSW) چیست؟
جوشکاری اغتشاشی (FSW) یا به انگلیسی «Friction Stir Welding» یک فرایند جوشکاری نوین است که برای اتصال قطعات فلزی بدون استفاده از فلز ذوبشده استفاده میشود. این فرآیند در دهه 1990 توسط محققان دانشگاه TWI (موسسه جوشکاری و تحقیقات مواد) در انگلستان توسعه یافت.
در جوشکاری اغتشاشی، قطعههای فلزی که قرار است جوش داده شوند، با استفاده از یک ابزار سیال و استوانه ای بهنام پین جوشکاری، تحت تاثیر نیروی فشار و حرکت گرداننده این ابزار قرار میگیرند. پین جوشکاری در مسیر حرکت، فشار و حرارت زیادی به قطعه اعمال میکند و باعث میشود دو قطعه فلزی به هم بچسبند.
در این فرایند، فلزها بهطور مکانیکی متحرک میشوند و در نتیجه نیازی به ذوبشدن فلزها نیست. این مزیت باعث میشود کیفیت جوش بسیار بالا و ضرر حرارتی واقعا کمتری نسبتبه روشهای جوشکاری سنتی داشته باشد.
جوشکاری اغتشاشی بهعنوان یک فرایند پیشرفته جوشکاری، در صنایع مختلفی از جمله خودروسازی، هواوفضا، ساختوساز، صنعت دریایی و صنایع نظامی استفاده میشود. این فرایند قابلیت جوشدادن مواد فلزی مختلف را دارد و میتواند قطعاتی را با شکلها و ضخامتهای متفاوت به هم متصل کند. همچنین، جوشکاری اغتشاشی امکان تعمیر قطعات جوشدادهشده را نیز فراهم میکند.
مزایای جوشکاری اغتشاشی (FSW)
- کاهش تأثیر حرارتی: در این روش، حرارت تنها به ناحیه جوش محدود میشود و از نرمشدن بیشازحد فلزات اطراف جلوگیری میکند. این ویژگی نیاز به گاز یا پودر حفاظتی را کاهش میدهد.
- کاهش فرایندهای پسپردازش: برخلاف روشهای سنتی که نیاز به عملیات تکمیلی مانند ماشینکاری و صیقلکاری دارند، جوشکاری اغتشاشی سطحی صاف و یکنواخت ایجاد میکند، در نتیجه زمان و هزینه تولید کاهش مییابد.
- استحکام بالا: این روش بدون ایجاد حوضه ذوب، اتصالهایی قوی و مقاوم در برابر تنشهای مکانیکی ایجاد میکند.
- امکان جوشکاری مواد دشوار: جوشکاری اغتشاشی امکان اتصال موادی مانند آلومینیوم، فولاد ضدزنگ، مس و آلیاژهای تیتانیوم را که در روشهای سنتی مشکلساز هستند، فراهم میکند.
- حفظ خواص مواد: ازآنجاییکه در این روش از حرارت قوس الکتریکی استفاده نمیشود، تغییرات مکانیکی و میکروساختاری در فلزات حداقل بوده است و این امر برای صنایع حساس مانند هوافضا اهمیت زیادی دارد.
- بهرهوری بالا: این فرایند سریع و کارآمد است و بهدلیل عدم نیاز به الکترود یا تمیزکاری بعد از جوشکاری، باعث کاهش زمان تولید میشود.
تجهیزات جوشکاری اغتشاشی (FSW)
جوشکاری اغتشاشی بهدلیل مزایای منحصربهفرد خود، به تجهیزات خاصی نیاز دارد که شامل موارد زیر است:
- دستگاه جوشکاری اغتشاشی: این دستگاه ابزار اصلی در فرایند FSW است و شامل پینی چرخان میشود که در اثر اصطکاک، اتصال بین قطعات را ایجاد میکند.
- تیغه جوشکاری: ابزار جوشکاری که معمولاً از آلیاژهای مقاوم ساخته میشود و برای ایجاد اغتشاش در ناحیه جوش مورداستفاده قرار میگیرد.
- ماشین CNC: در مواردی که نیاز بهدقت بالا باشد، از دستگاههای CNC برای کنترل حرکات و اجرای جوشکاری دقیق استفاده میشود.
- سیستم خنککننده: بهدلیل تولید گرمای زیاد در فرایند جوشکاری، از سیستمهای خنککننده (مانند آب یا هوا) برای جلوگیری از آسیب به قطعات استفاده میشود.
- دستگاههای مکانیکی کمکی: این تجهیزات برای کنترل موقعیت قطعات و تنظیم دقیق حرکات دستگاه جوشکاری بهکار میروند و دقت فرایند را افزایش میدهند.
جوشکاری دورانی یا چرخشی (FRW) چیست؟
جوشکاری چرخشی (Rotary Welding) یک روش جوشکاری است که در آن قطعاتی که باید به هم جوش داده شوند، در حالت چرخشی قرار میگیرند. در این روش، قطعات جوشدادهشده بهوسیله یک دستگاه چرخشی مانند خرید میز چرخشی یا دستگاه جوشکاری اتوماتیک که روی دستگاه چرخشی نصب شده است، قرار میگیرند.
سپس جوشکار بهصورت پیوسته و به اطراف قطعات چرخشی، جوش را میسازد. جوشکاری چرخشی برای جوشکاری قطعات استفاده میشود که دارای ساختار هندسی یا قوسی است و نیاز به جوش در اطراف آنها دارد.
این روش بهویژه در صنایعی مانند صنعت نفتوگاز، صنعت خودروسازی، ساختوساز، تولید لولهها و بسیاری از بخشهای صنعتی دیگر استفاده میشود. باتوجهبه اینکه این روش نیازمند دستگاه های خاصی است، هزینه بالایی برای راهاندازی و استفاده از آن وجود دارد. همچنین، مهارت و تخصص خاصی در استفاده از دستگاههای جوشکاری چرخشی موردنیاز است.
تجهیزات جوشکاری اغتشاشی (FSW)
جوشکاری اغتشاشی بهدلیل ویژگیهای منحصربهفرد خود، به تجهیزات خاصی نیاز دارد که شامل موارد زیر است:
- دستگاه جوشکاری اغتشاشی: این دستگاه نقش اصلی را در فرایند FSW ایفا میکند و شامل یک پین چرخان است که با ایجاد اصطکاک، اتصال قوی بین قطعات را فراهم میکند.
- تیغه جوشکاری: این ابزار که از آلیاژهای مقاوم ساخته شده، برای ایجاد اغتشاش و توزیع یکنواخت حرارت در ناحیه جوش استفاده میشود.
- ماشین CNC: در کاربردهایی که نیاز بهدقت بالا دارند، دستگاههای CNC برای کنترل دقیق حرکات و اجرای جوشکاری خودکار بهکار میروند.
- سیستم خنککننده: بهدلیل تولید حرارت بالا در این فرایند، از سیستمهای خنککننده مانند جریان آب یا هوا برای جلوگیری از آسیب به قطعات استفاده میشود.
- دستگاههای مکانیکی کمکی: این تجهیزات برای تنظیم موقعیت قطعات، تثبیت محل جوشکاری و افزایش دقت در حین عملیات بهکار میروند.
تجهیزات جوشکاری دورانی یا چرخشی (FRW)
- ماشین جوشکاری TIG دورانی: این ماشینها بهمنظور جوشکاری قطعاتی که در اطراف آنها باید یک دوران کامل انجام شود، استفاده میشوند. این ماشینها قادرند روی لولهها و سایر قطعات دورانی جوشکاری دقیق انجام دهند.
- دستگاه جوشکاری MIG/MAG دورانی: این دستگاهها برای جوشکاری قطعات دورانی با استفاده از فرایند جوشکاری MIG یا MAG استفاده میشوند. این فرایندها از الکترود پیچشی استفاده میکنند که باعث میشود جوشکاری روی قطعات دورانی انجام شود.
- دستگاه جوشکاری پلاسما دورانی: این دستگاهها از تکنولوژی جوشکاری پلاسما برای جوشکاری قطعات دورانی استفاده میکنند. این روش جوشکاری با استفاده از یک قوس پلاسمایی بین الکترود و قطعه کار انجام میشود.
جوشکاری مقاومتی (RW) چیست؟
جوشکاری مقاومتی (RW) مخفف عبارت Resistance Welding است. این روش جوشکاری، یکی از روشهای پرکاربرد در صنعت جوشکاری است که برای اتصال قطعات فلزی به یکدیگر استفاده میشود. در این روش، جرقهای بین قطعات فلزی ایجاد میشود که باعث ذوبشدن نقاط مخابره بین دو قطعه میشود و اتصالی محکم و دوام دار ایجاد میکند.
در جوشکاری مقاومتی، قطعات فلزی که قرار است جوش داده شوند، بین دو الکترود قرار میگیرند. الکترودها به منبع برق متصل میشوند و جریان الکتریکی از طریق قطعات فلزی جریان می یابند. بر اثر مقاومت الکتریکی قطعات فلزی، گرما به آنها منتقل میشود و نقاط مخابره بین قطعات ذوب میشوند. سپس فشاری به قطعات اعمال میشود تا در حالت جامد سرد شوند و اتصال محکمی بین قطعات ایجاد شود.
جوشکاری مقاومتی بهدلیل سرعت بالا، قابلیت اتصال قطعات با ضخامت مختلف، عدم نیاز به مواد افزودنی، عدم تولید چربی و بخار و همچنین کنترل آسان فرایند، در صنایع مختلفی از جمله خودرو سازی، الکترونیک، لوازم خانگی و صنایع فلزی استفاده میشود. جوشکاری مقاومتی در انواع مختلفی وجود دارند که عبارتند از:
- جوشکاری مقاومتی نقطه ای
- جوشکاری مقاومتی درز جوش (RSEW)
- جوشکاری مقاومتی زائده ای (RPW)
- جوش آپست
جوشکاری مقاومتی نقطه ای چیست؟
جوشکاری مقاومتی نقطهای (Spot Welding) یک روش جوشکاری است که در آن دو قطعه فلزی بهوسیله جریان الکتریکی و فشار فشرده به هم متصل میشوند. در این روش، قطعات فلزی به نقاط خاصی که جوشکاری میشوند، فشار داده میشوند و جریان الکتریکی بین این نقاط عبور میکند. با تأثیر جریان الکتریکی و فشار فشرده، نقاط تماس قطعات گرم و با یکدیگر یکپارچه میشوند.
برای انجام جوشکاری مقاومتی نقطه ای، از یک دستگاه جوشکاری مقاومتی نقطهای استفاده میشود. این دستگاه شامل دو الکترود است که روی قطعات فلزی قرار میگیرند و فشار به آن ها وارد میشود. الکترودها بهگونهای طراحی شدهاند که از بین هم متحرکند و برای هماهنگی با ضخامت قطعه، میتوانند تنظیم شوند.
در زمانی که الکترودها به قطعات فشرده میشوند، جریان الکتریکی از یک الکترود عبور میکند، از قطعات عبور و به الکترود دیگر باز میگردد. این جریان الکتریکی باعث ایجاد حرارت در نقاط تماس قطعات میشود و فلزات گرمشده را بهطور موقت ذوب میکند. پس از خنکشدن و ایجاد جامدشدن مجدد، نقاط تماس به یکدیگر متصل میشوند و جوش تشکیل میشود.
جوشکاری مقاومتی نقطه ای بهدلیل سرعت بالا و نیاز کمتر به نیروی دستی، در صنایع خودروسازی، صنعت فلزات و ساختوساز استفاده میشود. این روش برای اتصال قطعات فلزی با ضخامت کمتر مناسب است و میتواند در اتصالاتی که نیاز به ظاهر زیبا و قوی دارند، مؤثر باشد.
مزایای جوشکاری مقاومتی نقطه ای
- سرعت عمل: جوشکاری مقاومتی نقطه ای بسیار سریع انجام میشود و زمان کمی برای جوشکاری هر نقطه نیاز دارد. این امر باعث میشود فرآیند جوشکاری برای تولیدیهایی با ضریب نیروی کار بالا و زمان محدود مفید باشد.
- اتصال قوی: در جوشکاری مقاومتی نقطه ای، اتصال میان دو قطعه فلزی بسیار قوی و محکم است. با اعمال فشار و جریان بالا، دو قطعه فلزی بهطور محکم با هم جوش میخورند و اتصالی با مقاومت بالا و قابلیت انتقال جریان و حرارت خوب ایجاد میشود.
- عدم نیاز به مواد جانبی: در جوشکاری مقاومتی نقطهای، عموماً نیازی به استفاده از مواد جانبی مانند الکترود جوش نیست. این امر باعث کاهش هزینه و زمان مورد نیاز برای جوشکاری میشود.
- کارایی انرژی: در جوشکاری مقاومتی نقطه ای، انرژی مصرفی بسیار کمتر از روشهای جوشکاری دیگر مانند جوشکاری قوس الکتریکی است. این بهمعنای صرفهجویی در هزینههای انرژی و حفاظت از محیط زیست است.
- قابلیت اتصال انواع مختلف فلزات: جوشکاری مقاومتی نقطه ای قادر به اتصال انواع مختلفی از فلزات مانند فولاد، آلومینیوم و فولاد ضدزنگ است. این روش میتواند در بسیاری از صنایع مانند صنعت خودروسازی، صنعت لوازم خانگی و صنعت الکترونیک مورد استفاده قرار گیرد.
تجهیزات جوشکاری مقاومتی نقطه ای
- دستگاه جوشکاری مقاومتی نقطهای: این دستگاه شامل منابع تغذیه الکتریکی، الکترودها و سیستم کنترل جوش است. منابع تغذیه برق موردنیاز برای تولید جریان الکتریکی برای جوشکاری را فراهم میکنند. الکترودها بهعنوان محیط انتقال جریان بین قطعات فلزی عمل میکنند. سیستم کنترل جوش وظیفه کنترل پارامترهای جوشکاری، مانند جریان الکتریکی، زمان و فشار را دارد.
- الکترودها: الکترودها در جوشکاری مقاومتی نقطهای نقش بسیار مهمی دارند. الکترودها به دو نوع ثابت و دورانی تقسیم میشوند. الکترودهای ثابت در مواقعی استفاده میشوند که جزئیات دقیقتری برای قراردادن الکترود در نقاط مورد نظر وجود دارد، درحالیکه الکترودهای دورانی برای سرعت بالا و محلهای دسترسی دشوار مورد استفاده قرار میگیرند.
- سیستم خنککننده: در طول جوشکاری مقاومتی نقطهای، ممکن است الکترودها و قطعات فلزی گرم شوند. برای جلوگیری از افزایش دما و خنک شدن الکترودها، سیستم خنککننده استفاده میشود. این سیستم شامل یک منبع سردایی (معمولاً آب یا روغن) و یک سیستم پمپاژ برای گردش مایع خنککننده است.
- دستگاه فشار: جوشکاری مقاومتی نقطه ای نیازمند اعمال فشار مناسب روی قطعات فلزی است. برای این منظور، معمولاً از دستگاه فشار مجهز به سیستم هیدرولیک یا پنوماتیک استفاده میشود.
- سیستم کنترل: سیستم کنترل جوشکاری مقاومتی نقطهای نقش مهمی در کنترل پارامترهای جوشکاری و تضمین کیفیت اتصال دارد. این سیستم شامل کنترلرها، سنسورها و نمایشگرها است که به کاربر امکان کنترل و نظارت بر فرایند جوشکاری را میدهند.
جوشکاری مقاومتی درز جوش (RSEW) چیست؟
جوشکاری مقاومتی درز جوش (RSEW) یا Resistance Spot Welding به یک روش جوشکاری مقاومتی اشاره دارد که در آن، اجزای مختلف با استفاده از جریان الکتریکی و فشار متقابل به هم جوش داده میشوند. این روش جوشکاری بیشتر در صنایع خودروسازی، صنایع فلزی و ساختوساز استفاده میشود.
در روش جوشکاری مقاومتی درز جوش، دو تکه فلزی که قصد جوشکاری آنها را دارید، بین دو الکترود قرار میگیرند. الکترودها جریان الکتریکی با توان ولتاژ بالا را از خود عبور میدهند و در نقاط مشخصی روی سطح قرار گرفته، فشاری روی تکههای فلزی اعمال میکنند.
فشار متقابل همراه با جریان الکتریکی باعث ایجاد حرارت و ذوب نقاط تماس فلزی میشود. در نتیجه، فلزات ذوبشده با یکدیگر امتزاج میکنند و پس از خنکشدن، جوش درز ایجاد میشود. روش جوشکاری مقاومتی درز جوش برای اتصال قطعات فلزی با ضخامت کم استفاده میشود و میتواند بهصورت خودکار یا نیمه خودکار انجام شود.
این روش جوشکاری سریع و کارامد است و باعث ایجاد اتصالات قوی و مقاوم در برابر فشار، بارگذاری حرارتی و اثرات محیطی میشود. علاوهبراین، نیاز به مصرف جوشکاری ندارد و قطعات متصل به هم قابلیت جداشدن و مجدداً اتصالدادن را دارند.
استفاده از جوشکاری مقاومتی درز جوش (RSEW) بهدلیل سرعت بالا، کنترل دقیق و قابلیت اتصال قطعات فلزی با ضخامت کم، در صنایع مختلف بسیار رایج است.
مزایای جوشکاری مقاومتی درز جوش (RSEW)
جوشکاری مقاومتی درز جوش (RSEW) یکی از روشهای جوشکاری است که برای اتصال قطعات فلزی استفاده میشود. این روش دارای مزایای زیادی است که به شرح زیر است؛
- سرعت بالا: جوشکاری مقاومتی درز جوش یک روش سریع برای اتصال قطعات فلزی است. با استفاده از این روش، میتوان بهسرعت زیادی قطعات را به هم متصل کرد؛ این امر برای تولید انبوه قطعات و کاهش زمان تولید بسیار مهم است.
- کارایی بالا: با استفاده از جوشکاری مقاومتی درز جوش، اتصالات قوی و مقاومی بین قطعات فلزی تشکیل میشود. در این روش، جریان الکتریکی از طریق قطعات جوشکاریشده میگذرد و باعث ایجاد گرما و ذوب قسمتهایی از قطعات میشود. سپس با فشاردادن قطعات به هم، جوش تشکیل میشود.
- بهعلت استفاده از جریان الکتریکی، قطعات با سرعت بالا گرم میشوند و زمانی که جوش در حال تشکیل است، بهسرعت خنک میشوند. این امر باعث کاهش حداقلی تغییر شکل مواد و در نتیجه کاهش تنشهای باقیمانده در جوش میشود.
- هزینه کمتر: جوشکاری مقاومتی درز جوش هزینههای کمتری نسبتبه برخی از روشهای جوشکاری دیگر، مانند جوشکاری قوس الکتریکی دارد. علاوهبراین، این روش نیاز به تجهیزات ساده تری دارد که میتواند هزینها را به حداقل برساند.
- عدم نیاز به مواد جانبی: در جوشکاری مقاومتی درز جوش، معمولاً نیازی به استفاده از مواد جانبی نیست. در روشهایی مانند جوشکاری قوس الکتریکی، ممکن است نیاز به الکترود یا سیم جوش داشته باشید، اما در RSEW نیازی به مصرف مواد جانبی مانند این نیست.
- قابلیت استفاده در اتصال قطعات مختلف: جوشکاری مقاومتی درز جوش قابلیت استفاده در اتصال قطعات مختلف فلزی را دارا است. این روش برای اتصال قطعات با ضخامتهای متفاوت و حتی قطعات فلزی با ویژگیهای متفاوت کاربرد دارد.
تجهیزات جوشکاری مقاومتی درز جوش (RSEW)
تجهیزات مورد نیاز برای جوشکاری مقاومتی درز جوش شامل موارد زیر میشوند:
- ترانسفورماتور: این تجهیز از جریان بالا تغذیه میشود و ولتاژ و جریان را تا مقدار مورد نیاز برای جوشکاری تنظیم می کند.
- الکترودها: الکترودها برای ایجاد جریان الکتریکی و انتقال حرارت به قطعات فلزی استفاده میشوند. الکترودها معمولاً از مواد مقاومتی مانند مس یا آلیاژهای مس-کروم تهیه میشوند.
- کنترلکننده جریان: این دستگاه برای تنظیم جریان الکتریکی استفاده میشود. این کنترلکننده به ترانسفورماتور متصل میشود و جریان را به مقدار موردنیاز برای جوشکاری تنظیم میکند.
- سیستم خنککننده: هنگام جوشکاری، قطعات فلزی گرم میشوند و برای جلوگیری از آسیب به تجهیزات یا قطعات، سیستم خنککننده استفاده میشود. این سیستم معمولاً شامل یک مبدل حرارتی و یک منبع آب خنک است.
- سیستم کنترل دما: برای کنترل دمای جوشکاری و جلوگیری از ذوبشدن زیاد یا ضعیفشدن قطعات، سیستم کنترل دما استفاده میشود. این سیستم معمولاً شامل حسگرها و یک واحد کنترل است.
جوشکاری مقاومتی زائده ای (RPW) چیست؟
جوشکاری مقاومتی زائدهای یکی از روشهای جوشکاری الکتریکی است که در آن جریان الکتریکی بسیار بالا از طریق قطعات فلزی عبور و با ایجاد گرما، اتصال بین آنها را برقرار میکند. این فرایند عمدتاً در صنعت الکترونیک برای جوشکاری اتصالات الکتریکی بهکار میرود؛ اما در سایر صنایع نیز کاربرد دارد.
در این روش، قطعات موردنظر بین دو الکترود ویژه قرار میگیرد و به منبع تغذیه متصل میشوند. با عبور جریان، مقاومت الکتریکی قطعات موجب تولید گرما شده و اتصال محکمی ایجاد میکند.
کاربردهای جوشکاری مقاومتی زائدهای
- صنعت الکترونیک: اتصال پینها به بردهای مدارچاپی برای ایجاد اتصالات بادوام و رسانا.
- صنعت خودروسازی: جوشکاری قطعات فلزی در بدنه و اجزای خودرو.
- صنایع فلزی: اتصال قطعات کوچک فلزی که نیاز به جوشکاری دقیق و سریع دارند.
این روش علاوهبر استحکام بالای اتصالات، سرعت اجرای بالایی داشته و برای تولیدات انبوه گزینهای ایدهآل محسوب میشود.
مزایای جوشکاری مقاومتی زائده ای (RPW)
این روش بهعنوان یکی از روش های جوشکاری فلزات پیوسته استفاده میشود و دارای برخی مزایا است که عبارتند از:
- سرعت جوشکاری: RPW یکی از روشهای سریع جوشکاری است. با استفاده از این روش، میتوان قطعات را بهسرعت بالا جوش داد و زمان تولید را بهطور قابلتوجهی کاهش داد.
- اتصال قوی: جوشهای تولیدشده توسط RPW دارای اتصالات قوی هستند. در این روش، قطعات با هم فشرده میشوند و به هم جوش داده میشوند باعث ایجاد اتصالات محکم و قوی میشود.
- تغییر کم حرارتی: در RPW، حرارت تولیدشده در طول جوشکاری محدود است و بهسرعت از بین میرود. این ویژگی موجب می شود که تغییرات حرارتی در قطعه به حداقل برسد و اثر حرارتی روی خواص ماده کاهش یابد.
- عدم نیاز به ماده جوشکاری: در RPW، نیازی به استفاده از ماده جوشکاری مانند فلز روی، فلز فشاری یا فلز جوشکاری نیست. بدینترتیب، هزینه تهیه و استفاده از مواد جوشکاری کاهش مییابد.
- کنترل آسان: RPW دارای کنترل آسان است. با تنظیم پارامترهای مربوطه مانند جریان، زمان و فشار، میتوان کیفیت جوش را کنترل کرد و جوشهای با کیفیت بالا تولید کرد.
تجهیزات جوشکاری مقاومتی زائدهای (RPW)
- سیستم تامین برق: این سیستم شامل منبع تغذیه برقی است که برای ایجاد جریان بالا و فشار مورد نیاز در هنگام جوشکاری استفاده میشود. منابع تغذیه ممکن است شامل ترانسفورماتورهای قدرت و یا منابع برق سوئیچینگ باشند.
- الکترودها: در جوشکاری مقاومتی زائدهای، الکترودها برای ایجاد جریان بین قطعات فلزی استفاده میشوند. الکترودها باید قادر به تحمل جریان بالا و فشار مورد نیاز در هنگام جوشکاری باشند.
- قطعات فشار دهی: قطعات فشار دهی برای ایجاد فشار و اتصال محکم بین قطعات فلزی استفاده میشوند. این قطعات معمولاً شامل اجزای فلزی یا کربیدی هستند که مقاومت بالا در برابر فشار و استحکام حرارتی دارند.
- سیستم کنترل: سیستم کنترل برای کنترل جریان و فشار در هنگام جوشکاری استفاده میشود. این سیستم میتواند شامل کنترلرها، سنسورها و دستگاههای ایمنی باشد که برای مانیتورینگ و کنترل فرآیند جوشکاری استفاده میشوند.
جوشکاری آپست (Upset Welding – UW) چیست؟
جوشکاری آپست یکی از روشهای جوشکاری مقاومتی است که در آن قطعات فلزی تحتفشار به یکدیگر متصل و با عبور جریان الکتریکی، گرمای لازم برای ایجاد اتصال فراهم میشود. این فرایند بهدلیل استحکام بالا، دقت در کنترل پارامترهای جوش و عدم نیاز به مواد مصرفی اضافی، در صنایع مختلف کاربرد گستردهای دارد.
مکانیزم عملکرد جوش آپست
- فشردهسازی اولیه: دو قطعه فلزی در تماس با یکدیگر قرار گرفته و نیروی مکانیکی مشخصی به آنها اعمال میشود.
- اعمال جریان الکتریکی: جریان الکتریکی با شدت بالا از محل اتصال عبور و مقاومت الکتریکی در سطح تماس، گرمای لازم برای ایجاد جوش را فراهم میکند.
- ایجاد تغییر شکل پلاستیک: در اثر گرمایش موضعی، فلزات نرمشده و با حفظ فشار، ساختاری یکپارچه در محل جوش شکل میگیرد.
- خنکسازی و تثبیت اتصال: پس از قطع جریان، فشار همچنان حفظ میشود تا اتصال بهطور کامل شکل گیرد و استحکام نهایی حاصل شود.
ویژگیها و مزایای جوش آپست
- استحکام مکانیکی بالا: بهدلیل ایجاد یکپارچگی ساختاری در ناحیه جوش، این روش اتصالهای بسیار مقاومی تولید میکند.
- کاهش مصرف مواد و انرژی: عدم نیاز به مواد پرکننده و گازهای محافظ، این روش را از نظر اقتصادی و زیستمحیطی بهینه میکند.
- دقت و قابلیت کنترل بالا: امکان تنظیم دقیق پارامترهای جوشکاری مانند فشار، زمان و شدتجریان باعث بهبود کیفیت اتصال میشود.
- کاهش تغییرات متالورژیکی: با کنترل میزان حرارت ورودی، تغییرات نامطلوب در خواص مکانیکی و متالوژیکی قطعه به حداقل میرسد.
کاربردهای صنعتی جوش آپست
صنعت خودروسازی: جوشکاری اجزای شاسی، میللنگ، میلگردها و سایر قطعات حساس.
صنایع نفت و گاز: اتصال لولههای مقاوم در برابر فشار بالا و محیطهای خورنده.
ساختوساز و مهندسی عمران: تولید مقاطع فلزی با جوشهای مستحکم و بادوام.
تولید تجهیزات دریایی و هوافضا: ایجاد اتصالات مقاوم در برابر تنشهای دینامیکی و شرایط سخت محیطی.
مهندسی پزشکی: ساخت قطعات دقیق و مقاوم برای تجهیزات پزشکی و پروتزهای فلزی.
جوشکاری آپست یک روش پیشرفته، سریع و کارامد برای ایجاد اتصالات مستحکم در صنایع حساس است. بهدلیل کنترل بالا بر فرایند و کیفیت جوش، این روش جایگزین مناسبی برای برخی روشهای سنتی جوشکاری بوده است و در بخشهای صنعتی حیاتی مورداستفاده قرار میگیرد.
مزایای جوشکاری آپست (Upset Welding – UW)
جوشکاری آپست یکی از روشهای پیشرفته در صنعت جوشکاری است که با بهرهگیری از حرارت ناشی از مقاومت الکتریکی، قطعات فلزی را به هم متصل میکند. این روش بهدلیل ویژگیهای منحصربهفرد خود، کاربرد گستردهای در صنایع مختلف دارد.
۱. استحکام و دوام بالا
اتصالهای ایجادشده در جوشکاری آپست از استحکام مکانیکی بالایی برخوردارند و توانایی تحمل بارهای سنگین، ارتعاشات و تنشهای مکانیکی را دارند. این ویژگی باعث افزایش طول عمر و عملکرد قطعات متصلشده میشود.
۲. عدم نیاز به مواد مصرفی اضافی
در این فرایند، نیازی به استفاده از مواد پرکننده، الکترود، پیچومهره یا چسبهای صنعتی نیست. این مزیت باعث کاهش هزینههای مواد اولیه و افزایش بهرهوری در تولید میشود.
۳. سرعت بالا و افزایش راندمان تولید
جوشکاری آپست در مقایسه با بسیاری از روشهای دیگر، سرعت بیشتری دارد و امکان اجرای جوشکاری در زمان کوتاهتری را فراهم میکند. این ویژگی، باعث کاهش هزینههای عملیاتی و افزایش سرعت تولید در خطوط صنعتی میشود.
۴. امکان اتصال قطعات با ضخامتهای متفاوت
یکی از قابلیتهای مهم جوشکاری آپست، امکان اتصال قطعات فلزی با ضخامتهای مختلف است. این ویژگی در صنایعی که نیاز به ترکیب قطعات با اندازههای متفاوت دارند، مانند صنعت خودروسازی و ساخت قطعات مهندسی، اهمیت بالایی دارد.
۵. کاربرد گسترده در صنایع مختلف
این روش در صنایع خودروسازی، ساختمانسازی، صنایع دریایی، هوافضا، نفتوگاز و حتی صنایع پزشکی برای تولید قطعات دقیق و مقاوم استفاده میشود.
۶. انعطافپذیری در طراحی و مهندسی
جوشکاری آپست به مهندسان و طراحان این امکان را میدهد که اتصالات را در طرحهای پیچیده و ساختارهای متنوع اجرا کنند. این انعطافپذیری، طراحیهای خلاقانهتر و بهینهتری را در صنایع مختلف امکانپذیر میکند.
نکته مهم
جوشکاری آپست یک روش کارامد، سریع و اقتصادی برای ایجاد اتصالات مستحکم در صنایع حساس است. مزایایی مانند استحکام بالا، کاهش هزینهها، سرعت بالای جوشکاری و انعطافپذیری در طراحی، این روش را به یکی از گزینههای برتر در جوشکاری صنعتی تبدیل کرده است.
تجهیزات موردنیاز در جوشکاری آپست (Upset Welding – UW)
جوشکاری آپست برای اجرای صحیح و دستیابی به جوشهای باکیفیت، نیازمند تجهیزات تخصصی و دقیق است. در این روش، کنترل جریان الکتریکی، فشار و دما از اهمیت بالایی برخوردار است. در ادامه، مهمترین تجهیزات مورداستفاده در جوشکاری آپست معرفی شدهاند؛
منبع تغذیه جوشکاری
این دستگاه وظیفه تأمین جریان الکتریکی با شدت و ولتاژ مناسب را بر عهده دارد. جریان الکتریکی تولیدشده توسط این منبع، موجب ایجاد حرارت در سطح اتصال و فرایند ذوب موضعی فلزات میشود. منبع تغذیه باید دارای قابلیت تنظیم ولتاژ و جریان باشد تا بتوان جوشکاری را بادقت کنترل کرد.
الکترودهای جوشکاری
در جوشکاری آپست، الکترودها بهعنوان محل عبور جریان الکتریکی و ایجاد فشار روی قطعات عمل میکنند. این الکترودها معمولاً از موادی مانند فولاد ضدزنگ، فولاد کربنی یا آلیاژهای خاص ساخته میشوند تا استحکام و هدایت الکتریکی بالایی داشته باشند.
کنترلکنندههای جریان و ولتاژ (ولتمتر و آمپرمتر)
برای دستیابی به یک جوش یکنواخت و باکیفیت، اندازهگیری و کنترل دقیق میزان جریان و ولتاژ ضروری است. این تجهیزات به اپراتور اجازه میدهند که میزان انرژی ورودی را بهصورت دقیق تنظیم کند و از بروز عیوب جوش جلوگیری شود.
سیستم خنککننده
در حین جوشکاری، دمای الکترودها و قطعات افزایش مییابد که میتواند باعث آسیب یا تغییر شکل ناخواسته شود. سیستمهای خنککننده (آبی یا هوایی) به کاهش دمای الکترودها و سطح جوش کمک و از افزایش بیشازحد دما جلوگیری میکنند.
گیرهها و فیکسچرهای نگهدارنده
برای اطمینان از موقعیت صحیح قطعات در هنگام جوشکاری، از گیرههای مخصوص و فیکسچرها استفاده میشود. این ابزارها مانع از جابهجایی قطعات در حین جوشکاری و باعث یکنواختی و دقت در محل جوش میشوند.
ابزارهای آمادهسازی سطح (لبهزن و برسهای تمیزکاری)
قبل از انجام جوشکاری، سطوح اتصال باید بهخوبی آماده شوند تا از هرگونه آلودگی، زنگزدگی یا اکسیداسیون پاک شوند. برای این منظور، از لبهزنها، برسهای سیمی و دستگاههای سنگزنی استفاده میشود.
تجهیزات جوشکاری آپست شامل منبع تغذیه قوی، الکترودهای مناسب، ابزارهای اندازهگیری ولتاژ و جریان، سیستمهای خنککننده و تجهیزات نگهدارنده است. هر یک از این تجهیزات نقش کلیدی در کیفیت جوش نهایی ایفا میکنند و استفاده صحیح از آنها، منجر به بهبود استحکام، دقت و دوام اتصالات جوششده میشود.
جوشکاری انفجاری (Explosive Welding – EW) چیست؟
جوشکاری انفجاری (EW) یک روش جوشکاری پیشرفته و خاص است که در آن دو قطعه فلزی با استفاده از نیروی حاصل از یک انفجار شدید به یکدیگر متصل میشوند. این فرایند بدون ذوبشدن فلزات و تنها از طریق فشار بسیار زیاد ناشی از انفجار انجام میشود که باعث ایجاد اتصال متالورژیکی بین دو سطح فلزی میشود.
مکانیزم عملکرد جوشکاری انفجاری
۱. چیدمان قطعات: دو قطعه فلزی که قرار است به هم جوش داده شوند، بهصورت موازی یا در زوایای خاصی روی یکدیگر قرار میگیرند.
۲. استفاده از ماده انفجاری: یکلایه از مواد منفجره (مانند ترکیبات نیتروژنی) روی سطح قطعه بالایی قرار داده میشود.
۳. ایجاد انفجار: با یک تحریککننده، انفجار کنترلشدهای رخ میدهد که موج شوک شدیدی ایجاد و قطعه فوقانی را با سرعت زیاد بهسمت قطعه پایینی پرتاب میکند.
۴. ایجاد اتصال: در اثر برخورد با سرعت بالا، لایههای اکسیدی سطحی حذف شده و دو قطعه بهصورت مستقیم با هم تماس پیدا میکنند. در این نقطه، فشار بالا باعث ایجاد یک اتصال متالورژیکی بسیار قوی و بدون نیاز به ذوبشدن فلزات میشود.
ویژگیها و مزایای جوشکاری انفجاری
- امکان اتصال فلزات غیرهمجنس: این روش امکان جوشکاری فلزاتی را فراهم میکند که در روشهای جوشکاری سنتی بهدلیل تفاوت در نقطه ذوب و خواص شیمیایی، قابلاتصال نیستند (مانند جوشکاری آلومینیوم به فولاد یا مس به تیتانیوم).
- استحکام و مقاومت بالا: اتصالات ایجادشده در این روش دارای چسبندگی و استحکام مکانیکی بسیار بالایی هستند و در برابر تنشهای شدید، دماهای بالا و خوردگی مقاوماند.
- بدون ذوبشدن فلزات: بر خلاف روشهای دیگر، در جوشکاری انفجاری، فلزات ذوب نمیشوند؛ بنابراین تغییرات ساختاری ناخواسته در ماده پایه ایجاد نمیشود.
- قابلیت جوشکاری ورقهای بزرگ: این روش برای اتصال ورقهای فلزی در ابعاد و ضخامتهای مختلف کاربرد دارد.
کاربردهای جوشکاری انفجاری
- صنایع هوافضا: اتصال قطعات سبکوزن و مقاوم در برابر دماهای بالا.
- صنایع دریایی: تولید ورقهای چندلایه مقاوم در برابر خوردگی برای بدنه کشتیها.
- صنایع نفتوگاز: تولید مبدلهای حرارتی و لولههای مقاوم در برابر فشار بالا.
- صنایع خودروسازی: تولید قطعات مستحکم و سبک برای افزایش ایمنی و کاهش وزن خودرو.
جوشکاری انفجاری یکی از روشهای خاص و پیشرفته جوشکاری است که امکان اتصال فلزات غیرهمجنس را فراهم میکند. این روش با استفاده از نیروی حاصل از انفجار، بدون نیاز به ذوبشدن فلزات، اتصالاتی با استحکام بالا و مقاومت عالی در برابر شرایط سخت ایجاد میکند. بهدلیل مزایای منحصربهفرد، جوشکاری انفجاری در صنایع حساس و پیشرفته کاربرد گستردهای دارد.
مزایای جوشکاری انفجاری (Explosive Welding – EW)
جوشکاری انفجاری یکی از روشهای خاص جوشکاری است که بهدلیل ویژگیهای منحصربهفرد خود در صنایع پیشرفته مورداستفاده قرار میگیرد. در ادامه، مهمترین مزایای این روش را بررسی میکنیم؛
اتصال فوقالعاده قوی و مقاوم
- جوشکاری انفجاری باعث ایجاد اتصالاتی بسیار محکم و بادوام بین فلزات میشود.
- مقاومت بالا در برابر نیروهای مکانیکی، لرزشها و فشارهای شدید.
- کاهش احتمال ترکخوردگی یا جدایش در محل اتصال.
عدم نیاز به مواد مصرفی اضافی
- در این روش نیازی به الکترود، سیم جوش یا مواد فیلر نیست.
- کاهش هزینههای مواد مصرفی و صرفهجویی در فرایند جوشکاری.
ایجاد اتصالات خالص و بدون آلودگی
- این روش هیچ ناخالصی، اکسیداسیون یا آلودگی در محل جوش ایجاد نمیکند.
- حفظ خواص مکانیکی و شیمیایی فلزات پایه.
- بهویژه در صنایعی که نیاز به استانداردهای دقیق دارند، مانند صنایع هوافضا و پزشکی، بسیار مهم است.
امکان اتصال فلزات غیرهمجنس
- برخلاف روشهای سنتی، جوشکاری انفجاری امکان اتصال فلزات مختلف (مانند آلومینیوم به فولاد یا مس به تیتانیوم) را فراهم میکند.
- این ویژگی، این روش را برای تولید قطعات چندلایه و ترکیبی ایدهآل میکند.
عملکرد عالی در شرایط سخت و محیطهای دشوار
- جوشکاری انفجاری میتواند در محیطهایی با دمای بالا، فشار زیاد و شرایط خشن صنعتی انجام شود.
- کاربرد ویژه در صنایع دریایی، نفت و گاز، و تجهیزات تحتفشار.
تجهیزات ساده و هزینههای پایینتر
- برخلاف برخی روشهای جوشکاری پیچیده، تجهیزات جوشکاری انفجاری به نسبت ساده و کمهزینهتر هستند.
- نیاز کمتر به سیستمهای کنترل پیچیده و تجهیزات اضافی.
افزایش سرعت فرایند جوشکاری
- فرایند جوشکاری در مدتزمان بسیار کوتاهی انجام میشود.
- کاهش زمان تولید و افزایش بهرهوری در صنایع بزرگ.
جوشکاری انفجاری بهدلیل استحکام بالا، عدم نیاز به فیلر، امکان اتصال فلزات غیرهمجنس و عملکرد عالی در شرایط سخت، یکی از روشهای جوشکاری منحصربهفرد و پرکاربرد است. این روش بهویژه در صنایع پیشرفته مانند هوافضا، کشتیسازی و تجهیزات صنعتی تحتفشار نقش مهمی ایفا میکند.
تجهیزات جوشکاری انفجاری (EW)
جوشکاری انفجاری شامل مجموعهای از تجهیزات تخصصی است که برای ایجاد پیوندهای متالورژیکی از طریق تخلیه الکتریکی و انرژی انفجاری بهکار میروند. این تجهیزات عبارتند از:
- ماشین جوشکاری انفجاری: این دستگاه شامل منبع تغذیه الکتریکی است که انرژی لازم برای تخلیه الکتریکی را تأمین میکند. اجزای اصلی آن شامل ترانسفورماتورها، کویلها، سیستمهای قطبش و کنترل الکتریکی است.
- الکترودها: الکترودها برای ایجاد تخلیه الکتریکی و انتقال انرژی به سطح قطعات کار استفاده میشوند. این الکترودها به ماشین جوشکاری متصل میشوند و بسته بهنوع کاربرد، ممکن است بهصورت نوار، سیم یا سوپاپ باشند.
- قطعات کار: موادی که تحت فرایند جوشکاری قرار میگیرند باید از مقاومت کافی در برابر شوکهای الکتریکی و حرارتی برخوردار باشند. معمولاً از فلزاتی مانند فولاد، آلومینیوم و آلیاژهای خاص در این فرایند استفاده میشود.
- سیستم خنککننده: در حین جوشکاری انفجاری، قطعات و الکترودها بهشدت گرم میشوند. بههمیندلیل، یک سیستم خنککننده برای کاهش دما و جلوگیری از آسیب به تجهیزات و مواد مورداستفاده قرار میگیرد.
جوشکاری زیر آب چیست؟
جوشکاری زیر آب فرایندی است که در آن عملیات اتصال و تعمیر قطعات فلزی در محیط آبی انجام میشود. این فرایند توسط جوشکاران حرفهای و آموزشدیدهای انجام میشود که با استفاده از تجهیزات ویژه و مهارتهای فنی خاص، قادر به اجرای جوشکاری در شرایط زیر آب هستند.
برخلاف جوشکاریهای معمول که در محیطهای خشک انجام میشوند، در جوشکاری زیر آب چالشهایی مانند فشار آب، کاهش سریع دما و تماس مستقیم با آب باید در نظر گرفته شود. برای مثال، گرمای تولیدشده در این نوع جوشکاری بهسرعت توسط آب جذب میشود که میتواند بر کیفیت و خواص مکانیکی جوش تأثیر بگذارد.
از کاربردهای رایج جوشکاری زیر آب میتوان به تعمیر و نگهداری سازههای دریایی مانند کشتیها، سکوهای نفتی، خطوط لوله انتقال نفتوگاز، سدها و تأسیسات زیرآبی اشاره کرد. این فناوری همچنین در صنایع دریایی، زیردریاییسازی و تحقیقات اقیانوسی نیز مورداستفاده قرار میگیرد.
استفاده از جوشکاری زیر آب، نهتنها موجب افزایش سرعت و کارایی در تعمیرات میشود،؛ بلکه هزینههای مربوط به خشککردن و آمادهسازی محیط را کاهش میدهد و از نظر اقتصادی نیز مقرونبهصرفه است.
مزایای جوشکاری زیر آب
جوشکاری زیر آب مزایای متعددی دارد که آن را به یک روش کاربردی و کارآمد در صنایع دریایی و زیرآبی تبدیل کرده است؛
- حفظ کیفیت و عملکرد جوش: این روش باعث کاهش تنشهای حرارتی و جلوگیری از اکسیداسیون و آلودگی جوش میشود. عدم تماس مستقیم با هوا، کیفیت جوش را بهبود بخشیده و از زنگزدگی و تخریب جلوگیری میکند.
- کاهش دما و تنشهای حرارتی: آب بهعنوان یک محیط خنککننده طبیعی عمل کرده و از افزایش بیش از حد دمای جوش جلوگیری میکند. این امر موجب کاهش تغییرات حرارتی و کاهش احتمال ایجاد ترک و تغییر در خواص مکانیکی جوش میشود.
- کنترل دقیق پارامترهای جوشکاری: در جوشکاری زیر آب، میزان خنکشدن و سرعت آن بهطور دقیق قابلتنظیم است. این ویژگی امکان کنترل بهتر روی فرایند جوشکاری و کیفیت نهایی را فراهم میکند.
- کاهش خطرات ایمنی: این روش خطراتی مانند آتشسوزی، انفجار، انتشار دودهای سمی و سایر آلایندههای جوشکاری را به حداقل میرساند که در محیطهای بسته یا مناطق حساس ایمنی، یک مزیت مهم محسوب میشود.
- امکان جوشکاری در محیطهای آبی: جوشکاری زیر آب امکان انجام تعمیرات و ساخت سازههای فلزی را در محیطهایی مانند دریا، رودخانه و استخر فراهم میکند. این ویژگی برای صنایع دریایی، تأسیسات نفتوگاز و تعمیرات زیرآبی بسیار ارزشمند است.
تجهیزات جوشکاری زیر آب
جوشکاری زیر آب نیازمند تجهیزات خاصی است که بتوانند در شرایط زیر آب عملکرد بهینه داشته باشند. در اینجا برخی از این تجهیزات ذکر شده است؛
- الکترودهای زیر آب: الکترودهایی که در جوشکاری زیر آب استفاده میشوند باید ویژگیهای خاصی داشته باشند. این الکترودها باید در برابر آب مقاوم و قادر به انتقال جریان الکتریکی در محیط آبی باشند.
- منبع تغذیه: برای تولید جریان الکتریکی موردنیاز در جوشکاری زیر آب، از منابع تغذیه ویژهای استفاده میشود. این منابع باید ضدآب و توانایی مقاومت در برابر شرایط محیطی زیر آب را داشته باشند.
- سیستم خنککننده: بهدلیل حرارت تولید شده در حین جوشکاری، نیاز به سیستمهای خنککننده برای حفظ عملکرد صحیح تجهیزات وجود دارد. این سیستمها ممکن است شامل پمپهای خنککننده، مبدلهای حرارتی و مخازن آب باشند.
- محافظ حفاظتی: برای حفاظت از جوشکار و تجهیزات در برابر شرایط محیطی و آب، از پوششهای حفاظتی خاص استفاده میشود. این پوششها میتوانند شامل لباسهای ضدآب، عینکهای حفاظتی و دستکشهای مخصوص باشند.
- سیستم نگهدارنده قطعات: برای نگهداری قطعات در موقعیت دقیق حین جوشکاری، از سیستمهای خاص نگهدارنده استفاده میشود. این سیستمها میتوانند شامل مغناطیسها، فشارهای هیدرولیکی یا پنوماتیکی و دیگر سیستمهای مکانیکی باشند.
جوشکاری سربالا چیست؟
جوشکاری سربالا (Overhead welding) فرایندی است که در آن قطعات فلزی یا جوشها در موقعیتهایی قرار دارند که جوشکار برای دسترسی به آنها باید بالای سرخود کار کند. این نوع جوشکاری معمولاً در مواردی استفاده میشود که قطعات و سازههای بزرگ و پیچیده وجود دارند و جوشکار باید برای جوشدادن، به نواحی بالای سر دسترسی داشته باشد.
این وضعیت در سازههایی مانند سقفها، تونلها، کانالهای هوا، پلها و سایر سازههای بلند و در دسترسنبودن رخ میدهد. در جوشکاری سربالا، جوشکار باید در موقعیتی قرار گیرد که بتواند ابزارهای جوشکاری را بهدرستی روی قطعه قرار دهد و از بالای سرخود کار کند. این کار چالشهایی مانند دسترسی محدود، شرایط کاری ناامن و دید محدود را برای جوشکار بههمراه دارد.
بنابراین، برای انجام جوشکاری سربالا، داشتن تجهیزات ایمنی مناسب و همچنین آموزشهای تخصصی در این زمینه ضروری است. جوشکاری سربالا نیازمند مهارت و تجربه بالا در جوشکاری است و جوشکار باید با روشهای ایمنی و استفاده صحیح از تجهیزات آشنایی کامل داشته باشد.
مزایای جوشکاری سربالا
جوشکاری سربالا یکی از روشهای مؤثر برای اتصال قطعات فلزی است که در بسیاری از صنایع کاربرد دارد. این روش مزایای زیادی دارد که در ادامه به برخی از آنها اشاره میشود؛
- استحکام بالا: جوشکاری سربالا میتواند اتصالات بسیار قوی و مقاوم ایجاد کند. با استفاده از تکنیکهای مناسب، اتصالات جوشکاریشده قدرت کششی و تحمل بار بالایی خواهند داشت.
- انعطافپذیری: این روش در انواع فلزات و ضخامتهای مختلف قابلاستفاده است. جوشکاری سربالا امکان ایجاد اتصالات در ابعاد و ضخامتهای متنوع را فراهم میآورد.
- کارایی بالا: جوشکاری سربالا روشی سریع و کارامد است. این فرایند زمان کمتری برای تکمیل اتصالات نیاز دارد و با استفاده از تجهیزات مناسب، میتوان آن را بهصورت خودکار و پیوسته انجام داد.
- کنترل کیفیت: جوشکاری سربالا امکان کنترل دقیق کیفیت اتصالات را فراهم میکند. از روشهای بازرسی غیرمخرب مانند آزمونهای رادیوگرافی میتوان برای اطمینان از کیفیت و تطابق اتصالات با استانداردهای فنی استفاده کرد.
- کاربرد گسترده: جوشکاری سربالا در صنایع مختلفی مانند خودروسازی، ساختمان، دریایی، هوافضا، نفتوگاز و سایر صنایع کاربرد دارد. بهدلیل مزایای متعدد، این روش یکی از روشهای پرکاربرد برای اتصال قطعات فلزی است.
جوشکاری برق چیست؟
جوشکاری برق یک فرآیند صنعتی است که برای اتصال دو قطعه فلزی یا آلیاژ فلزی با استفاده از جریان الکتریکی، حرارت و فشار صورت میگیرد. در این روش، جوشکار با استفاده از سیمهای جوشکاری یا الکترودهای خاص، جریان الکتریکی بین دو قطعه فلزی ایجاد میکند. این جریان الکتریکی باعث ایجاد حرارت شدید در محل اتصال قطعات میشود که سبب ذوب شدن بخشهای مورد نظر و اتصال دائمی آنها میشود.
کاربردها و مزایای جوشکاری برق
جوشکاری برق بهدلیل سرعت بالا، کارآیی، و توانایی اتصال قطعات با ضخامتهای مختلف و از جنسهای متنوع، در صنایع مختلف کاربرد گستردهای دارد. از جمله صنایعی که از این روش بهره میبرند میتوان به خودروسازی، ساختوساز، صنایع فلزی، نفت و گاز، و صنایع الکترونیکی اشاره کرد.
ویژگیهای مهم جوشکاری برق
- تنوع در استفاده: جوشکاری برق میتواند برای جوشدادن انواع فلزات و آلیاژها استفاده شود.
- اتصال محکم: این فرایند اتصال مقاوم و با استحکام بالا بین قطعات ایجاد میکند.
- سرعت بالا: بهدلیل سرعت بالای این روش، در صنایع تولیدی بهویژه در مواردی که سرعت در فرآیند مهم است، بهطور وسیع استفاده میشود.
انواع الکترودها و تجهیزات
در جوشکاری برق از انواع مختلفی از الکترودها و تجهیزات استفاده میشود که انتخاب صحیح آنها بستهبه نوع قطعه و نیاز پروژه از اهمیت بالایی برخوردار است.
ایمنی در جوشکاری برق
بهدلیل شرایط خاص فرآیند جوشکاری برق و خطرات ناشی از برق، حرارت و دود، رعایت نکات ایمنی و استفاده از تجهیزات حفاظتی از اهمیت ویژهای برخوردار است.
این فرآیند از کاربردیترین و موثرترین روشها برای اتصال قطعات فلزی است که در صنایع مختلف بهطور گسترده مورد استفاده قرار میگیرد.
مزایای جوشکاری برق
جوشکاری برق بهعنوان یک روش اتصال قطعات فلزی دارای مزایای زیادی است که به برخی از آنها در زیر اشاره شده است؛
- اتصال قوی: جوشکاری برق اتصال بسیار مقاومی ایجاد میکند که در سازهها و تجهیزات نیازمند استحکام بالا، مانند سازههای فلزی و وسایل نقلیه، کاربرد دارد.
- تنوع وسایل قابل جوشکاری: این روش قابلیت جوشکاری انواع فلزات همچون فولاد، آلومینیوم، استیل و همچنین برخی قطعات غیرفلزی مانند پلاستیک و سرامیک را دارد.
- سرعت اجرا: جوشکاری برق بهدلیل سرعت بالای انجام آن در مقایسه با سایر روشها، گزینهای مقرونبهصرفه برای تولید انبوه و صنعتی بهشمار میآید.
- عملکرد در شرایط مختلف: جوشکاری برق قادر به عملکرد در شرایط دشوار از جمله دما و فشار بالا، زیر آب، فضا یا حتی در محیطهای خطرناک است.
- قابلیت تعمیر: در صورت نیاز به تعمیر قطعات جوشکاری شده، میتوان آنها را دوباره با جوشکاری برق تعمیر کرده یا اتصالات جدید ایجاد کرد.
- کاربردهای وسیع: این روش در صنایع مختلف از جمله خودروسازی، ساختمانسازی، تولید لوازمخانگی، صنایع دریایی، هوافضا و بسیاری دیگر بهکار میرود.
- کنترل کیفیت: با استفاده از تجهیزات پیشرفته، جوشکاری برق امکان کنترل دقیق کیفیت اتصالات را فراهم میآورد و میتواند عملکرد و کیفیت جوشها را بهطور مؤثری بهبود بخشد.
این مزایا باعث شده است که جوشکاری برق یکی از پرکاربردترین روشها در صنایع مختلف باشد و گزینهای ایدهآل برای اتصال قطعات فلزی محسوب شود.
جمعبندی آنچه مطالعه کردید…
در این مقاله با انواع جوشکاریها آشنا شدید و دانستید هر کدام چه مزایایی دارند. همچنین با تجهیزات هر یک از این جوشکاریها آشنا شدید. امید است این مطلب برای شما مفید واقع شده باشد و بتوانید از آن نهایت استفاده را ببرید.