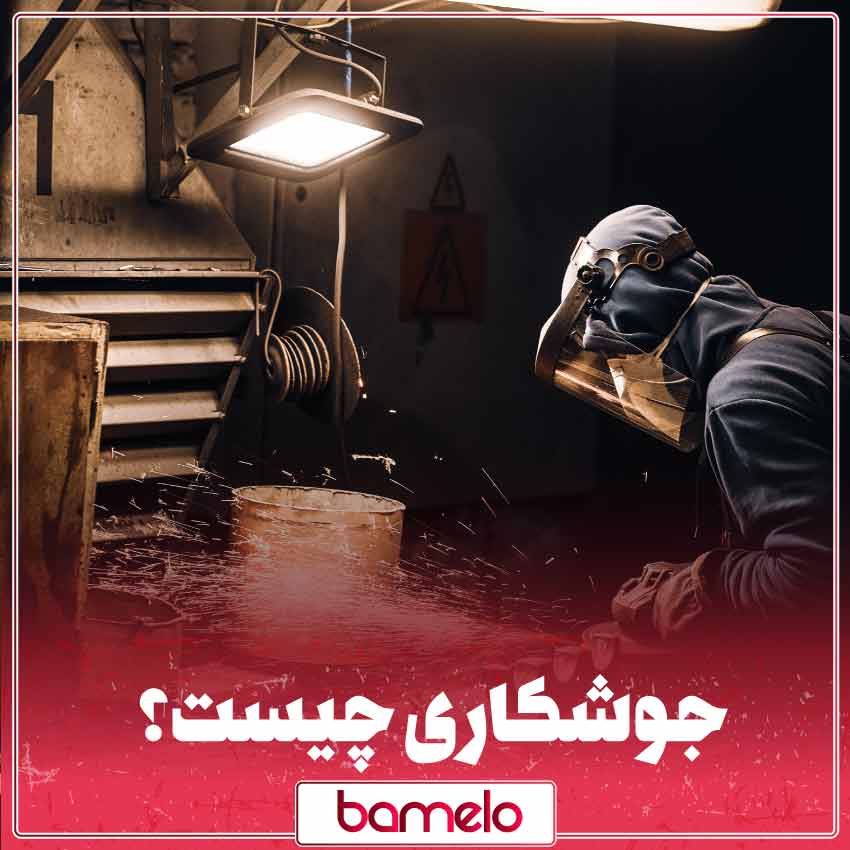
جوشکاری چیست؟
جوشکاری یا جوش دهی یک فرایند صنعتی است که در آن اجزای مختلف متصل و متحد شده و به هم وصل می شوند. این فرایند شامل استفاده از حرارت، فشار، جریان الکتریکی و یا مواد شیمیایی است که باعث ایجاد اتصال قوی و ماندگاری بین اجزا می شود.
جوشکاری در انواع مختلفی از صنایع استفاده می شود، از جمله صنایع خودرو سازی، ساخت و ساز، ساختمانی، لوله کشی، دریایی، هوا و فضا، صنایع فلزی و بسیاری صنایع دیگر. این فرایند از نظر فنی به دسته بندی های مختلفی تقسیم می شود.
هر یک از این روش ها برای شرایط خاصی و با توجه به نیاز های مختلف انتخاب می شود. جوشکاری می تواند به صورت دستی با استفاده از ابزار های ساده یا به صورت خودکار با استفاده از ماشین آلات پیشرفته انجام شود.
در جوشکاری، قطعات فلزی به هم فشرده و سپس در نقاط تماس با استفاده از حرارت و فشار، جوش می خورند. این حرارت می تواند از منابع مختلفی مانند له شدن فلز، استفاده از لحیم کاری، یا استفاده از قوس الکتریکی تولید شود. همچنین برای جوشکاری ممکن است از گاز های محافظ استفاده شود تا از تماس قطعات با هوا جلوگیری شود و کیفیت جوشکاری بهبود یابد.
از آنجایی که دکل ها هم در انواع مختلفی وجود دارند، هر دکل جوشکاری مخصوص به خود را دارد. انتخاب جوشکاری مناسب برای دکل مهاری به عوامل مختلفی وابسته است. در این مقاله با بهترین نوع جوشکاری دکل مهاری و بهترین نوع جوشکاری دکل منوپل آشنا می شوید. پس در این مقاله همراه ما باشید.
مزایای جوشکاری
مزایای جوشکاری عبارت اند از:
- ایجاد اتصال قوی و ماندگار بین اجزا
- امکان اتصال اجزا با شکل ها و اندازه های مختلف
- قابلیت اتصال مواد مختلف با یکدیگر
- کارآیی بالا و سرعت بالا در انجام عملیات
- عدم نیاز به استفاده از اتصالات جداگانه مانند پیچ و مهره
با این حال، جوشکاری همچنین ممکن است مشکلاتی همچون تغییر خواص مکانیکی مواد، تغییر شکل قطعات و مشکلاتی مرتبط با حرارت و تنش ایجاد کند. برای رفع این مشکلات، فرآیند های پس از جوشکاری مانند تغذیه، حمله، سخت کاری و آزمون های غیر مخرب نیز استفاده می شوند.
انواع جوشکاری کدامند؟
جوشکاری در انواع مختلفی وجود دارد. به طور کلی به دو دسته ذوبی و غیر ذوبی تقسیم می شود. هر کدام از این دو دسته، زیر مجموعه های مرتبط با خود را دارد که در ادامه با آن ها آشنا می شوید. منبع
جوشکاری ذوبی چیست؟
جوشکاری ذوبی (Fusion Welding) یا جوشکاری ذوب، یکی از روش های اصلی جوشکاری است که در آن قطعات فلزی با استفاده از گرما و ذوب شدن قسمت های مورد نظر به یکدیگر متصل می شوند.
در جوشکاری ذوبی، مواد پایه فلزی را با استفاده از یک منبع حرارتی، مانند قوس برقی یا لیزر، به دما های بالا تر از نقطه ذوب خود رسانده و سپس پس از ذوب شدن، قطعات فلزی را به هم متصل می کنند.
از جوشکاری ذوبی در صنایع مختلفی مانند صنعت خودرو سازی، صنعت دریایی، صنعت هوا و فضا، صنعت نفت و گاز و صنایع ساختمانی استفاده می شود. این روش برای اتصال قطعات فلزی با اندازه و شکل مختلف بسیار کارآمد است و اتصالاتی با استحکام بالا و تراکم بالا ایجاد می کند. انواع مختلف جوشکاری ذوبی عبارت اند از:
- جوشکاری با پرتوی الکترونی (Electron beam welding)
- جوشکاری اکسی گاز (Oxy fuel welding)
- جوشکاری قوسی (Arc welding)
- جوشکاری با پرتو لیزری (Laser beam welding)
جوشکاری با پرتو الکترونی (EBW) چیست؟
جوشکاری با پرتو الکترونی (EBW) یک فرایند جوشکاری است که در آن از پرتو های الکترونی برای ایجاد اتصالات جامد بین قطعات فلزی استفاده می شود. در این فرایند، الکترون ها با سرعت بالا به عنوان یک پرتو تمرکز شده ارسال می شوند و در نقطه مورد نظر بر روی قطعه تابیده می شوند.
این الکترون ها در اثر برخورد با قطعه، انرژی خود را از دست می دهند و این انرژی تبدیل به گرما می شود. وقتی پرتو الکترونی بر روی قطعه تابیده می شود، انرژی حرکتی الکترون ها به صورت حرارت منتقل می شود و باعث محلول شدن و ذوب شدن قسمتی از قطعه می شود. سپس، قطعه ها به هم فشرده می شوند و جوشکاری نهایی انجام می شود.
این روش معمولاً برای جوشکاری قطعات فلزی پیچیده، اتصالاتی با شکل ها و ضخامت های مختلف و همچنین در برخی موارد برای جوشکاری فلزات با خواص خاص مورد استفاده قرار می گیرد.
مزایای جوشکاری با پرتو الکترونی (EBW)
این روش جوشکاری به دلایل زیر مزایای قابل توجهی دارد:
عمق نفوذ بالا: پرتو الکترونی دارای نیروی حرارتی بالا است و قادر به نفوذ به عمق های بزرگی در مقایسه با روش های دیگر جوشکاری است. این عمق نفوذ بالا به ویژه در جوشکاری قطعات ضخیم و چند لایه بسیار مفید است.
ذوب کنندگی کمتر: پرتو الکترونی قطعات را با استفاده از حرارت تولید شده از ایجاد الکترون های پرانرژی در جوشکاری می تواند ذوب کند. این روش می تواند به کاهش تغییرات ابعادی و تغییرات مورفولوژیکی که در روش های دیگر جوشکاری اتفاق می افتد، کمک کند.
عملکرد با دقت بالا: جوشکاری با پرتو الکترونی دقت بالایی در محل جوشکاری فراهم می کند. این روش قابلیت کنترل دما و فوکوس پرتو الکترونی را دارد، که به عملکرد دقیق تر و محدوده کاری دقیق تر اجازه می دهد. همچنین، برخلاف روش های دیگر جوشکاری، عملیات انجام شده در این روش از تماس مستقیم با قطعه جلوگیری می کند و به همین دلیل ممکن است ریسک آلودگی کمتری داشته باشد.
نیاز به عملیات پس پردازش کمتر: به دلیل دمای بالای محیط در جوشکاری با پرتو الکترونی، عملیات پس پردازش مانند تمیز کردن، خنک کردن و انحراف کاهش می یابد. این باعث کاهش زمان و هزینه های مربوط به پس پردازش می شود.
مناسب برای جوشکاری مواد حساس به حرارت: EBW به عنوان یک فرایند جوشکاری با کنترل دما بالا می تواند در جوشکاری مواد حساس به حرارت، مانند آلیاژ های تیتانیوم، استفاده شود. این روش به آلیاژ ها اجازه می دهد که در دماهای بالا به طور دقیق جوش خورده و به شکل های پیچیده تر متصل شوند.
تجهیزات جوشکاری با پرتو الکترونی (EBW)
تجهیزات جوشکاری با پرتو الکترونی شامل موارد زیر می شوند:
منبع تولید الکترون: این تجهیزات شامل منبعی هستند که الکترون ها را تولید می کنند. این الکترون ها به صورت تشعشع الکترونی به قطعات فلزی منتقل می شوند.
جوشکاری کانونی: جوشکاری با پرتو الکترونی عمدتاً در یک کانون جوشکاری انجام می شود. این کانون شامل منابع الکترونی است که الکترون ها را به صورت متمرکز بر روی نقطه جوش تمرکز می دهند.
جدول جوشکاری: برای نگهداری و حرکت قطعات فلزی در جوشکاری با پرتو الکترونی، از یک جدول جوشکاری استفاده می شود. این جدول معمولاً دارای قابلیت چرخش و حرکت دو بعدی است تا قطعات را در موقعیت صحیح قرار دهد و جوشکاری دقیق را تسهیل کند.
سیستم کنترل: برای کنترل فرایند جوشکاری با پرتو الکترونی و تنظیم پارامتر های مختلف، از سیستم کنترل استفاده می شود. این سیستم می تواند شامل کامپیوتر و نرم افزار مربوطه باشد که به کاربر امکان می دهد تنظیمات را انجام دهد و فرایند جوشکاری را کنترل کند
سیستم خنک کننده: جوشکاری با پرتو الکترونی باعث گرم شدن قطعات فلزی می شود. برای جلوگیری از آسیب به قطعات و کنترل دما، سیستم خنک کننده بهکار می رود. این سیستم شامل سیستم های خنک کننده آب یا هوا است.
سیستم ایمنی: برای جوشکاری با پرتو الکترونی، سیستم ایمنی مناسب نیز لازم است. این شامل تجهیزاتی مانند شیلدینگ مناسب برای جلوگیری از تابش مستقیم پرتو الکترونی به اپراتور یا محیط کار است.
جوشکاری اکسی گاز (OFW) چیست؟
جوشکاری اکسی گاز (Oxy-Fuel Welding)، که به طور مختصر به آن OFW می گویند، یک فرایند جوشکاری است که در آن از ترکیبی از اکسیژن و گاز سوخت استفاده می شود تا حرارت لازم برای ذوب دو قطعه فلزی فراهم شود. OFW یکی از روش های سنتی جوشکاری است که در سال های قبل از توسعه روش های جدید تر مانند جوشکاری قوس الکتریکی و جوشکاری MIG/MAG استفاده می شد.
در فرایند OFW، گاز سوخت (معمولاً استیلن یا اسیتیلن) با استفاده از اکسیژن محلول در هوا به آتش می گیرد. این مخلوط سوخت-اکسیژن در اندازه های صحیح تهیه و تنظیم می شود تا دما و حرارت مناسبی برای ذوب فلز فراهم کند.
قطعات مورد جوش قرار گرفته و در معرض شعله قرار می گیرند و هنگامی که دما به اندازه کافی بالا برسد، قطعات فلزی ذوب می شوند و با هم جوش می خورند. جوشکاری اکسی کار در انواع مختلفی وجود دارد که عبارت اند از:
- جوشکاری با گاز پروپان
- جوشکاری با گاز و فشار
- جوشکاری هوا استیلن
- جوشکاری با اکسیژن استیلن
- جوشکاری اکسیژن هیدروژن
جوشکاری با گاز پروپان چیست؟
جوشکاری با گاز پروپان یک روش جوشکاری است که در آن از گاز پروپان به عنوان منبع حرارت استفاده می شود. گاز پروپان یکی از سوخت های فسیلی است که در صنعت برای تامین حرارت در فرآیند های مختلف مورد استفاده قرار می گیرد، و جوشکاری یکی از این فرآیندهاست.
برای جوشکاری با گاز پروپان، ابتدا یک فشار قوی از گاز پروپان و اکسیژن به همراه منبع آتش درست می کنند. سپس این مخلوط گازی به عنوان منبع حرارت برای ذوب قطعات مورد نیاز استفاده می شود. ذوب قطعات می تواند با استفاده از شعله مستقیم یا با استفاده از پیستون های هوای گرم نتیجه شود.
جوشکاری با گاز پروپان در فرآیندهای مختلفی مانند جوشکاری فلزات، برش فلزات، گرم کردن و تغییر شکل قطعات فلزی و حتی جوشکاری لوله های پلاستیکی استفاده می شود. به هر حال، در هر روش جوشکاری، نکات ایمنی بسیار مهم هستند و باید دقت و احتیاط لازم را در استفاده از گاز پروپان و ابزارهای مربوطه رعایت کرد. همچنین، برای جوشکاری حرفهای و دقیق با گاز پروپان، می توانید به آموزش های مربوطه مراجعه کنید و یا با صنعتگران و کارشناسان مجرب مشورت نمایید.
مزایای جوشکاری با گاز پروپان
این روش دارای مزایای زیادی است که شامل موارد زیر می شود:
همراهی با هزینه کمتر: استفاده از گاز پروپان در جوشکاری باعث کاهش هزینه های انرژی می شود، زیرا گاز پروپان در مقایسه با سایر گاز های جوشکاری مانند استیلن، آرگون و CO2، هزینه کمتری دارد.
قابلیت استفاده در محیط های متنوع: گاز پروپان در محیط های مختلف و در شرایط متفاوت مانند فضای باز، دماهای مختلف و محیط های خشک و مرطوب، قابل استفاده است. این ویژگی باعث می شود که جوشکاری با گاز پروپان برای زمینه های مختلف از جمله ساخت و ساز، تعمیرات، صنعت خودرو سازی و صنایع فلزی، بسیار مناسب باشد.
سهولت حمل و نقل: گاز پروپان در مقایسه با برخی دیگر انواع گاز ها، به عنوان یک گاز فشرده و قابل حمل، آسانی در حمل و نقل را دارد. این مزیت برای کاربرانی که نیاز به جوشکاری در محل های مختلف دارند، بسیار مهم است.
قابلیت کنترل حرارت: گاز پروپان، با قابلیت تنظیم شدت و دمای شعله، به جوشکاران امکان می دهد تا در طول عملیات جوشکاری، حرارت مورد نیاز را کنترل کنند. این ویژگی به عنوان یکی از مزیت های مهم در جوشکاری با گاز پروپان محسوب می شود.
آسانی استفاده: استفاده از جوشکاری با گاز پروپان بسیار آسان است و نیاز به تجهیزات پیچیده تری نسبت به روش های دیگر ندارد. این امر باعث می شود که حتی کاربران مبتدی نیز بتوانند با استفاده از گاز پروپان به راحتی جوشکاری کنند.
جوشکاری با گاز و فشار چیست؟
جوشکاری با گاز و فشار یک روش اتصال قطعات فلزی است که در آن از حرارت و فشار گاز برای ایجاد اتصال بین قطعات استفاده می شود. در این روش، دو قطعه فلزی که قرار است به هم متصل شوند، با استفاده از حرارت و فشار گاز به حالت گدازه (محلول جامد و مذاب فلز) تبدیل می شوند و به یکدیگر متصل می شوند.
مزایای جوشکاری با گاز و فشار
این روش دارای مزایا و مزیت های متعددی است که عبارت اند از:
قابلیت جوشکاری قطعات فلزی با ضخامت های مختلف: جوشکاری با گاز و فشار امکان جوشکاری قطعات فلزی با ضخامت های مختلف را فراهم می کند. این روش، به خصوص برای جوشکاری قطعات فلزی ضخیم و سنگین بسیار مناسب است.
اتصال قوی و دوام: جوشکاری با گاز و فشار به دلیل استفاده از فشار بالا و حرارت متمرکز، اتصالات قوی و دوام بالایی را فراهم می کند. این اتصالات معمولاً مقاوم در برابر ضربه، تنش و ارتعاش هستند و در برابر عوامل زیستی و محیطی نیز مقاومت خوبی دارند.
کنترل دقیق دما و حرارت: در جوشکاری با گاز و فشار، میزان دما و حرارت به صورت دقیق قابل کنترل است. این امکان به جوشکاران می دهد تا دمای مناسب برای جوشکاری هر نوع فلز را تنظیم کرده و کیفیت جوش را بهبود بخشند.
عدم نیاز به مصرف الکترود: در جوشکاری با گاز و فشار، برخلاف روش های دیگر مانند جوشکاری الکتریکی، نیازی به استفاده از الکترود برای اتصال قطعات نیست. این امر به معنای عدم نیاز به تعویض و هزینه برداری از الکترود ها است.
صرفه جویی در زمان و هزینه: جوشکاری با گاز و فشار به دلیل سرعت بالا و کنترل دقیق فرآیند، زمان و هزینه های جوشکاری را کاهش می دهد. همچنین، عدم نیاز به استفاده از الکترود و استفاده بهینه از مواد، باعث صرفه جویی در هزینه ها می شود.
تجهیزات جوشکاری با گاز و فشار
برای انجام جوشکاری با گاز و فشار، از اجزای زیر استفاده می شود:
سیستم جوشکاری: این سیستم شامل یک محفظه گاز است که می تواند گاز های مختلفی مانند آرگون، هلیوم، آزوت و… را شامل شود. گاز به عنوان محیط حمله در این روش استفاده می شود.
سیستم فشار: در جوشکاری با گاز و فشار، فشاری به قدر کافی روی قطعات فلزی وارد می شود تا آن ها را به هم فشرده کند و در نتیجه اتصال محکمی بین آن ها ایجاد شود. این فشار می تواند به صورت هیدرولیکی، پنوماتیک یا مکانیکی اعمال شود.
حرارت: برای جوشکاری با گاز و فشار، قطعات فلزی به دمایی بالا (نزدیک به نقطه ذوب) گرم می شوند. این حرارت می تواند از طریق فن های گازی، الکترود های نیمهخودکار یا لوله های حرارتی به قطعات اعمال شود.
زمان: برای ایجاد اتصال محکم، قطعات فلزی تحت فشار و حرارت قرار می گیرند و به مدت زمانی مشخص (که ممکن است به چند دقیقه برسد) در این شرایط نگه داشته می شوند تا اتصال به خوبی شکل بگیرد.
جوشکاری هوا استیلن چیست؟
جوشکاری هوا استیل، یا به عبارت دیگر جوشکاری فولاد ضد زنگ، فرآیندی است که در آن قطعات فلزی از جنس فولاد ضد زنگ، که معمولاً از آلیاژ های فولادی با حداقل ۱۰.۵٪ کروم ساخته می شوند، به یکدیگر متصل می شوند.
فولاد ضد زنگ به دلیل خواصی که دارد، از جمله مقاومت در برابر زنگ زدگی، اکسیداسیون و خوردگی، در برخورد با شرایط محیطی سخت مورد استفاده قرار می گیرد. به طور کلی، جوشکاری هوا استیلن نیازمند مهارت و تخصص بالا است و برای اطمینان از کیفیت و قوت اتصال، بهتر است توسط کارگران ماهر و با استفاده از تجهیزات مناسب انجام شود.
مزایای جوشکاری هوا استیلن
در زیر تعدادی از اصلیترین مزایای جوشکاری هوا استیل را بررسی می کنیم.:
مقاومت در برابر زنگ زدگی: هوا استیل مشهور به مقاومت بسیار بالا در برابر زنگ زدگی است. با جوشکاری صحیح هوا استیل، می توانیم این ویژگی مقاومت در برابر زنگ زدگی را در اتصالات جوشی حفظ کنیم.
قدرت مکانیکی بالا: هوا استیل دارای قدرت مکانیکی بسیار بالا است. با استفاده از روش های جوشکاری مناسب، می توان اتصالات جوشی با قدرت مکانیکی بالا و مقاومت در برابر تنش های مختلف را ایجاد کرد.
امکان شکل دهی: هوا استیل قابلیت شکل پذیری بسیار بالایی دارد. با استفاده از جوشکاری، می توان اتصالات پیچیده و شکل پذیر را در هوا استیل ایجاد کرد و به طرح ها و نیاز های خاص صنعتی پاسخ داد.
مقاومت در برابر درجه حرارت: هوا استیل دارای مقاومت بالا در برابر درجه حرارت است. با استفاده از روش های جوشکاری مناسب، می توان اتصالات جوشی را در برابر درجه حرارت های بالا و تغییرات حرارتی متنوع حفظ کرد.
ظاهر زیبا: هوا استیل دارای ظاهری زیبا و جذاب است. با استفاده از جوشکاری هوا استیل، می توان اتصالات جوشی را به طور صحیح و زیبا ایجاد کرد و از ظاهری جذاب در محصولات و سازه ها برخوردار شد.
مقاومت شیمیایی: هوا استیل دارای مقاومت بسیار خوبی در برابر عوامل شیمیایی است. با جوشکاری هوا استیل، می توان اتصالاتی با مقاومت شیمیایی بالا در برابر اکسیداسیون، خوردگی و تاثیرات محیطی دیگر ایجاد کرد.
تجهیزات جوشکاری هوا استیل
از جمله تجهیزات جوشکاری هوا استیل می توان به موارد زیر اشاره کرد:
ماشین های جوشکاری مقاومتی: برای جوشکاری قطعات هواستیل به همدیگر از ماشین های جوشکاری مقاومتی می توان استفاده کرد. این ماشین ها عموماً شامل دستگاه هایی با الکترود های کوتاه و دائمی می باشند.
لیزر جوشکاری: از لیزر های قدرتمند برای جوشکاری قطعات هواستیل نیز استفاده می شود. در این روش، انرژی لیزر به صورت دقیق بر روی قسمت های مورد نظر تمرکز می شود و باعث جوشکاری محلی و دقیق می شود.
جوشکاری با اکسیژن استیلن چیست؟
جوشکاری با استفاده از اکسیژن استیلن (Oxyacetylene welding) یا به طور مختصر جوشکاری استیلن، یک روش جوشکاری است که برای اتصال قطعات فلزی استفاده می شود. این روش از گاز استیلن و اکسیژن به عنوان منابع حرارت استفاده می کند.
فرایند جوشکاری با اکسیژن استیلن به این صورت است که گاز استیلن و اکسیژن در نسبت صحیحی ترکیب می شوند و به یک سوزنده (Torch) منتقل می شوند. در سوزنده، گاز های مخلوط به آتش می گیرند و یک شعله بسیار گرم و تماسی را ایجاد می کنند. این شعله گرم قادر است قطعات فلزی را ذوب کند و به هم بپیونداند.
وقتی شعله گرم بر روی قطعات فلزی تماس پیدا می کند، فلز های ذوب شده با هم ترکیب می شوند و پس از خنک شدن تشکیل یک اتصال محکم و ماندگار می دهند. جوشکاری با استفاده از اکسیژن استیلن برای اتصال فولاد های کربنی، فولاد های ضدزنگ و برخی از فلزات دیگر استفاده می شود.
مزایای جوشکاری با استفاده از اکسیژن استیلن
جوشکاری با استفاده از اکسیژن استیلن مزایای زیادی دارد که در ادامه آن ها را معرفی می کنیم:
- امکان جوشکاری قطعات با ضخامت مختلف
- قابلیت جوشکاری در محل و در محیط های بیرونی
- قابلیت استفاده در تعمیرات و تعمیرات فوری
- هزینه نسبتاً پایین نسبت به روش های جوشکاری پیچیده تر
تجهیزات جوشکاری با استفاده از اکسیژن استیلن
برای انجام جوشکاری با استفاده از اکسیژن استیلن، نیاز به تجهیزات و وسایل زیر است:
دستگاه جوشکاری استیلن: دستگاهی که برای ایجاد لهجه حرارتی بالا و آتش برای جوشکاری استفاده می شود. این دستگاه معمولاً شامل یک تورچ استیلن، بخاری، و اجزای دیگر برای تأمین سوخت و اکسیژن استیلن است.
بطری های گاز: برای تأمین سوخت و اکسیژن استیلن، بطری های گاز مخصوصی استفاده می شود. این بطری ها حاوی سوخت استیلن و اکسیژن هستند و با استفاده از رگولاتور ها و شیر های کنترل، فشار و دبی گاز را تنظیم می کنند.
لوازم ایمنی: همانند هر فرایند جوشکاری دیگر، استفاده از لوازم ایمنی مناسب از جمله عینک جوشکاری، لباس محافظ، دستکش های مقاوم در برابر حرارت و سایر لوازم محافظ جوشکاری بسیار مهم است.
جوشکاران ماهر: جوشکاران ماهری که تجربه و آموزش لازم را در زمینه جوشکاری با استفاده از اکسیژن استیلن دارند، برای انجام عملیات جوشکاری به خوبی و با کیفیت لازم احتیاج است.
جوشکاری اکسیژن هیدروژن چیست؟
جوشکاری اکسیژن هیدروژن یا به عبارتی دیگر جوشکاری HHO، روشی است که در آن از ترکیب گاز های هیدروژن و اکسیژن استفاده می شود تا در فرآیند جوشکاری به عنوان منبع حرارت و انرژی استفاده شود.
در این فرآیند، گاز هیدروژن و اکسیژن به نسبت 2:1 تولید و می سوزند تا آتش و جرقه ای بزرگ و بسیار گرم تولید شود. جوشکاری اکسیژن هیدروژن به خاطر داشتن خصوصیات خاص، می تواند در برخی از برنامه های جوشکاری مفید باشد.
مزایای جوشکاری اکسیژن هیدروژن
جوشکاری اکسیژن هیدروژن مزایای زیادی دارد که در ادامه برخی از آن ها را معرفی می کنیم.
حرارت بالا: جوشکاری اکسیژن هیدروژن دارای دما های بسیار بالاست که می تواند منجر به ذوب و اتصال قطعات فلزی باشد. این حرارت بالا به دلیل احتراق مخلوط هیدروژن و اکسیژن است که نیازی به منبع خارجی برقی یا گازی ندارد.
عدم تشکیل ذرات پرت: با استفاده از جوشکاری HHO، از دست دادن مواد جامد یا پرتی های ذرات فلزی بهصورت قابل توجهی کاهش می یابد. این امر می تواند در برخی کاربردهای دقیق و حساس مانند جوشکاری قطعات الکترونیکی مفید باشد.
محیط زیستی: در هنگام احتراق هیدروژن و اکسیژن، تنها محصول تولید شده آب است. به عبارتی دیگر، این فرآیند صفر گاز های گلخانه ای و آلودگی هوا تولید می کند و بسیار کمترین تأثیر بر محیط زیست دارد.
کاربرد گسترده: جوشکاری اکسیژن هیدروژن در صنایع مختلفی از جمله خودرو سازی، ساخت و ساز، تولید انرژی، جوشکاری لوله ها و غیره مورد استفاده قرار می گیرد.
تجهیزات جوشکاری اکسیژن هیدروژن
تجهیزات جوشکاری اکسیژن هیدروژن معمولاً شامل موارد زیر است:
مولد هیدروژن و اکسیژن: این دستگاه برای تولید هیدروژن و اکسیژن در نسبت صحیح برای جوشکاری استفاده می شود. معمولاً از فناوری الکترولیز برای تفکیک آب به هیدروژن و اکسیژن استفاده می شود.
لوله ها و خطوط تامین گاز: هیدروژن و اکسیژن تولید شده توسط مولد به کمک لوله ها و خطوطی به جوشکار منتقل می شوند.
سوزن و قلم جوشکاری: سوزن جوشکاری به طور معمول از جنس مس است و در آن جرقه برقی میان هیدروژن و اکسیژن تشکیل می شود. قلم جوشکاری برای اتصال قطعات مورد نظر با استفاده از حرارت و لحیم کاری استفاده می شود.
سیستم کنترل و ایمنی: این سیستم شامل سوئیچ ها، شیر ها، صمام ها و دستگاه های کنترلی است که جریان گاز را کنترل کرده و از نظر ایمنی اطمینان حاصل می کند.
جوشکاری قوسی چیست؟
جوشکاری قوسی یک روش جوشکاری است که در آن جرقه های الکتریکی بین قطب های مثبت و منفی یک الکترود تشکیل می شود. این جرقه ها یک دمای بسیار بالا و یک ماده یونیزه شده به نام پلاسما ایجاد می کنند که باعث انجام فرایند جوشکاری می شود.
در جوشکاری قوسی، قوس الکتریکی بین دو الکترود تشکیل می شود. یک الکترود به نام الکترود مثبت (آنود) و دیگری به نام الکترود منفی (کاتود) است. این الکترود ها به روشن شدن الکترود ها یا با استفاده از جریان برق مستقیم یا جریان متناوب باعث ایجاد قوس الکتریکی می شوند.
قوس الکتریکی تولید شده در جوشکاری قوسی بسیار داغ است و مواد قابل جوشکاری را به دما های بالا می رساند. این دماهای بالا باعث ذوب شدن مواد قابل جوشکاری می شوند و با استفاده از مواد جوشکاری مثل سیم جوشکاری، قطعات جوشکاری می شوند.
جوشکاری قوسی در صنایع مختلفی مانند خودرو سازی، ساخت و ساز، صنعت فضایی و صنایع فلزی استفاده می شود. این روش جوشکاری نسبتاً سریع و اقتصادی است و به طور گسترده ای در صنعت مورد استفاده قرار می گیرد. جوشکاری قوسی در انواع مختلفی وجود دارد که عبارت اند از:
- جوشکاری قوسی با الکترود دستی روکش دار (SMAW)
- جوشکاری قوسی با گاز محافظ و الکترود فلزی (MIG/MAG یا GMAW)
- جوشکاری قوسی با گاز محافظ و الکترود تنگستنی (GTAW یا TIG)
- جوشکاری قوس پلاسما (PAW)
- جوشکاری قوسی زیر پودری (SAW)
- جوشکاری قوسی توپودری (FCAW)
- جوشکاری اتمی هیدروژن
- جوشکاری قوسی کربنی (CAW)
جوشکاری قوسی با الکترود دستی روکش دار (SMAW) چیست؟
جوشکاری قوسی با الکترود دستی روکش دار (SMAW) یکی از روش های شایع جوشکاری فلزات است که با استفاده از الکترود های قوسی کار می کند. در این روش، قوس الکتریکی بین الکترود و قطعه کار ایجاد می شود که باعث ذوب شدن الکترود و تشکیل حوضچه جوش می شود.
در SMAW، الکترود دستی شامل قسمت مرکزی (که از فلز جوشکاری شده تشکیل شده است) و روکش حفاظتی است که قوس جوش را از هوا و عناصر خارجی محافظت می کند. روکش حفاظتی از موادی مانند مس یا فریت تشکیل شده است که هنگام جوشکاری ذوب شده و پوششی حاکم بر سطح جوش ایجاد می کند.
این پوشش به عنوان یک لایه محافظ عمل می کند و از مخلوط شدن قوس جوش با هوا، اکسیژن و نیتروژن جلوگیری می کند که می تواند به تشکیل شکستگی ها و ناهمواری های سطحی در جوش منجر شود.
فرایند SMAW برای جوشکاری فلزات مختلف از جمله فولاد، آهن، آلومینیوم و فلزات غیر آهنی استفاده می شود. این روش جوشکاری قابل اجرا در شرایط خارج از کارگاهی و در محیط های باز است و به علت استفاده از الکترود دستی برای جوشکاری، به طور گسترده ای در صنعت ساختمانی، خودرو سازی، تعمیرات و ساخت و ساز استفاده می شود.
جوشکاران ماهر برای انجام SMAW باید دقت کافی را در تنظیم جریان جوش، نوع و قطر الکترود، نوع وضعیت جوشکاری (عمودی، افقی و غیره) و تکنیک های موجود در این روش داشته باشند.
مزایای جوشکاری قوسی با الکترود دستی روکش دار (SMAW)
در زیر به برخی از مزایا و موارد استفاده از جوشکاری SMAW اشاره خواهم کرد:
قابلیت استفاده در شرایط دشوار: جوشکاری SMAW می تواند در شرایط فضای باز و در محیط های خارجی با شرایط آب و هوایی متفاوت انجام شود. علاوه بر این، این روش در محیط های با امکانات محدود و محیط های دسترسی محدود نیز قابل استفاده است.
امکان استفاده در جوشکاری توده ای: با استفاده از الکترود های قوی و قطر بزرگ، جوشکاری SMAW قادر است به جوشکاری توده های ضخیم و قطعات سنگین بپردازد. این امکان در برخی روش های دیگر جوشکاری وجود ندارد.
انعطاف پذیری مواد جوشکاری: جوشکاری SMAW قابلیت جوشکاری انواع مواد فلزی متفاوت را داراست، از جمله فولاد، آلومینیوم، استیل و غیره. همچنین، می توان با انتخاب الکترود های متناسب با نوع فلز، خواص مکانیکی جوش را تنظیم کرد.
هزینه کم: ابزار های مورد نیاز برای جوشکاری SMAW ساده و ساخت آن ها ارزان است. این روش نیاز به تجهیزات پیشرفته تر مانند گاز محافظ و دستگاه های پیچیده را ندارد، که هزینه کمتری برای جوشکاری به همراه دارد.
قابلیت استفاده در محل: یکی از مزایای بزرگ جوشکاری SMAW، امکان استفاده در محل می باشد. این روش قابلیت انجام جوشکاری در محل های مختلف را فراهم می کند، از جمله در تعمیرات در محل، ساخت و ساز در محیط های خارجی و تعمیرات اضطراری.
تجهیزات جوشکاری الکترود دستی
تجهیزات اصلی مورد نیاز برای جوشکاری الکترود دستی عبارت اند از:
الکترود ها: الکترود ها معمولاً شامل قطب مثبت و منفی هستند. قطب مثبت به عنوان الکترود اصلی استفاده می شود و قطب منفی به عنوان مقطع کار مورد استفاده قرار می گیرد. الکترود ها براساس نوع مواد جوش، قطر و نوع پوشش خارجی طبقه بندی می شوند.
منبع برق: برای جوشکاری الکترود دستی، منبع برقی قدرتمندی که قادر به تأمین جریان الکتریکی لازم برای جوشکاری است، لازم است. منابع برق معمولاً شامل ترانسفورماتورهای جریان مستقیم (DC) یا ترانسفورماتورهای جریان متناوب (AC) هستند. همچنین، برخی از منابع برق قابل حمل بوده و برای کار های میدانی مناسب هستند.
لبه ها و فریم ها: جهت نگهداری الکترود و قطعات فلزی، لبه ها و فریم های جوشکاری استفاده می شود. این تجهیزات می توانند برای تثبیت قطعات فلزی و جلوگیری از حرکت غیرضروری در حین جوشکاری مفید باشند.
لباس های ایمنی: جوشکاری الکترود دستی ممکن است با خطراتی همچون ذرات فلزی مذاب، اشعه UV و خطرات حرارتی همراه باشد. لباس های ایمنی مانند عینک های ایمنی، لباس های ضد حرارت، دستکش های محافظ و کاپشن های آتشنشانی برای حفاظت از جوشکاران بسیار مهم هستند.
ابزارهای جانبی: برخی از ابزارهای جانبی مورد نیاز برای جوشکاری الکترود دستی شامل قیچی جوشکاری، خرطوم جوشکاری، برس سیمان و قیچی فلزات است.
جوشکاری قوسی با گاز محافظ و الکترود فلزی (MIG/MAG یا GMAW) چیست؟
جوشکاری قوسی با گاز محافظ و الکترود فلزی (MIG/MAG یا GMAW) یک روش جوشکاری است که در آن الکترود فلزی به عنوان منبع جوشکاری استفاده می شود. این روش معمولاً برای جوشکاری فلزات آهنی و غیر آهنی استفاده می شود و در صنعت و ساخت و ساز بسیار رایج است.
در جوشکاری MIG/MAG، الکترود فلزی به صورت پیوسته وارد منطقه جوشکاری می شود و توسط جریان قوس الکتریکی ذوب می شود. در همین حین، گاز محافظی مانند آرگون یا مخلوطی از آرگون و دی اکسید کربن از طریق نازل الکترود به منطقه جوشکاری پخش می شود.
این گاز محافظ برای حفظ و محافظت از منطقه جوشکاری و جوشکاری از تاثیر جوی و اکسیژن هوا استفاده می شود و همچنین به عنوان یک پوشش محافظ برای جوشکاری و جامعه جوشکاری عمل می کند.
روش MIG/MAG یا GMAW بسیار محبوب است زیرا سرعت بالا، کیفیت بالا و امکانات خوبی در جوشکاری لحیم و انتقال گرمای جوشکاری دارد. همچنین، این روش قابلیت اتوماسیون و خودکارسازی را دارد، که امکان جوشکاری در خطوط تولید صنعتی را فراهم می کند.
مزایای جوشکاری قوسی با گاز محافظ و الکترود فلزی (MIG/MAG یا GMAW)
جوشکاری قوسی با گاز محافظ و الکترود فلزی (MIG/MAG یا GMAW) یکی از روش های پر کاربرد جوشکاری است و دارای بسیاری از مزایا است. در زیر تعدادی از این مزایا آمده است:
سرعت بالا: جوشکاری MIG/MAG یکی از روش های سریع و کارآمد جوشکاری است. استفاده از الکترود فلزی و جریان قوسی مستقیم در این روش به جوشکار امکان می دهد با سرعت بالا جوشکاری را انجام دهد و به طور مداوم الکترود را پیشروی دهد.
کارآیی بالا: با استفاده از گاز محافظ در جوشکاری MIG/MAG، امکان خنک کردن الکترود و منطقه جوش را فراهم می کند. این به معنی کاهش آلاینده ها، پیشگیری از تشکیل شیارها و حفظ خواص مکانیکی قطعه جوش شده است. همچنین، استفاده از الکترود فلزی باعث کاهش آلایش با آلومینیوم و اکسید نیتروژن می شود.
قابلیت جوشکاری خودکار: جوشکاری MIG/MAG به خوبی برای جوشکاری خودکار مناسب است. این روش امکان استفاده از روبات های جوشکاری را فراهم می کند که باعث افزایش سرعت، دقت و دقت جوشکاری می شود.
قابلیت استفاده در انواع فلزات: جوشکاری MIG/MAG قابلیت استفاده در انواع مختلفی از فلزات را دارد، از جمله فولاد های کربنی، فولاد های ضد زنگ، آلومینیوم و فلزات دیگر. با تغییر الکترود و گاز محافظ، می توان به سادگی با مواد مختلف جوشکاری کرد.
کم هدر رفتن مواد جوش: در جوشکاری MIG/MAG به دلیل استفاده از الکترود فلزی، هیچ بخشی از الکترود به عنوان ضایعات از بین نمی رود. این باعث می شود هزینه های مربوط به جوشکاری، از جمله هزینه مصرف الکترود، کاهش یابد.
کنترل آسان: جوشکاری MIG/MAG از دستگاه های کنترل آسانی استفاده می کند که به جوشکار امکان کنترل دقیق جریان قوس، سرعت الکترود و جریان گاز محافظ را می دهد. این کنترل دقیق باعث ایجاد جوشکاری با کیفیت و دقیق تر می شود.
جوشکاری بهرهور: جوشکاری MIG/MAG به دلیل سرعت بالا، کارآیی بالا و کاهش ضایعات مواد جوش، از لحاظ اقتصادی بهرهور است. این روش امکان جوشکاری سریع تر و به میزان بیشتری را فراهم می کند، که می تواند در تولید صنعتی بهبود قابل توجهی داشته باشد.
تجهیزات جوشکاری قوسی با گاز محافظ و الکترود فلزی (MIG/MAG یا GMAW)
تجهیزات جوشکاری MIG/MAG شامل موارد زیر است:
بستر جوشکاری (Welding Power Source): این واحد تأمین کننده جریان الکتریکی برای جوشکاری است. آن را می توان با استفاده از برق شهری یا سایر منابع برقی انرژی زا تغذیه کرد. بستر جوشکاری باید قابلیت تنظیم جریان، ولتاژ و سرعت پیشرانش را داشته باشد.
سیم جوش (Welding Wire): سیم جوش فلزی به عنوان الکترود در این روش جوشکاری استفاده می شود. سیم جوش ممکن است از جنس های مختلفی مانند فولاد کربنی، فولاد ضد زنگ و آلیاژ های خاص ساخته شود. انتخاب سیم جوش صحیح بر اساس جنس قطعه کار و نیاز های جوشکاری مشخص می شود.
سیم تغذیه (Wire Feeder): سیم تغذیه برای تغذیه سیم جوش به طور مستقیم به نقطه جوشکاری استفاده می شود. این واحد سیم جوش را به سرعت و جریان مورد نیاز برای جوشکاری منظم تغذیه می کند.
گاز محافظ (Shielding Gas): گاز محافظ برای حفاظت فضای جوشکاری از هوا و آلاینده ها استفاده می شود. نوع گاز محافظ بسته به نوع فلز جوشکاری و شرایط جوشکاری ممکن است متفاوت باشد. برخی از محافظ های گازی شامل آرگون، دی اکسید کربن و مخلوطی از آرگون و دی اکسید کربن هستند.
تورچ جوشکاری (Welding Torch): تورچ جوشکاری شامل سیم جوش، سیم تغذیه و خروجی گاز محافظ است. این تورچ قابلیت کنترل دقیق تغذیه سیم جوش، گاز محافظ و جریان الکتریکی را فراهم می کند. عملکرد صحیح تورچ جوشکاری توسط جوشکار بسیار مهم است.
جوشکاری قوسی با گاز محافظ و الکترود تنگستنی (GTAW یا TIG) چیست؟
جوشکاری قوسی با گاز محافظ و الکترود تنگستنی (GTAW)، که به طور عام با نام TIG (تونگستن بمعنای الکترود Tungsten Inert Gas) نیز شناخته می شود، یک روش جوشکاری است که برای اتصال قطعات فلزی استفاده می شود.
در این روش، یک الکترود تنگستنی غیر مصرفی در دستگاه جوش قرار داده می شود که توسط جریان الکتریکی گرم می شود. همچنین، برای حفظ و تأمین یک محیط غیر فعال اطراف سوزن جوش، یک گاز محافظ (معمولاً آرگون و همچنین مخلوط آرگون و هلیم) از طریق نازل دستگاه جوش به منطقه جوشکاری تزریق می شود.
در این روش، جریان الکتریکی بین الکترود تنگستنی و قطعات فلزی ایجاد می شود، که باعث تشکیل یک قوس الکتریکی بین آنها می شود. در نتیجه، قطعات فلزی به دلیل حرارت تولید شده توسط قوس الکتریکی، ذوب می شوند و با هم اتصال می یابند.
جوشکاری GTAW به دلیل کنترل دقیق دما، اتصال قوی و کیفیت بالا، برای اتصال قطعات فلزی از جنس های مختلف، به خصوص فلزات آلیاژی حساس، استفاده می شود. این روش جوشکاری معمولاً در صنایع مختلفی مانند صنعت خودرو سازی، صنعت هوا و فضا، صنعت دریایی، تولید لوله ها و سیستم های لوله کشی، تولید قطعات پزشکی و صنایع دیگر مورد استفاده قرار می گیرد.
مزایای جوشکاری قوسی با گاز محافظ و الکترود تنگستنی (GTAW یا TIG)
این روش به دلایل متعددی مزایای قابل توجهی دارد. در زیر تعدادی از این مزایا آورده شده است:
کنترل دقیق: جوشکاری TIG برخلاف بسیاری از روش های دیگر، امکان کنترل دقیق بر روی فرآیند جوشکاری را فراهم می کند. این به معنای امکان تنظیم جریان الکتریکی، سرعت جریان گاز محافظ، سرعت تغذیه الکترود و دیگر پارامتر های فرآیند است. این امکان به جوشکاران کمک می کند تا کنترل دقیق تری بر روی جوشکاری داشته باشند و نتایج بهتری را به دست آورند.
کیفیت بالا: با استفاده از جوشکاری TIG، می توان کیفیت بالایی از نظر ظاهری و مکانیکی در جوش ها به دست آورد. این روش به علت استفاده از الکترود تنگستنی باعث تولید جوشکاری تمیز و دقیق می شود. جوش های TIG به طور معمول کمترین نا همواری ها، خزش ها و خطوط لغزشی را نسبت به سایر روش ها دارند.
عدم استفاده از ماده جانبی: در جوشکاری TIG، الکترود تنگستنی برای تولید قوس الکتریکی استفاده می شود و به طور معمول ماده جانبی اضافی به فرایند اضافه نمی شود. این موضوع در بسیاری از کاربرد ها مفید است، به خصوص زمانی که از آلیاژ های خاصی استفاده می شود که به طور معمول نیاز به اضافه کردن ماده جانبی ندارند.
قابلیت جوشکاری متناهی: جوشکاری TIG به دلیل کنترل دقیق و عدم استفاده از ماده جانبی، برای جوشکاری قطعات بسیار نازک و حساس مناسب است. با استفاده از این روش می توان قطعاتی را جوش داد که ضخامت بسیار کمی داشته باشند.
استفاده در جوشکاری آلیاژ های خاص: GTAW معمولاً برای جوشکاری آلیاژ های خاصی مانند آلومینیوم، استیل ضدزنگ و آلیاژ های تیتانیوم استفاده می شود. این روش به دلیل عدم اضافه کردن ماده جانبی و کنترل دقیق، در جوشکاری این نوع آلیاژ ها عملکرد بسیار خوبی دارد.
جوشکاری قوس پلاسما (PAW) چیست؟
جوشکاری قوس پلاسما (Plasma Arc Welding یا PAW) یک روش جوشکاری پیشرفته است که از قوس پلاسما برای اتصال قطعات فلزی استفاده می کند. در این فرایند، قوس پلاسما توسط جریان الکتریکی بین یک الکترود منفی (کاتد) و قطعه کار (آند) ایجاد می شود.
قوس پلاسما، با تولید یک جریان الکتریکی بسیار بالا و ایجاد حرارت بسیار زیاد، گاز های اطراف را یونیزه و به حالت پلاسما تبدیل می کند. در جوشکاری قوس پلاسما، از یک نوار فلزی با نقطه ذوب بالا برای جوشکاری استفاده می شود.
این نوار فلزی، به عنوان الکترود کاتدی عمل می کند و توسط جریان الکتریکی از طریق آند گرم می شود. همچنین، گاز های محافظ نیز به منظور جلوگیری از تعامل قوس با جوی محیط استفاده می شوند.
قوس پلاسما در جوشکاری قوس پلاسما دما و انرژی بالایی دارد که امکان جوشکاری مواد با ضخامت های بزرگتر را فراهم می کند. همچنین، به دلیل دمای بالا و شدت حرارت قوس پلاسما، این فرایند می تواند با سرعت بالا انجام شود و اتصالات قوی و با کیفیتی را به وجود آورد. PAW معمولاً در صنایع مختلفی مانند صنایع هوا و فضا، خودرو سازی، الکترونیک و ساخت و ساز استفاده می شود.
در مجموع، جوشکاری قوس پلاسما یک روش پیشرفته و کارآمد برای اتصال قطعات فلزی است که با استفاده از قوس پلاسما، امکان جوشکاری مواد با ضخامت بالا و تولید اتصالات با کیفیت بالا را فراهم می کند.
مزایای جوشکاری قوس پلاسما (PAW)
این روش به دلایل زیر مزایای قابل توجهی دارد:
قدرت نفوذ بالا: در جوشکاری قوس پلاسما، قدرت نفوذ بالایی در اتصال جوش ایجاد می شود. این به معنی توانایی ایجاد اتصالات محکم و عمیق در ترکیبات فلزی ضخیم است. به علاوه، قدرت نفوذ بالا می تواند کاهش نیاز به طیف وسیعی از پردازش های پیشرفته مثل چسباندن، مته نوکی و برش باشد.
نیاز به تمیز کاری کم: PAW معمولاً نیازی به تمیز کاری یا حذف لایه اکسید از سطح قطعه ها ندارد. این به معنی کاهش زمان و هزینه های مربوط به آماده سازی سطح قطعه ها قبل از جوشکاری است.
آسانی استفاده: PAW قابلیت کنترل و استفاده آسان را فراهم می کند. تنظیماتی مثل جریان الکتریکی و گاز محافظ قابل تنظیم هستند، که به جوشکاران اجازه می دهد پارامتر هایی جوشکاری را براساس نیازهای خود تنظیم کنند. همچنین، عدم وابستگی به جهت گرانش در فرایند PAW به اپراتورها اجازه می دهد به راحتی در موقعیت های مختلف قرار بگیرند و به جوشکاری دسترسی داشته باشند.
کیفیت جوش بالا: PAW قابلیت ایجاد اتصالات جوش با کیفیت بالا را دارد. این روش به دلیل امکان استفاده از گاز محافظ و جریان الکتریکی دقیق، کنترل دما و سرعت سرد شدن جوش را فراهم می کند. نتیجه آن، جوش های متناسب با استاندارد های کیفیت بالا و قابل قبول بین المللی است.
امکان استفاده در محیط های مختلف: PAW به عنوان یک فرایند مبتنی بر قوس الکتریکی، امکان استفاده در محیط های مختلف را دارد. می توان در فضای باز یا در محیط های آبی از این روش استفاده کرد.
تجهیزات جوشکاری قوس پلاسما (PAW)
تجهیزات جوشکاری قوس پلاسما شامل موارد زیر می شود:
منبع برق: منبع برق برای تولید جریان الکتریکی مورد نیاز برای ایجاد قوس پلاسما استفاده می شود. این منبع می تواند از نوع تکنولوژی ترانسفورماتور، روتاری یا مبدل الکترونیکی باشد.
الکترود ها: در جوشکاری قوس پلاسما، استفاده از الکترود های مخصوصی که قابلیت تحمل جریان بالا و تابش پلاسمای قوی را داشته باشند، ضروری است. این الکترود ها معمولاً از مواد مانند تنگستن یا تنگستن آلیاژی تهیه می شوند.
تورچ جوشکاری: تورچ جوشکاری قوس پلاسما برای ایجاد قوس الکتریکی و انتقال جریان پلاسما به نقطه جوش استفاده می شود. تورچ به صورت دستی در دسترس قرار می گیرد و دارای سیستم خنک کننده است تا حرارت تولید شده توسط جریان پلاسما را تا حداقلی کاهش دهد.
گاز محافظ: برای حفاظت از منطقه جوشکاری و جلوگیری از تداخل با هوا و آلاینده ها، از یک گاز محافظ استفاده می شود. گاز های متداول برای جوشکاری قوس پلاسما شامل آرگون، هلیم و نیتروژن می باشند.
سیستم کنترل: تجهیزات جوشکاری قوس پلاسما معمولاً دارای یک سیستم کنترل هوشمند هستند که برای تنظیم جریان، شدت و دمای قوس و متغیر های دیگر مورد استفاده قرار می گیرد. این سیستم کنترل می تواند از نوع دستی یا خودکار باشد.
جوشکاری قوسی زیر پودری (SAW) چیست؟
جوشکاری قوسی زیر پودری (Submerged Arc Welding)، مخفف SAW است، یک روش جوشکاری است که در آن قوس الکتریکی بین الکترود فلزی و قطعه کار به وسیله یک پودر فلزی (به عنوان الکترود فرق دهنده) در محیط زیر پودری تشکیل می شود. این روش به عنوان یکی از روش های جوشکاری غوطهور معروف است.
در جوشکاری قوسی زیر پودری، قوس الکتریکی بین الکترود و قطعه کار در یک محیط پودری تشکیل می شود. این پودر فلزی که به عنوان الکترود فرق دهنده عمل می کند، به طور مستقیم در قلب قوس قرار دارد و با حرارت قوس ذوب می شود. در اثر ذوب شدن پودر فلزی، قطره های ذوب شده به صورت زیر پودری به سطح جوش می ریزند و جوش تشکیل می شود.
مزایای جوشکاری قوسی زیر پودری
جوشکاری قوسی زیر پودری مزایای زیادی دارد که در ادامه به مهم ترین آن ها اشاره می کنیم:
سرعت جوشکاری بالا: این روش به دلیل استفاده از الکترود فلزی بزرگ و محیط زیر پودری، سرعت جوشکاری بالا و پوشش بزرگی را ارائه می دهد.
عملکرد بهتر: جوشکاری قوسی زیر پودری می تواند به عملکرد مکانیکی و مقاومت در برابر خستگی قطعه کار کمک کند.
کیفیت جوش بالا: با استفاده از این روش، جوش هایی با کیفیت بالا، اندازه های یکنواخت و خواص مکانیکی مطلوب تولید می شوند.
توانایی جوشکاری در شرایط خاموش: به دلیل استفاده از محیط زیر پودری، این روش قابلیت جوشکاری در شرایطی که قوس الکتریکی قابل رویت نیست را داراست.
کارآیی بالا: با توجه به سرعت جوشکاری بالا و امکان استفاده از الکترود فلزی بزرگ، این روش کارآیی بالایی دارد.
تجهیزات جوشکاری قوسی زیر پودری (SAW)
برای انجام جوشکاری قوسی زیر پودری، نیاز به تجهیزات خاصی دارید که شامل موارد زیر می شود:
منبع تغذیه الکتریکی: برای تولید قوس الکتریکی و تامین جریان لازم برای جوشکاری، نیاز به یک منبع تغذیه الکتریکی است. منبع تغذیه معمولاً از نوع ترانسفورماتوری یا اینورتری است و می تواند برای جریان مستمر یا جریان متناوب استفاده شود.
الکترود قوسی: برای جوشکاری قوسی زیر پودری از الکترود های قوسی خاصی استفاده می شود. این الکترود ها شامل هسته فلزی و پوشش معدنی هستند و عمدتاً از فولاد کربنی یا فولاد آلیاژی تشکیل شده اند.
دستگاه تغذیه الکترود: برای حرکت خودکار الکترود در طول جوشکاری، نیاز به یک دستگاه تغذیه الکترود و سیستم حرکتی دارید. این دستگاه الکترود را به طور پیوسته و تدریجی تغذیه می کند تا الکترود به صورت خودکار حرکت کند و طول قوس را حفظ کند.
دستگاه پودرزنی: برای تغذیه پودر معدنی زیر پودری، نیاز به یک دستگاه پودرزنی است. این دستگاه پودر را به صورت خودکار و به میزان دقیقی تغذیه می کند تا پوشش محافظ روی جوش تشکیل شود.
سیستم خنک کننده: در طول جوشکاری قوسی زیر پودری، دمای بالای الکترود و قطعه کار ممکن است باعث افزایش دمای تجهیزات شود. برای جلوگیری از آب گرفتگی و خرابی تجهیزات، نیاز به سیستم خنک کننده است که حرارت را از تجهیزات جوشکاری تخلیه می کند.
جوشکاری قوسی توپودری (FCAW) چیست؟
جوشکاری قوسی توپودری (FCAW) یک روش جوشکاری است که در آن الکترود مورد استفاده شامل یک سیم فلزی پر شده با پودر فلزی است. در این روش، قوس الکتریکی بین الکترود و قطعه کاری تشکیل می شود و در همین حین، پودر فلزی به صورت خودکار از داخل الکترود تغذیه می شود و در منطقه جوشکاری ذوب شده و با فلز پایه ترکیب می شود.
جوشکاری قوسی توپودری یک روش پیشرفته از جوشکاری قوسی با الکترود پر شده است. با استفاده از پودر فلزی درون الکترود، این روش می تواند به نحوی باشد که از فرایندهای جوشکاری سنتی مثل جوشکاری MIG/MAG و جوشکاری تیگ استفاده می کند، اما از نظر کیفیت جوش و سرعت جوشکاری، بهتر عمل می کند.
مزایای جوشکاری قوسی توپودری
جوشکاری قوسی توپودری مزایای بسیاری دارد که در ادامه با برخی از آن ها آشنا می شوید:
سرعت بالا: این روش می تواند به صورت مداوم جوش بزند و سرعت جوشکاری را افزایش دهد.
اندازه جوشکاری: استفاده از الکترود پر شده باعث می شود تا بتوان در جوشکاری های عمودی و افقی و حتی در موقعیت های خاصی مانند جوشکاری سقفی نیز استفاده کرد.
مقاومت بالا در برابر خوردگی: جوشکاری قوسی توپودری می تواند جوش هایی با خواص مقاومت بالا در برابر خوردگی تولید کند.
کاربرد های گسترده: این روش در صنایع مختلفی مانند صنعت ساخت و ساز، صنعت خودرو سازی، صنعت دریایی و غیره مورد استفاده قرار می گیرد.
تجهیزات جوشکاری قوسی توپودری (FCAW)
تجهیزات جوشکاری قوسی توپودری (FCAW) شامل موارد زیر می شوند:
منبع جوش: این شامل منبع تغذیه برق و دستگاه جوش است. در جوشکاری توپودری معمولاً از منبع جوشکاری قوسی با ولتاژ ثابت (DC) یا منبع جوشکاری قوسی با ولتاژ متغیر (AC) استفاده می شود.
الکترود جوش: الکترود های جوشکاری توپودری معمولاً شامل یک مهار کننده فلزی با پوشش پودر جوش هستند. پوشش پودر جوش شامل موادی است که باعث تولید گاز های محافظ و خاصیت پوششی بر روی حوضچه جوش می شوند.
سیم فیدر: سیم فیدر یک دستگاه است که سیم جوش را به صورت خودکار تغذیه می کند. این سیم جوش از طریق سیم فیدر به الکترود جوش متصل می شود و باعث تغذیه پودر جوش به الکترود می شود.
دستگاه حفاظت گاز: در برخی از موارد، برای حفاظت از حوضچه جوش در جوشکاری توپودری از گاز های حفاظتی مانند آرگون یا مخلوطی از آرگون و دی اکسید کربن استفاده می شود. دستگاه حفاظت گاز، این گاز ها را به صورت محافظ حول حوضچه جوش ارائه می دهد.
لبه بردار: لبه بردار یا تمیزکننده سطح، برای تمیز کردن و آماده سازی سطح جوش قبل از جوشکاری استفاده می شود. این ابزار می تواند شامل برس، دیسک های سنگین، یا ابزارهای دیگری باشد که برای حذف آلودگی ها و ایجاد سطحی صاف و تمیز استفاده می شوند.
جوشکاری اتمی هیدروژن چیست؟
جوشکاری اتمی هیدروژن یک فرایند جوشکاری است که در آن از انرژی تولید شده توسط واکنش هسته ای هیدروژن (معمولاً هیدروژن-دیوتریوم یا هیدروژن-تریتیوم) برای اتصال قطعات فلزی استفاده می شود. این فرایند از ترکیب انرژی هسته ای و توان جوشکاری که به دلیل دمای بسیار بالا به دست می آید، برای ایجاد اتصال قوی و محکم بین قطعات استفاده می کند.
در جوشکاری اتمی هیدروژن، انرژی هستهای در ناحیهای از فلزی که قرار است جوش داده شود، تولید می شود. این انرژی هستهای، باعث افزایش دما در ناحیه جوش می شود و باعث ذوب و اتصال قطعات فلزی به هم می شود. از آنجا که این فرایند به انرژی هستهای برای تولید گرما و جوش استفاده می کند، به آن “جوشکاری اتمی هیدروژن” گفته می شود.
مزایای جوشکاری اتمی هیدروژن
این روش دارای مزایای زیر است:
کیفیت بالا: جوشکاری اتمی هیدروژن به دلیل استفاده از گاز هیدروژن، باعث بهبود کیفیت جوش و خواص مکانیکی قطعات جوشکاری شده می شود. هیدروژن باعث کاهش میزان آلودگی هوای محیط و اکسیداسیون مواد فلزی می شود که نتیجه آن جوش با خواص مکانیکی بالا و عیب کمتر است.
کارآیی بالا: استفاده از جوشکاری اتمی هیدروژن باعث افزایش سرعت و کارایی جوشکاری می شود. ترکیب هیدروژن با گاز های دیگر، امکان دستیابی به دمای بالا و سرعت جوشکاری بیشتر را فراهم می کند.
عملکرد در دما های بالا: یکی از مزایای جوشکاری اتمی هیدروژن این است که می توان در دما های بالا جوشکاری را انجام داد. هیدروژن به دلیل دارا بودن نقطه جوش بسیار بالا (حدود ۲۵۰۰ درجه سانتی گراد)، امکان جوشکاری قطعاتی که نیاز به دما های بالا دارند، فراهم می کند.
کاهش میزان نفوذ آلاینده ها: جوشکاری اتمی هیدروژن به دلیل استفاده از محیط گازی، میزان نفوذ آلاینده ها به مناطق جوشکاری را کاهش می دهد. این امر باعث کاهش نیاز به پاک سازی و پسجوشکاری بعد از جوشکاری می شود.
محیط زیست و اقتصادی: جوشکاری اتمی هیدروژن به دلیل کاهش آلاینده ها و آسیب به محیط زیست کمتر، به عنوان یک روش پایدار و دوستدار محیط زیست مطرح است. علاوه بر این، با افزایش کارایی و کاهش هزینه ها، از لحاظ اقتصادی نیز مزیت دارد.
جوشکاری قوسی کربنی (CAW) چیست؟
جوشکاری قوسی کربنی (CAW) به روشی اشاره دارد که در آن از قوس برقی برای ایجاد اتصالات میان قطعات فلزی استفاده می شود، اما با استفاده از گاز های بسیار خنک کننده مانند هلیوم به جای گاز های معمولی مانند آرگون. این روش برای جوشکاری فولاد های آلیاژی کربنی پیچیده مورد استفاده قرار می گیرد.
جوشکاری قوسی کربنی برای جوشکاری فولاد های آلیاژی با درصدهای کربن بالا، که معمولاً در حدود ۰.۶ تا ۱.۵ درصد است، مناسب است. این فرآیند اغلب در صنایع نفت و گاز، صنایع خودرو سازی و ساخت و ساز استفاده می شود.
با استفاده از جوشکاری قوسی کربنی، امکان جوشکاری قطعات فلزی با ضخامت ها و شکل های مختلف وجود دارد. همچنین، این روش قابلیت پیوند دادن به فولاد های با کربن بالا را دارد و باعث ایجاد اتصالات با استحکام بالا و خواص مکانیکی مناسب می شود.
در جوشکاری قوسی کربنی، از منابع جوشکاری قوس الکتریکی مانند جوشکاری قوسی فلزی استفاده می شود. با اعمال جریان الکتریکی بین الکترود و قطعات فلزی، قوس برقی ایجاد می شود که می تواند دمای بسیار بالا را تولید کند.
در همین حین، گاز های خنک کننده مانند هلیوم در اطراف منطقه جوشکاری استفاده می شوند تا دمای منطقه جوشکاری را کاهش دهند و از اکسیداسیون و آلایش قطعات فلزی جلوگیری کنند.
جوشکاری قوسی کربنی یک فناوری پیشرفته و پیچیده است که تخصص و مهارت فنی بالایی برای اجرای صحیح آن نیاز دارد. علاوه بر این، مطالعه و اجرای روش های مناسب برای کنترل دما و عوامل دیگر در جوشکاری قوسی کربنی بسیار مهم است تا اتصالات با کیفیت بالا و خواص مطلوب حاصل شود.
مزایای جوشکاری قوسی کربنی (CAW)
مزایای جوشکاری قوسی کربنی عبارت اند از:
سرعت بالا: جوشکاری قوسی کربنی به دلیل امکان استفاده از جریان بالا، سرعت بالایی را برای اتمام عملیات جوشکاری فراهم می کند. این امر به دلیل این است که جوشکاری CAW بر روی تمام ضخامت ها امکان پذیر است و نیازی به استفاده از مواد اضافی ندارد.
قابلیت جوشکاری انواع فلزات: جوشکاری قوسی کربنی می تواند بر روی انواع مختلف فلزات اعم از فولاد کربنی، فولاد ضد زنگ و آلیاژ ها اعم از آلومینیوم و مس انجام شود. این روش برای جوشکاری قطعات متفاوتی که از مواد مختلف ساخته شدهاند بسیار مفید است.
کیفیت بالا: جوشکاری قوسی کربنی باعث ایجاد جوش با کیفیت بالا و مقاومت مکانیکی قابل قبولی می شود. همچنین، زمانی که از فلزات با دماهای بالا استفاده می شود، خواص مکانیکی بهبود می یابد و ایجاد حرارت محدود می شود که باعث کاهش خطر تغییر ساختار فلزی می شود.
عملیات ساده: جوشکاری قوسی کربنی نسبت به روش های دیگری مانند جوشکاری MIG و TIG کمترین نیاز را به آموزش و مهارت دارد. به علاوه، نیاز به تجهیزات پیچیده و هزینه بالا نیز کمتر است.
کاربرد گسترده: جوشکاری قوسی کربنی در صنایع مختلفی از جمله خودرو سازی، ساخت و ساز، تعمیرات صنعتی و تولید لوله ها استفاده می شود. این روش برای اتصال قطعات فلزی بزرگ و تولید سازه های فلزی مناسب است.
تجهیزات جوشکاری قوسی کربنی (CAW)
تجهیزات جوشکاری قوسی کربنی (CAW) شامل موارد زیر می شود:
منبع برق: یک سیستم تأمین برق مورد نیاز برای ایجاد قوس الکتریکی استفاده می شود. این منبع برق می تواند از منابع مختلفی مانند باتری ها، مولد جریان مستقیم (DC) یا مولد جریان متناوب (AC) تامین شود.
الکترود ها: دو الکترود با خاصیت های مختلف استفاده می شوند. یک الکترود مثبت (آند) و یک الکترود منفی (کاتد) وجود دارد. جریان الکتریکی از الکترود مثبت به الکترود منفی جریان می کند و قوس الکتریکی را تشکیل می دهد.
مواد پایه و جوش: فلزات مادرزادی که قرار است جوش داده شوند، در نقاط تماس خود آبشده می شوند و با خنک شدن اتصال جامد تشکیل می دهند. مواد پایه و جوش بسته به نوع کاربرد و نیاز های جوشکاری ممکن است متفاوت باشند.
سیستم خنک کننده: به دلیل دمای بالای قوس الکتریکی در جوشکاری قوسی کربنی، سیستم خنک کننده برای خنک کردن الکترود ها و قطعات کار استفاده می شود. این سیستم معمولاً شامل یک پمپ خنک کننده، مبدل حرارتی و یک مخزن آب است.
جوشکاری با پرتو لیزر (LBW) چیست؟
جوشکاری با پرتو لیزر (Laser Beam Welding یا به اختصار LBW) یک فرایند جوشکاری صنعتی است که در آن از پرتو لیزر برای اتصال قطعات فلزی استفاده می شود. در این فرایند، پرتو لیزر با تمرکز بالا و انرژی بالا بر روی یک منطقه کوچک از قطعات فلزی تابانده می شود.
انرژی لیزر، باعث ذوب و ذوب ناپذیر شدن قطعات فلزی می شود و با استفاده از این انرژی، قطعات با هم جوش می خورند. در جوشکاری با پرتو لیزر، پرتو لیزر از منابع لیزر قوی مانند لیزر های فیبری، لیزر های دیودی یا لیزر های یاگ قدرتمند استفاده می شود. این پرتو لیزر به صورت متمرکز شده و بر روی محل مورد نظر تابانده می شود.
تمرکز بالای انرژی لیزر باعث ایجاد یک لکه کوچک و شدیداً داغ در قطعات فلزی می شود که باعث ذوب و اتصال قطعات می شود. پس از تاباندن پرتو لیزر، قطعات تحت تأثیر نیروهای جوشکاری قرار می گیرند تا بخش های ذوب شده به هم بچسبند و جامد شوند.
مزابای جوشکاری با پرتو لیزر (LBW)
جوشکاری با پرتو لیزر (LBW)، دارای مزیت های فراوان است که در ادامه با برخی از آن ها آشنا می شوید.
دقت بالا: پرتو لیزر به طور دقیق بر روی منطقه مورد نظر تمرکز می شود و به همین دلیل قابلیت دسترسی به نواحی دشوار و پیچیده را دارد.
حرارت محدود: در این فرایند، حرارت به مناطق اطراف منتقل نمی شود و به همین دلیل خطر آسیب به قطعات نزدیک به منطقه جوشکاری کمتر است.
کنترل پارامتر های جوشکاری: با تنظیم قدرت و فاصله پرتو لیزر، می توان به طور دقیق کنترل دما و سرعت جوشکاری و برنامه ریزی دقیق تری را در انجام جوشکاری داشت.
تجهیزات جوشکاری با پرتو لیزر (LBW)
برای انجام جوشکاری با پرتو لیزر، تجهیزات خاصی نیاز است که شامل موارد زیر می شود:
لیزر: انتخاب لیزر مناسب برای جوشکاری با پرتو لیزر بسیار مهم است. لیزر های با توان و انرژی بالا معمولاً برای جوشکاری صنعتی استفاده می شوند.
سیستم حوضچه و جدول: قطعات مورد جوشکاری بر روی سیستم حوضچه قرار می گیرند و توسط جدول محکم شده و در جای خود ثابت می مانند. این سیستم ها باید به منظور تحمل حرارت و وزن قطعات مناسب باشند.
سیستم تمرکز پرتو: پرتو لیزر باید به طور دقیق بر روی نقطه جوشکاری تمرکز شود. سیستم تمرکز پرتو به این منظور طراحی شده است که بتواند پرتو را به صورت دقیق روی نقطه مورد نظر تمرکز کند.
سیستم تابش لیزر: این سیستم با استفاده از آینه ها و عدسی ها، پرتو لیزر را از منبع لیزر به سیستم تمرکز پرتو هدایت می کند.
سیستم کنترل: یک سیستم کنترل پیچیده معمولاً برای کنترل پارامتر های جوشکاری مانند توان لیزر، سرعت جوشکاری و عمق حفره استفاده می شود.
سیستم خنک کننده: به دلیل ایجاد حرارت زیاد در فرآیند جوشکاری با پرتو لیزر، سیستم خنک کننده برای خنک کردن لیزر و تجهیزات مرتبط استفاده می شود.
جوشکاری غیر ذوبی چیست؟
جوشکاری غیر ذوبی یا جوشکاری فشاری، روشی است که در آن، اتصالات بین قطعات فلزی به وسیلهی فشار، اصطکاک، امواج الکترو مغناطیسی یا گرما ایجاد می شود، اما ماده فلزی به صورت مذاب نمی شود. در جوشکاری غیر ذوبی، دما معمولاً زیر دمای ذوب نقطه مواد استفاده شده در اتصال قرار می گیرد.
مزیت اصلی جوشکاری غیر ذوبی در مقایسه با جوشکاری ذوبی در این است که امکان استفاده از دما های پایین تر و عدم نیاز به استفاده از مواد مذاب و مواد اضافی برای ایجاد اتصال وجود دارد. این روش ها معمولاً برای جوشکاری قطعات با خواص مکانیکی خوب، عدم تغییر در ساختار میکروسکوپیک و حفظ ابعاد قطعات مناسب هستند.
به عنوان مثال، در جوشکاری فرکشن، قطعات به روشی مکانیکی در معرض فرکشن قرار می گیرند و با فشار و گرمای تولید شده به هم جوش می خورند. در جوشکاری اصطکاکی نیز، با استفاده از اصطکاک بین قطعه و ابزار جوشکاری، حرارت تولید شده موجب جوشکاری قطعات می شود.
جوشکاری غیر ذوبی در صنایع مختلفی مانند خودرو سازی، هوا و فضا، ساخت و ساز و صنایع فلزی استفاده می شود. مزایای جوشکاری غیر ذوبی شامل سرعت بالا، استفاده کمتر از حرارت و عدم تغییر ویژگی های مکانیکی فلزات می باشد. این روش برای اتصال قطعاتی با خواص مختلف و همچنین جوشکاری فلزاتی با نقاط ذوب پایین مفید است.
روش های مختلفی برای جوشکاری غیر ذوبی وجود دارد که عبارت اند از:
- جوشکاری فراصوتی (UW)
- جوشکاری اصطکاکی (FW)
- جوشکاری مقاومتی (RW)
- جوشکاری انفجاری (EW)
جوشکاری التراسونیک یا فراصوتی (UW) چیست؟
جوشکاری التراسونیک یا فراصوتی (Ultrasonic Welding) یک فرایند جوشکاری است که در آن قطعات متصل را با استفاده از اصول اولتراسونیک به هم متصل می کند. در این روش، امواج صوتی با فرکانس بالا (بیش از حدالصوت) از طریق قطعات قرار می گیرند و باعث ایجاد اصطکاک و انتقال حرارت بین سطوح متصل می شوند.
این انتقال حرارت به مقدار کافی برای ذوب شدن ناحیهای از قطعات منجر می شود و پس از خنک شدن و جامد شدن، قطعات به هم متصل می شوند. فرایند جوشکاری التراسونیک در بسیاری از صنایع، از جمله صنایع خودرو سازی، الکترونیک، پزشکی، بسته بندی و تولید پلاستیک استفاده می شود.
مزایای جوشکاری التراسونیک یا فراصوتی (UW)
جوشکاری التراسونیک یا فراصوتی (UW) مزایای بسیاری دارد که در ادامه برخی از آن ها را بیان می کنیم:
سرعت بالا: جوشکاری التراسونیک فرایندی سریع است و می تواند در زمان کوتاهی قطعات را به هم متصل کند.
عدم نیاز به مواد مصرفی: در این روش، هیچ نیازی به استفاده از مواد جوشکاری نظیر الکترود ها یا لحیم ها نیست.
عدم تولید ذرات و گاز های مضر: در جوشکاری التراسونیک، هیچ ذرات مضر یا گاز های آلاینده تولید نمی شوند، بنابراین به عنوان یک روش پاک و سبز شناخته می شود.
اتصال قوی: جوشکاری التراسونیک به دلیل ایجاد اصطکاک و اتصال مولکولی بین قطعات، اتصالات قوی و محکمی ایجاد می کند.
قابلیت استفاده در قطعات نا همسان: این روش قابلیت جوشکاری قطعات مختلفی با مشخصات متفاوت را دارد، از جمله قطعات نا همسان و مختلف از نظر ضخامت و ماده ساختاری.
تجهیزات جوشکاری التراسونیک یا فراصوتی (UW)
تجهیزات جوشکاری التراسونیک شامل موارد زیر میشود
مولد التراسونیک: این تجهیز به امواج صوتی با فرکانس بالا نیاز دارد که توسط مولد تراسونیک تولید می شود. این مولد عموماً شامل یک ترانسدیوسر (تبدیل کننده انرژی) است که انرژی الکتریکی را به انرژی مکانیکی تبدیل می کند.
هواپیمایی یا بوندر: قطعاتی که قرار است به هم جوش داده شوند، بر روی بوندر قرار می گیرند. بوندر نقش حفظ فشار و راه اندازی ارتعاشات را دارد.
سونوترود: سونوترود در محل تماس با قطعات قرار می گیرد و امواج صوتی را به قطعات منتقل می کند. این ترد خارجی می تواند به شکل استوانهای، مخروطی یا شکل دیگری باشد، بسته به نیاز های جوشکاری.
دستگاه فشار: قطعات با استفاده از دستگاه فشار به هم فشرده می شوند و جوش خود را شکل می دهند. دستگاه فشار باید قدرت کافی برای اعمال فشار لازم را داشته باشد.
جوشکاری اصطکاکی (FW) چیست؟
جوشکاری اصطکاکی (Friction Welding) یا به اختصار FW، یک فرایند جوشکاری است که در آن قطعات فلزی به وسیله اصطکاک و حرارت به هم متصل می شوند. در این فرایند، دو قطعه فلزی به هم فشرده می شوند و سپس به صورت روان به یکدیگر نزدیک می شوند تا اصطکاک بین آنها تولید شود. اصطکاک موجب ایجاد گرما می شود و به تبدیل انرژی حرکتی به انرژی حرارتی منجر می شود.
با افزایش دما، قطعات فلزی به یکدیگر متصل می شوند و در نهایت در نقطه اتصالی سرد شده و اتصال محکمی را تشکیل می دهند. به دلیل این که در جوشکاری اصطکاکی نیازی به استفاده از مواد پر کاربرد نیست، می توان انواع مختلف فلزات را به یکدیگر جوش داد.
جوشکاری اصطکاکی برای اتصال قطعات با اندازه ها و شکل های مختلف استفاده می شود و به طور گسترده در صنایع خودرو سازی، هوا و فضا، ساخت و ساز، نفت و گاز و صنایع دیگر استفاده می شود.
این فرایند جوشکاری سریع تر و اقتصادی تر از بسیاری از روش های جوشکاری سنتی است و می تواند به کاهش زمان و هزینه تولید کمک کند. جوشکاری اصطکاکی در انواع مختلفی وجود دارد که عبارت اند از:
- جوشکاری اغتشاشی (FSW)
- جوشکاری دورانی یا چرخشی (FRW)
جوشکاری اغتشاشی (FSW) چیست؟
جوشکاری اغتشاشی (FSW) یا به انگلیسی “Friction Stir Welding” یک فرآیند جوشکاری نوین است که برای اتصال قطعات فلزی بدون استفاده از فلز ذوب شده استفاده می شود. این فرآیند در دهه 1990 توسط محققان دانشگاه TWI (موسسه جوشکاری و تحقیقات مواد) در انگلستان توسعه یافت.
در جوشکاری اغتشاشی، قطعه های فلزی که قرار است جوش داده شوند، با استفاده از یک ابزار سیال و استوانه ای به نام پین جوشکاری، تحت تاثیر نیروی فشار و حرکت گرداننده این ابزار قرار می گیرند. پین جوشکاری در مسیر حرکت، فشار و حرارت زیادی به قطعه اعمال می کند و باعث می شود دو قطعه فلزی به هم بچسبند.
در این فرآیند، فلز ها به طور مکانیکی متحرک می شوند و در نتیجه نیازی به ذوب شدن فلز ها نیست. این مزیت باعث می شود کیفیت جوش بسیار بالا و ضرر حرارتی واقعا کمتری نسبت به روش های جوشکاری سنتی داشته باشد.
جوشکاری اغتشاشی به عنوان یک فرآیند پیشرفته جوشکاری، در صنایع مختلفی از جمله خودرو سازی، هوا و فضا، ساخت و ساز، صنعت دریایی و صنایع نظامی استفاده می شود. این فرآیند قابلیت جوش دادن مواد فلزی مختلف را دارد و می تواند قطعاتی را با شکل ها و ضخامت های متفاوت به هم متصل کند. همچنین، جوشکاری اغتشاشی امکان تعمیر قطعات جوش داده شده را نیز فراهم می کند.
مزایای جوشکاری اغتشاشی (FSW)
در ادامه، به مزایای جوشکاری اغتشاشی می پردازیم:
اندازه کمتر حوضه حرارتی: در جوشکاری اغتشاشی، حرارت به صورت محدود به ناحیه جوش منتقل می شود. این باعث می شود که منطقه پرهیز از نرم شدن و افت کیفیت فلزات اطراف جوشکاری شود. همچنین، نیاز به استفاده از اجزای حفاظتی مانند گاز یا پودر حفاظتی نیز کاهش می یابد.
کاهش نیاز به فرآیند های پس پردازش: در روش های سنتی جوشکاری، پس از جوشکاری، عملیات پس پردازشی مانند ماشین کاری و صیقل کاری برای حذف نا همواری ها و خراش های ناشی از حوضه حرارتی ممکن است لازم باشد. با استفاده از جوشکاری اغتشاشی، این نیاز به پس پردازش کاهش یافته و زمان و هزینه تولید را کاهش می دهد.
اتصالات قوی: جوشکاری اغتشاشی باعث ایجاد اتصالات بسیار قوی و استحکام بالا می شود. این روش به دلیل جلوگیری از تشکیل حوضه حرارتی و ذوب متقاطع، به وجود پلیت فلزی قوی در ناحیه جوش می انجامد
جوشکاری مواد قابل جوشکاری: جوشکاری اغتشاشی قابلیت جوشکاری موادی را که در روش های سنتی مشکل دارند، فراهم می کند. این شامل فلزات آلومینیومی، فولاد های ضد زنگ، مس و آلیاژ های تیتانیومی است.
کاهش تغییر خواص مواد: در جوشکاری اغتشاشی، به دلیل عدم استفاده از حرارت قوس الکتریکی، تغییر خواص مکانیکی و میکروساختار فلزات در ناحیه جوش به حداقل می رسد. این مزیت مخصوصاً در صنایع حساس به دما و خواص مواد مانند صنعت هوا و فضا بسیار مهم است.
کارآیی بالا: جوشکاری اغتشاشی یک فرآیند سریع و کارآمد است. سرعت اجرای بالا و عدم نیاز به تغییرات مکانیکی مانند قراردادن الکترود یا نیاز به تمیز کردن قطعات پس از جوشکاری، زمان تولید را به حداقل می رساند.
تجهیزات جوشکاری اغتشاشی (FSW)
جوشکاری اغتشاشی به عنوان یک روش جدید و نو آورانه جوشکاری، در سال های اخیر بسیار مورد توجه قرار گرفته است. تجهیزات جوشکاری اغتشاشی، معمولاً شامل موارد زیر می شوند:
دستگاه جوشکاری اغتشاشی: دستگاه جوشکاری اغتشاشی (FSW) ابزار اصلی در فرآیند جوشکاری اغتشاشی است. این دستگاه شامل قطعه ای است که به نام پین یا شافت می باشد و در اثر چرخش این قطعه در محل جوشکاری، اغتشاشی در جهت جریان جوش تولید می شود.
تیغه جوشکاری: تیغه جوشکاری یا ابزار جوشکاری به شکلی ساخته می شود که به وسیله آن می توان جوشکاری اغتشاشی را انجام داد. تیغه جوشکاری معمولاً از مواد مقاوم و محکمی مانند آلیاژ آلومینیومی استوانه ای ساخته می شود.
ماشین CNC: در برخی از حالات، استفاده از ماشین CNC (کنترل عددی کامپیوتری) برای جوشکاری اغتشاشی استفاده می شود. این ماشین ها با استفاده از برنامه های کامپیوتری قادر به انجام حرکات دقیق و اصولی بر روی قطعات جوشکاری هستند.
سیستم خنک کننده: در هنگام انجام جوشکاری اغتشاشی، تولید حرارت زیادی صورت می گیرد. برای جلوگیری از گرم شدن بیش از حد و خراب شدن قطعه جوشکاری، سیستم خنک کنندهای مانند سیستم آب خنک کننده می تواند استفاده شود.
دستگاه های مکانیکی: برای ثبت و تنظیم حرکات دقیق دستگاه جوشکاری اغتشاشی، از دستگاه های مکانیکی نیز استفاده می شود. این دستگاه ها می توانند موقعیت قطعات را تغییر دهند و حرکات دقیق را کنترل کنند.
جوشکاری دورانی یا چرخشی (FRW) چیست؟
جوشکاری چرخشی (به انگلیسی: Rotary Welding) یک روش جوشکاری است که در آن قطعاتی که باید به هم جوش داده شوند، در حالت چرخشی قرار می گیرند. در این روش، قطعات جوش داده شده به وسیله یک دستگاه چرخشی مانند خریدو، میز چرخشی یا دستگاه جوشکاری اتوماتیک که بر روی دستگاه چرخشی نصب شده است، قرار می گیرند.
سپس جوشکار به صورت پیوسته و به اطراف قطعات چرخشی، جوش را می سازد. جوشکاری چرخشی برای جوشکاری قطعات استفاده می شود که دارای ساختار هندسی یا قوسی است و نیاز به جوش در اطراف آن ها دارد.
این روش به ویژه در صنایعی مانند صنعت نفت و گاز، صنعت خودرو سازی، ساخت و ساز، تولید لوله ها و بسیاری از بخش های صنعتی دیگر استفاده می شود. با توجه به اینکه این روش نیازمند دستگاه های خاصی است، هزینه بالایی برای راه اندازی و استفاده از آن وجود دارد. همچنین، مهارت و تخصص خاصی در استفاده از دستگاه های جوشکاری چرخشی مورد نیاز است.
مزایای جوشکاری دورانی یا چرخشی (FRW)
در زیر تعدادی از مزایای جوشکاری دورانی را بررسی می کنیم:
اتصال قوی: جوشکاری دورانی می تواند اتصالات قوی و استحکام بالایی را ایجاد کند. با استفاده از جریان الکتریکی دورانی، قطعات فلزی به هم فشرده می شوند و جوشکاری اتصال محکمی را تشکیل می دهد.
عدم نیاز به ماده جوشکاری: در جوشکاری دورانی، برای ایجاد اتصال قوی، نیازی به استفاده از ماده جوشکاری نیست. این به این معنی است که می توان قطعات را بدون استفاده از مواد جدا کننده یا فلزات مذاب دیگر جوشکاری کرد.
عدم نیاز به فشار: در بسیاری از روش های جوشکاری، فشار مورد نیاز است که ممکن است منجر به تغییر شکل قطعات یا نیاز به تجهیزات و ماشین آلات پیچیده تر شود. با جوشکاری دورانی، نیازی به فشار متقابل نیست و این مزیت را ارائه می دهد که قطعات را به سادگی و بدون نیاز به تجهیزات خاصی جوش دهید.
سرعت بالا: جوشکاری دورانی می تواند به سرعت بالا جوش را تشکیل دهد. با استفاده از جریان الکتریکی دورانی، حرارت به سرعتی بالا تولید می شود و فرآیند جوشکاری به سرعت انجام می شود. این مزیت مخصوصاً در خطوط تولید صنعتی با ضربه زدایی بالا یا خطوط تولید انبوه بسیار مفید است.
استفاده آسان: جوشکاری دورانی روشی نسبتاً آسان برای استفاده است. برای انجام این نوع جوشکاری، عموماً نیازی به ماشین آلات پیچیده یا تجهیزات خاصی نیست و فرآیند ساده تری نسبت به برخی از روش های دیگر جوشکاری دارد.
کاربرد های گسترده: جوشکاری دورانی در بسیاری از صنایع و کاربرد ها استفاده می شود. این روش در صنایع خودرو سازی، صنایع دریایی، ساخت و ساز، تولید لوله های فلزی، صنعت الکترونیک و غیره استفاده می شود.
تجهیزات جوشکاری دورانی یا چرخشی (FRW)
تجهیزات جوشکاری دورانی شامل موارد زیر می شوند:
ماشین جوشکاری TIG دورانی: این ماشین ها به منظور جوشکاری قطعاتی که در اطراف آن ها باید یک دوران کامل انجام شود، استفاده می شوند. این ماشین ها قادرند بر روی لوله ها و سایر قطعات دورانی جوشکاری دقیق انجام دهند.
دستگاه جوشکاری MIG/MAG دورانی: این دستگاه ها برای جوشکاری قطعات دورانی با استفاده از فرایند جوشکاری MIG یا MAG استفاده می شوند. این فرایندها از الکترود پیچشی استفاده می کنند که باعث می شود جوشکاری روی قطعات دورانی انجام شود.
دستگاه جوشکاری پلاسما دورانی: این دستگاه ها از تکنولوژی جوشکاری پلاسما برای جوشکاری قطعات دورانی استفاده می کنند. این روش جوشکاری با استفاده از یک قوس پلاسمایی بین الکترود و قطعه کار انجام می شود.
جوشکاری مقاومتی (RW) چیست؟
جوشکاری مقاومتی (RW) مخفف عبارت Resistance Welding است. این روش جوشکاری، یکی از روش های پر کاربرد در صنعت جوشکاری است که برای اتصال قطعات فلزی به یکدیگر استفاده می شود. در این روش، جرقه ای بین قطعات فلزی ایجاد می شود که باعث ذوب شدن نقاط مخابره بین دو قطعه می شود و اتصالی محکم و دوام دار ایجاد می کند.
در جوشکاری مقاومتی، قطعات فلزی که قرار است جوش داده شوند، بین دو الکترود قرار می گیرند. الکترود ها به منبع برق متصل شده و جریان الکتریکی از طریق قطعات فلزی جریان می یابد. بر اثر مقاومت الکتریکی قطعات فلزی، گرما به آن ها منتقل می شود و نقاط مخابره بین قطعات ذوب می شوند. سپس فشاری به قطعات اعمال می شود تا در حالت جامد سرد شوند و اتصال محکمی بین قطعات ایجاد شود.
جوشکاری مقاومتی به دلیل سرعت بالا، قابلیت اتصال قطعات با ضخامت مختلف، عدم نیاز به مواد افزودنی، عدم تولید چربی و بخار و همچنین کنترل آسان فرایند، در صنایع مختلفی از جمله خودرو سازی، الکترونیک، لوازم خانگی و صنایع فلزی استفاده می شود. جوشکاری مقاومتی در انواع مختلفی وجود دارند که عبارت اند از:
- جوشکاری مقاومتی نقطه ای
- جوشکاری مقاومتی درز جوش (RSEW)
- جوشکاری مقاومتی زائده ای (RPW)
- جوش آپست
جوشکاری مقاومتی نقطه ای چیست؟
جوشکاری مقاومتی نقطهای (Spot Welding) یک روش جوشکاری است که در آن دو قطعه فلزی به وسیله جریان الکتریکی و فشار فشرده به هم متصل می شوند. در این روش، قطعات فلزی به نقاط خاصی که جوشکاری می شوند، فشار داده می شوند و جریان الکتریکی بین این نقاط عبور می کند. با تأثیر جریان الکتریکی و فشار فشرده، نقاط تماس قطعات گرم می شوند و با یکدیگر یکپارچه می شوند.
برای انجام جوشکاری مقاومتی نقطه ای، از یک دستگاه جوشکاری مقاومتی نقطه ای استفاده می شود. این دستگاه شامل دو الکترود است که روی قطعات فلزی قرار می گیرند و فشار به آن ها وارد می شود. الکترود ها به گونه ای طراحی شده اند که از بین هم متحرکند و برای هماهنگی با ضخامت قطعه، می توانند تنظیم شوند.
در زمانی که الکترود ها به قطعات فشرده می شوند، جریان الکتریکی از یک الکترود عبور می کند، از قطعات عبور کرده و به الکترود دیگر باز می گردد. این جریان الکتریکی باعث ایجاد حرارت در نقاط تماس قطعات می شود و فلزات گرم شده را به طور موقت ذوب می کند. پس از خنک شدن و ایجاد جامد شدن مجدد، نقاط تماس به یکدیگر متصل می شوند و جوش تشکیل می شود.
جوشکاری مقاومتی نقطه ای به دلیل سرعت بالا و نیاز کمتر به نیروی دستی، در صنایع خودرو سازی، صنعت فلزات و ساخت و ساز استفاده می شود. این روش برای اتصال قطعات فلزی با ضخامت کمتر مناسب است و می تواند در اتصالاتی که نیاز به ظاهر زیبا و قوی دارند، مؤثر باشد.
مزایای جوشکاری مقاومتی نقطه ای
این روش برای جوشکاری قطعات فلزی در صنایع مختلف استفاده می شود و دارای مزایای زیر می باشد:
سرعت عمل: جوشکاری مقاومتی نقطه ای بسیار سریع انجام می شود و زمان کمی برای جوشکاری هر نقطه نیاز دارد. این امر باعث می شود فرآیند جوشکاری برای تولیدی هایی با ضریب نیروی کار بالا و زمان محدود مفید باشد.
اتصال قوی: در جوشکاری مقاومتی نقطه ای، اتصال میان دو قطعه فلزی بسیار قوی و محکم است. با اعمال فشار و جریان بالا، دو قطعه فلزی به طور محکم با هم جوش می خورند و اتصالی با مقاومت بالا و قابلیت انتقال جریان و حرارت خوب ایجاد می شود.
عدم نیاز به مواد جانبی: در جوشکاری مقاومتی نقطه ای، عموماً نیازی به استفاده از مواد جانبی مانند الکترود جوش نیست. این امر باعث کاهش هزینه و زمان مورد نیاز برای جوشکاری می شود.
کارایی انرژی: در جوشکاری مقاومتی نقطه ای، انرژی مصرفی بسیار کمتر از روش های جوشکاری دیگر مانند جوشکاری قوس الکتریکی است. این به معنای صرفه جویی در هزینه های انرژی و حفاظت از محیط زیست است.
قابلیت اتصال انواع مختلف فلزات: جوشکاری مقاومتی نقطه ای قادر به اتصال انواع مختلفی از فلزات مانند فولاد، آلومینیوم و فولاد ضد زنگ است. این روش می تواند در بسیاری از صنایع مانند صنعت خودرو سازی، صنعت لوازم خانگی و صنعت الکترونیک مورد استفاده قرار گیرد.
تجهیزات جوشکاری مقاومتی نقطه ای
برای انجام جوشکاری مقاومتی نقطهای، شما به تجهیزات زیر نیاز دارید:
دستگاه جوشکاری مقاومتی نقطهای: این دستگاه شامل منابع تغذیه الکتریکی، الکترود ها، و سیستم کنترل جوش است. منابع تغذیه برق مورد نیاز برای تولید جریان الکتریکی برای جوشکاری را فراهم می کنند. الکترود ها به عنوان محیط انتقال جریان بین قطعات فلزی عمل می کنند. سیستم کنترل جوش وظیفه کنترل پارامتر های جوشکاری، مانند جریان الکتریکی، زمان، و فشار را دارد.
الکترود ها: الکترود ها در جوشکاری مقاومتی نقطه ای نقش بسیار مهمی دارند. الکترود ها به دو نوع ثابت و دورانی تقسیم می شوند. الکترود های ثابت در مواقعی استفاده می شوند که جزئیات دقیق تری برای قرار دادن الکترود در نقاط مورد نظر وجود دارد، در حالی که الکترود های دورانی برای سرعت بالا و محل های دسترسی دشوار مورد استفاده قرار می گیرند.
سیستم خنک کننده: در طول جوشکاری مقاومتی نقطهای، ممکن است الکترود ها و قطعات فلزی گرم شوند. برای جلوگیری از افزایش دما و خنک شدن الکترود ها، سیستم خنک کننده استفاده می شود. این سیستم شامل یک منبع سردایی (معمولاً آب یا روغن) و یک سیستم پمپاژ برای گردش مایع خنک کننده است.
دستگاه فشار: جوشکاری مقاومتی نقطه ای نیازمند اعمال فشار مناسب بر روی قطعات فلزی است. برای این منظور، معمولاً از دستگاه فشار مجهز به سیستم هیدرولیک یا پنوماتیک استفاده می شود.
سیستم کنترل: سیستم کنترل جوشکاری مقاومتی نقطه ای نقش مهمی در کنترل پارامتر های جوشکاری و تضمین کیفیت اتصال دارد. این سیستم شامل کنترلر ها، سنسور ها و نمایشگر ها است که به کاربر امکان کنترل و نظارت بر فرایند جوشکاری را می دهند.
جوشکاری مقاومتی درز جوش (RSEW) چیست؟
جوشکاری مقاومتی درز جوش (RSEW) یا Resistance Spot Welding به یک روش جوشکاری مقاومتی اشاره دارد که در آن، اجزای مختلف با استفاده از جریان الکتریکی و فشار متقابل به هم جوش داده می شوند. این روش جوشکاری بیشتر در صنایع خودرو سازی، صنایع فلزی و ساخت و ساز استفاده می شود.
در روش جوشکاری مقاومتی درز جوش، دو تکه فلزی که قصد جوشکاری آنها را دارید، بین دو الکترود قرار می گیرند. الکترود ها جریان الکتریکی با توان ولتاژ بالا را از خود عبور می دهند و در نقاط مشخصی بر روی سطح قرار گرفته، فشاری بر روی تکه های فلزی اعمال می کنند.
فشار متقابل همراه با جریان الکتریکی باعث ایجاد حرارت و ذوب نقاط تماس فلزی می شود. در نتیجه، فلزات ذوب شده با یکدیگر امتزاج می کنند و پس از خنک شدن، جوش درز ایجاد می شود. روش جوشکاری مقاومتی درز جوش برای اتصال قطعات فلزی با ضخامت کم استفاده می شود و می تواند به صورت خودکار یا نیمه خودکار انجام شود.
این روش جوشکاری سریع و کارآمد است و باعث ایجاد اتصالات قوی و مقاوم در برابر فشار، بارگذاری حرارتی و اثرات محیطی می شود. علاوه بر این، نیاز به مصرف جوشکاری ندارد و قطعات متصل به هم قابلیت جدا شدن و مجدداً اتصال دادن را دارند.
استفاده از جوشکاری مقاومتی درز جوش (RSEW) به دلیل سرعت بالا، کنترل دقیق و قابلیت اتصال قطعات فلزی با ضخامت کم، در صنایع مختلف بسیار رایج است.
مزایای جوشکاری مقاومتی درز جوش (RSEW)
جوشکاری مقاومتی درز جوش (RSEW) یکی از روش های جوشکاری است که برای اتصال قطعات فلزی استفاده می شود. این روش دارای مزایای زیادی است که به شرح زیر می باشد:
سرعت بالا: جوشکاری مقاومتی درز جوش یک روش سریع برای اتصال قطعات فلزی است. با استفاده از این روش، می توان به سرعت زیادی قطعات را به هم متصل کرد، که این امر برای تولید انبوه قطعات و کاهش زمان تولید بسیار مهم است.
کارایی بالا: با استفاده از جوشکاری مقاومتی درز جوش، اتصالات قوی و مقاومی بین قطعات فلزی تشکیل می شود. در این روش، جریان الکتریکی از طریق قطعات جوشکاری شده می گذرد و باعث ایجاد گرما و ذوب قسمت هایی از قطعات می شود. سپس با فشار دادن قطعات به هم، جوش تشکیل می شود.
به علت استفاده از جریان الکتریکی، قطعات با سرعت بالا گرم می شوند و زمانی که جوش در حال تشکیل است، به سرعت خنک می شوند. این امر باعث کاهش حداقلی تغییر شکل مواد و در نتیجه کاهش تنش های باقیمانده در جوش می شود.
هزینه کمتر: جوشکاری مقاومتی درز جوش هزینه های کمتری نسبت به برخی از روش های جوشکاری دیگر، مانند جوشکاری قوس الکتریکی دارد. علاوه بر این، این روش نیاز به تجهیزات ساده تری دارد که می تواند هزینه ها را به حداقل برساند.
عدم نیاز به مواد جانبی: در جوشکاری مقاومتی درز جوش، معمولاً نیازی به استفاده از مواد جانبی نیست. در روش هایی مانند جوشکاری قوس الکتریکی، ممکن است نیاز به الکترود یا سیم جوش داشته باشید، اما در RSEW نیازی به مصرف مواد جانبی مانند این نیست.
قابلیت استفاده در اتصال قطعات مختلف: جوشکاری مقاومتی درز جوش قابلیت استفاده در اتصال قطعات مختلف فلزی را دارا است. این روش برای اتصال قطعات با ضخامت های متفاوت و حتی قطعات فلزی با ویژگی های متفاوت کاربرد دارد.
تجهیزات جوشکاری مقاومتی درز جوش (RSEW)
تجهیزات مورد نیاز برای جوشکاری مقاومتی درز جوش شامل موارد زیر می شوند:
ترانسفورماتور: این تجهیز از جریان بالا تغذیه می شود و ولتاژ و جریان را تا مقدار مورد نیاز برای جوشکاری تنظیم می کند.
الکترود ها: الکترود ها برای ایجاد جریان الکتریکی و انتقال حرارت به قطعات فلزی استفاده می شوند. الکترود ها معمولاً از مواد مقاومتی مانند مس یا آلیاژ های مس-کروم تهیه می شوند.
کنترل کننده جریان: این دستگاه برای تنظیم جریان الکتریکی استفاده می شود. این کنترل کننده به ترانسفورماتور متصل شده و جریان را به مقدار مورد نیاز برای جوشکاری تنظیم می کند.
سیستم خنک کننده: هنگام جوشکاری، قطعات فلزی گرم می شوند و برای جلوگیری از آسیب به تجهیزات یا قطعات، سیستم خنک کننده استفاده می شود. این سیستم معمولاً شامل یک مبدل حرارتی و یک منبع آب خنک است.
سیستم کنترل دما: برای کنترل دمای جوشکاری و جلوگیری از ذوب شدن زیاد یا ضعیف شدن قطعات، سیستم کنترل دما استفاده می شود. این سیستم معمولاً شامل حسگرها و یک واحد کنترل است.
جوشکاری مقاومتی زائده ای (RPW) چیست؟
جوشکاری مقاومتی زائده ای (RPW) به عملیات جوشکاری اطلاق می شود که در آن یک جریان الکتریکی بسیار بالا از طریق قطعات فلزی عبور می کند و باعث ایجاد گرما و جوشکاری قطعات می شود. این فرایند در اصل برای جوشکاری اتصالات الکتریکی در صنعت الکترونیک استفاده می شود، اما در برخی موارد دیگر نیز مورد استفاده قرار می گیرد.
در جوشکاری مقاومتی زائده ای، قطعاتی که قرار است جوشکاری شوند، بین دو الکترود مخصوص قرار می گیرند. الکترود ها به منبع تغذیه الکتریکی متصل می شوند که جریان بالا را تأمین می کند. هنگامی که جریان از طریق قطعات عبور می کند، مقاومت الکتریکی موجود در این قطعات باعث ایجاد گرما می شود و باعث جوشکاری قطعات می شود.
یکی از کاربرد های مهم جوشکاری مقاومتی زائده ای در صنعت الکترونیک استفاده از آن برای جوشکاری اتصالات بین قطعات الکترونیکی می باشد، مانند جوشکاری پین ها به برد های مدار چاپی. این روش باعث اتصال قوی و دوام بالا بین قطعات می شود و همچنین زمان جوشکاری کوتاه است. همچنین در برخی صنایع دیگر نیز از جوشکاری مقاومتی زائده ای استفاده می شود، از جمله صنعت خودرو سازی و صنایع فلزی.
مزایای جوشکاری مقاومتی زائده ای (RPW)
این روش به عنوان یکی از روش های جوشکاری فلزات پیوسته استفاده می شود و دارای برخی مزایا است که عبارت اند از:
سرعت جوشکاری: RPW یکی از روش های سریع جوشکاری است. با استفاده از این روش، می توان قطعات را به سرعت بالا جوش داد و زمان تولید را به طور قابل توجهی کاهش داد.
اتصال قوی: جوش های تولید شده توسط RPW دارای اتصالات قوی هستند. در این روش، قطعات با هم فشرده می شوند و به هم جوش داده می شوند، که باعث ایجاد اتصالات محکم و قوی می شود.
تغییر کم حرارتی: در RPW، حرارت تولید شده در طول جوشکاری محدود است و به سرعت از بین می رود. این ویژگی موجب می شود که تغییرات حرارتی در قطعه به حداقل برسد و اثر حرارتی بر روی خواص ماده کاهش یابد.
عدم نیاز به ماده جوشکاری: در RPW، نیازی به استفاده از ماده جوشکاری مانند فلز روی، فلز فشاری یا فلز جوشکاری نیست. بدین ترتیب، هزینه تهیه و استفاده از مواد جوشکاری کاهش می یابد.
کنترل آسان: RPW دارای کنترل آسان است. با تنظیم پارامترهای مربوطه مانند جریان، زمان و فشار، می توان کیفیت جوش را کنترل کرد و جوش های با کیفیت بالا تولید کرد.
تجهیزات جوشکاری مقاومتی زائده ای (RPW)
تجهیزات جوشکاری مقاومتی زائده ای شامل موارد زیر می شود:
سیستم تامین برق: این سیستم شامل منبع تغذیه برقی است که برای ایجاد جریان بالا و فشار مورد نیاز در هنگام جوشکاری استفاده می شود. منابع تغذیه ممکن است شامل ترانسفورماتور های قدرت و یا منابع برق سوئیچینگ باشند.
الکترود ها: در جوشکاری مقاومتی زائده ای، الکترود ها برای ایجاد جریان بین قطعات فلزی استفاده می شوند. الکترود ها باید قادر به تحمل جریان بالا و فشار مورد نیاز در هنگام جوشکاری باشند.
قطعات فشار دهی: قطعات فشار دهی برای ایجاد فشار و اتصال محکم بین قطعات فلزی استفاده می شوند. این قطعات معمولاً شامل اجزای فلزی یا کربیدی هستند که مقاومت بالا در برابر فشار و استحکام حرارتی دارند.
سیستم کنترل: سیستم کنترل برای کنترل جریان و فشار در هنگام جوشکاری استفاده می شود. این سیستم می تواند شامل کنترلر ها، سنسور ها و دستگاه های ایمنی باشد که برای مانیتورینگ و کنترل فرآیند جوشکاری استفاده می شوند.
جوش آپست چیست؟
جوش آپست یک فرایند جوشکاری است که در آن قطعات فلزی با استفاده از جوشکاری به یکدیگر متصل می شوند. اصطلاح “آپست” به یک روش خاص جوشکاری اشاره دارد که به وسیله آن قطعات با فلزات آپستی به هم متصل می شوند.
در جوش آپست، ابتدا قطعات مورد نظر با یکدیگر در تماس قرار می گیرند. سپس یک جرقه الکتریکی بین قطعات ایجاد می شود که باعث حرارت و ذوب شدن فلزات آپستی می شود. در این حالت، قطعات با هم ترکیب شده و پس از سرد شدن، یک جوش قوی و دوام دار شکل می گیرد.
این روش جوشکاری معمولاً در صنایع مختلفی مورد استفاده قرار می گیرد، از جمله صنایع خودرو سازی، ساختمان سازی، تولید لوله ها و سیستم های لوله کشی، صنایع نفت و گاز، و ساخت و سازهای دریایی. جوش آپست به دلیل قوی بودن اتصالات حاصل و امکان استفاده از جوش قابل اطمینان در برابر فشار، ارتعاشات و شرایط آب و هوایی سخت، به عنوان یکی از روش های اصلی جوشکاری مورد استفاده قرار می گیرد.
مزایای جوش آپست
جوش آپست یکی از روش های مهم و پر کاربرد در صنعت جوشکاری است که به وسیلهٔ آن می توان قطعات فلزی را به هم وصل کرد. این روش دارای مزایای زیادی است که به شرح زیر است:
قدرت و استحکام بالا: جوش آپست به وسیلهٔ اتصال قطعات فلزی به هم توسط جوش ورقه ای انجام می شود که استحکام بالایی دارد. این نوع اتصالات قادر به تحمل بار های سنگین و نیرو های قابل توجهی هستند و به این ترتیب قطعات فلزی به طور دقیق و محکم به هم متصل می شوند.
اتصال بدون متریال اضافی: در جوش آپست، برای اتصال قطعات، متریال اضافی مانند پیچ و مهره لازم نیست. این به معنای این است که نیازی به تهیه قطعات اضافی برای اتصال نداریم و همین امر باعث صرفه جویی در هزینه ها و زمان می شود.
سرعت و کارایی بالا: جوشکاری آپست به سرعت بالایی انجام می شود و به همین دلیل در صنعت مورد استفاده قرار می گیرد. فرآیند جوشکاری آپست سریع و کارآمد است و باعث افزایش تولید و کاهش زمان و هزینه های مربوط به عملیات جوشکاری می شود.
امکان جوشکاری قطعات با ضخامت متفاوت: با استفاده از جوشکاری آپست، می توان قطعاتی را با ضخامت های متفاوت با هم وصل کرد. این امکان به صنعت هایی که با قطعاتی با ضخامت متفاوت سر و کار دارند، ارائه می دهد تا بتوانند این قطعات را به صورت محکم و با کیفیت بالا به هم متصل کنند.
کاربرد گسترده: جوشکاری آپست در صنعت های مختلف مانند صنعت خودرو سازی، ساختمانسازی، صنعت دریایی، صنایع هوا و فضا و غیره استفاده می شود. این روش جوشکاری قابلیت اتصال انواع مختلف فلزات را دارد و برای اتصال قطعات فلزی در بیشتر صنایع مورد استفاده قرار می گیرد.
انعطاف پذیری در طراحی: با استفاده از جوشکاری آپست، می توان طرح ها و ساختار های مختلفی را ایجاد کرد. این روش جوشکاری به طراحان و مهندسان امکان می دهد تا قطعات فلزی را به شکل ها و ساختار های خاصی به هم وصل کنند و طراحی های خلاقانه تری انجام دهند.
تجهیزات جوشکاری آپست
در زیر تعدادی از تجهیزات معمولاً استفاده شده در جوشکاری آپست را می توانید بیابید:
منبع تغذیه جوشکاری: این یکی از اجزای اساسی در جوشکاری آپست است. منبع تغذیه جوشکاری الکتریکی برقی را تامین می کند که جهت تشکیل قوس الکتریکی استفاده می شود. این منبع تغذیه باید برای تامین برق مناسب جریان و ولتاژ به عملکرد صحیح جوشکاری آپست کمک کند.
الکترود ها: جوشکاری آپست با استفاده از الکترود های خاص انجام می شود. الکترود ها معمولاً شامل مواد مختلفی مانند فولاد ضد زنگ، فولاد کربنی و آلومینیوم هستند. الکترود ها به عنوان محل جریان الکتریکی و عامل جوشکاری بین قطعات فلزی عمل می کنند.
جریان سنج و ولت متر: این تجهیزات برای اندازه گیری جریان الکتریکی و ولتاژ در حین جوشکاری استفاده می شوند. اندازه گیری دقیق این پارامتر ها برای کنترل صحیح جوشکاری آپست بسیار مهم است.
سیستم خنک کننده: جوشکاری آپست معمولاً باعث تولید حرارت زیاد در نقطه جوش می شود. سیستم خنک کننده با استفاده از آب یا هوا، حرارت تولید شده را از الکترود ها و قطعات فلزی جدا کرده و آن ها را خنک می کند تا از آسیب ناشی از گرمای زیاد جلوگیری شود.
لبه دهنده و آچار جوشکاری: این ابزار ها برای آماده سازی قطعات قبل از جوشکاری مورد استفاده قرار می گیرند. لبه دهنده برای تمیز کردن و شکل دادن به لبه ها و آچار جوشکاری برای نگهداری و پرچیدن قطعات در موقعیت مناسب استفاده می شود.
جوشکاری انفجاری (EW) چیست؟
جوشکاری انفجاری (EW) یا به انگلیسی “Explosive Welding”، یک فرآیند جوشکاری خاص است که در آن دو قطعه فلزی با استفاده از انفجار متقابل به هم وصل می شوند. در این فرآیند، دو قطعه فلزی که قصد اتصال آن ها را داریم، به صورت موازی در کنار هم قرار می گیرند.
سپس بین این دو قطعه، یک لایه انفجاری (explosive layer) که معمولاً از موادی مانند تیتانیوم یا آلومینیوم تشکیل شده است، قرار می گیرد. پس از آماده سازی، متفجرات در اطراف لایه انفجاری قرار داده می شوند و در نقاط استراتژیکی جای داده می شوند.
سپس با استفاده از انفجار متقابل متفجرات، لایه انفجاری بین دو قطعه فلزی تحریک می شود. انفجار متقابل باعث افزایش فشار و دما در نقاط تماس بین قطعات فلزی می شود و در نتیجه، باعث جوشکاری آنها به هم می شود. جوشکاری انفجاری به دلیل قدرت و سرعت بالای انفجار، قابلیت اتصال متریال های مختلف را داراست.
همچنین این روش می تواند در اتصال قطعاتی با اندازه و شکل های مختلف نیز مورد استفاده قرار گیرد. در برخی از صنایع مانند صنایع هوا و فضا، دریایی و خودرو سازی، جوشکاری انفجاری برای اتصال قطعات فلزی با استحکام و چسبندگی بالا استفاده می شود.
مزایای جوشکاری انفجاری (EW)
در زیر مزایای جوشکاری انفجاری را بررسی می کنیم:
اتصال قوی: جوشکاری انفجاری باعث ایجاد اتصالات بسیار قوی و محکم بین قطعات فلزی می شود. این روش قادر است به شکل موثری قطعات را به یکدیگر متصل کند و اتصالاتی با استحکام بالا و مقاوم در برابر نیرو های مکانیکی، لرزش ها و فشار های بالا ایجاد کند.
عدم نیاز به مواد جداگانه: در جوشکاری انفجاری، نیازی به مصرف مواد جداگانه مانند الکترود یا فیلر نیست. انفجار مواد منفجره مستقیماً به عنوان منبع انرژی برای جوشکاری استفاده می شود. این امر باعث کاهش هزینه ها و زمان مورد نیاز برای اجرای عملیات جوشکاری می شود.
اتصالات خالص: جوشکاری انفجاری باعث ایجاد اتصالات خالص و بدون آلایش بین قطعات فلزی می شود. این امر مخصوصاً در برخی صنایعی که نیاز به اتصالات با خواص مکانیکی و شیمیایی استاندارد دارند، بسیار مهم است. جوشکاری انفجاری معمولاً باعث حفظ خواص فیزیکی و شیمیایی قطعات جوش داده شده می شود.
عملکرد در شرایط سخت: جوشکاری انفجاری قابلیت کار در شرایط سخت و خشن را دارد. این روش جوشکاری می تواند در محیط های با دما های بسیار بالا یا پایین، فشار های بالا، زمین های نفتی و صنایع دریایی کاربرد داشته باشد. این امر از اهمیت بالایی برخوردار است زیرا در برخی موارد دیگر روش های جوشکاری سنتی قادر به انجام عملیات نیستند.
اندازه گیری کم: در جوشکاری انفجاری، برخلاف برخی روش های جوشکاری دیگر که نیاز به تجهیزات گسترده و پیچیده دارند، تجهیزات مورد نیاز برای انجام این روش ساده و کوچک است. این امر باعث کاهش هزینه ها و زمان مورد نیاز برای تهیه و نگهداری تجهیزات می شود.
تجهیزات جوشکاری انفجاری (EW)
تجهیزات جوشکاری انفجاری شامل عناصر زیر می شوند:
ماشین جوشکاری انفجاری: این ماشین شامل منبع تغذیه الکتریکی است که انرژی لازم برای تولید تخلیه الکتریکی در جوشکاری را فراهم می کند. ماشین جوشکاری انفجاری معمولاً شامل ترانسفورماتور ها، کویل ها، قطبش ها و سیستم های کنترل الکتریکی است.
الکترود ها: الکترود ها برای ایجاد تخلیه الکتریکی استفاده می شوند. آن ها به صورت مستقیم به ماشین جوشکاری متصل می شوند و به سطح قطعه کار نزدیک می شوند. الکترود ها ممکن است شامل نوار ها، سیم ها یا سوپاپ ها باشند.
قطعات کار: قطعات کار که قرار است جوشکاری شوند، باید قادر باشند تا تحمل انفجار الکتریکی باشند. این قطعات معمولاً از فلزات مانند فولاد و آلومینیوم ساخته می شوند.
سیستم خنک کننده: در جوشکاری انفجاری، بعد از انجام عمل جوشکاری، قطعه کار و الکترود ها گرم می شوند. بنابراین، سیستم خنک کننده استفاده می شود تا از افزایش دما جلوگیری کرده و قطعه کار را سریعاً خنک کند.
جوشکاری زیر آب چیست؟
جوشکاری زیر آب یا همان زیر آبی، فرایندی است که در آن عملیات جوشکاری و اتصال قطعات فلزی در محیط آب انجام می شود. این فرایند به وسیلهی جوشکاران زیر آبی انجام می شود که با استفاده از تجهیزات خاص و مهارت های فنی منحصر به فرد، قادر به جوشکاری و تعمیر قطعات فلزی در زیر سطح آب هستند.
برخلاف جوشکاری های معمولی که در محیط های خشک و باز انجام می شوند، در جوشکاری زیر آب می بایست مشکلاتی از جمله حرارت، فشار و تماس با آب را در نظر گرفت. برای مثال، حرارت تولیدی در جوشکاری زیرآب به سرعت توسط آب خنک می شود و در نتیجه جوشکاری بدون تغییر در سختی و خواص فلز انجام می شود.
از کاربرد های رایج جوشکاری زیر آب می توان به تعمیرات زیر آبی سازه های فلزی دریایی مانند سازه های نفت کش، مخازن نفت و گاز، میادین نفتی زیر آبی و پلا هی دریایی اشاره کرد. همچنین، این فناوری در صنایع دریایی، زیر دریایی سازی و تحقیقات زیر آبی نیز کاربرد دارد.
استفاده از جوشکاری زیر آب نه تنها باعث افزایش سرعت و کارایی در تعمیرات و ساختار های زیر آبی می شود، بلکه با کاهش هزینه ها و زمان مورد نیاز برای خشک کردن و سطح سنجی قبل از جوشکاری، از لحاظ اقتصادی نیز مزیت دارد.
مزایای جوشکاری زیر آب
مزایای جوشکاری زیر آب عبارت اند از:
حفظ کیفیت و عملکرد جوش: جوشکاری زیر آب باعث حفظ کیفیت جوش و کاهش نیرو ها و تنش های حاصل از حرارت می شود. با عدم تماس مستقیم با هوا، جوشکاری زیر آب می تواند از اکسیداسیون و آلایش جوش جلوگیری کند.
کاهش دما و تنش های حرارتی: زیر آب بودن فرآیند جوشکاری می تواند باعث کاهش دما و تنش های حرارتی شود. این باعث می شود که تغییر حرارتی در محل جوشکاری کاهش یابد و احتمال تشکیل ترک و تغییر خواص مکانیکی جوش کاهش یابد.
کنترل پارامتر های جوشکاری: با استفاده از جوشکاری زیر آب، می توان پارامتر های جوشکاری را به طور دقیق کنترل کرد. به دلیل وجود آب در اطراف جوش، میزان خنک شدن و سرعت خنک شدن جوش می تواند بهطور دقیق تنظیم شود.
کاهش خطرات: با استفاده از جوشکاری زیر آب، خطرات احتمالی مانند آتش سوزی، انفجار، دود و آلاینده های جوشکاری کاهش می یابند. این امر برای فضا های محدود و مناطق خطرناک بسیار مهم است.
امکان جوشکاری در محیط های آبی: با استفاده از جوشکاری زیر آب، میتوان در محیط های آبی مانند زیر دریا ها، رودخانه ها و استخر ها جوشکاری انجام داد. این به ویژه در صنایع دریایی، ساخت سازه های فلزی در زیر آب و تعمیرات زیر آبی مفید است.
تجهیزات جوشکاری زیر آب
در زیر به برخی از تجهیزات مورد نیاز برای جوشکاری زیر آب اشاره می کنیم:
الکترود های زیر آب: برای جوشکاری زیر آب، شما نیاز به الکترود های خاصی دارید که قادر به کار در محیط آب باشند. این الکترود ها باید مقاومت خوبی در برابر آب داشته باشند و بتوانند جریان الکتریکی را در محیط آب منتقل کنند.
منبع تغذیه: برای ایجاد جریان الکتریکی برای جوشکاری زیر آب، نیاز به منبع تغذیه خاصی دارید که بتواند جریان مورد نیاز را در محیط آب ایجاد کند. منابع تغذیه زیر آب باید ضد آب و مقاوم در برابر شرایط محیطی آب باشند.
سیستم خنک کننده: در جوشکاری زیر آب، نیاز به سیستمی برای خنک کردن الکترود ها و منبع تغذیه دارید. این سیستم می تواند شامل یک یا چند پمپ خنک کننده، مبدل حرارتی و مخزن آب باشد.
محافظ حفاظتی: در جوشکاری زیر آب، برای حفاظت از جوشکار و تجهیزات در برابر آب، از محافظ حفاظتی استفاده میشود. این محافظ می تواند شامل لباس های مخصوص، عینک حفاظتی و دستکش های ضد آب باشد.
سیستم نگهدارندهی قطعات: در جوشکاری زیر آب، برای نگهداری قطعات در محل دقیق جوشکاری، از سیستم نگهدارنده های خاصی استفاده میشود. این سیستم می تواند شامل مغناطیس ها، فشار های هیدرولیک یا پنوماتیک و سیستم های مکانیکی باشد.
جوشکاری سر بالا چیست؟
جوشکاری سر بالا (Overhead welding) یک فرایند جوشکاری است که در آن قطعات فلزی یا جوش ها در موقعیت هایی جایگذاری می شوند که جوشکار برای دسترسی به آن ها باید بالای سر خود کار کند. این نوع جوشکاری در مواردی کاربرد دارد که قطعات و ساختارهایی بزرگ و گنگ وجود دارند و جوشکار برای دسترسی به آن ها باید بالا برود.
مثلاً در موقعیت هایی که قطعات بر روی سقف، سقف تونل ها، کانال های هوا، پل ها و سازه های بلند قرار دارند. برای جوشکاری سر بالا، جوشکار باید در موقعیتی قرار بگیرد که بتواند ابزار های جوشکاری را بر روی قطعه قرار دهد و از بالای سر خود کار کند. این می تواند چالش هایی مانند دسترسی محدود، نا امنی موقعیت کاری و دید محدود را برای جوشکار ایجاد کند.
بنابراین، برای جوشکاری سر بالا، تجهیزات ایمنی مناسب و آموزش جوشکاری متناسب با این نوع کار الزامی است. جوشکاری سر بالا مهارت و تجربه قوی از جوشکاری و همچنین آگاهی کامل از روش های ایمنی و استفاده صحیح از تجهیزات جوشکاری را می طلبد.
مزایای جوشکاری سر بالا
جوشکاری سر بالا یکی از روش های اتصال قطعات فلزی است که در بسیاری از صنایع و بخش های مختلف استفاده میشود. این روش دارای بسیاری از مزایا است که در زیر به توضیح برخی از آن ها میپردازیم:
استحکام بالا: جوشکاری سر بالا می تواند اتصالات بسیار قوی و مقاومی بین قطعات فلزی ایجاد کند. با استفاده از فنون و روش های مناسب جوشکاری، اتصالات سر بالا به طور کامل به قطعات پایه متصل می شوند و قدرت کششی و تحمل بار بالایی دارند.
انعطاف پذیری: جوشکاری سر بالا می تواند در تنوع وسیعی از فلزات و ضخامت های مختلف استفاده شود. با تنوع این روش، میتوان اتصالات را بین قطعات فلزی با ضخامت ها و ابعاد متفاوت ایجاد کرد و در بسیاری از صنایع مورد استفاده قرار داد.
کارایی بالا: جوشکاری سر بالا به طور عمومی یک روش سریع و کارآمد برای اتصال قطعات فلزی است. فرآیند جوشکاری سر بالا می تواند به سرعت صورت بگیرد و نیاز به زمان کمتری برای تکمیل اتصالات داشته باشد. همچنین، با استفاده از تجهیزات و ماشین آلات مناسب، می توان این روش را به صورت خودکار و پیوسته انجام داد.
کنترل کیفیت: جوشکاری سر بالا امکان کنترل کیفیت اتصالات را فراهم می کند. با استفاده از روش های مختلفی مانند بررسی بازرسی های غیر مخرب (مانند آزمون های رادیوگرافی و فلز شناسی) و کنترل جوش، می توان مطمئن شد که اتصالات سر بالا مطابق با استاندارد ها و مشخصات فنی مورد نظر هستند.
کاربرد گسترده: جوشکاری سر بالا در صنایع مختلفی مانند صنعت خودرو سازی، صنعت ساختمان، صنعت دریایی، صنعت هوا و فضا، صنعت نفت و گاز و بسیاری از صنایع دیگر استفاده می شود. این روش به دلیل مزایایی که ارائه می دهد، یکی از روش های پر کاربرد در اتصال قطعات فلزی محسوب می شود.
جوشکاری برق چیست؟
جوشکاری برق یا به عبارت دقیق تر جوشکاری با استفاده از روش برقی، یک فرایند صنعتی است که برای اتصال دو قطعه فلزی یا آلیاژ فلزی از طریق اعمال حرارت و فشار و انتقال جریان برق استفاده می شود. در این فرایند، جوشکار با استفاده از سیم های جوشکاری خاص و یا الکترود های محدودهای (Electrodes)، جریان الکتریکی بین قطعات را ایجاد می کند.
این جریان الکتریکی باعث ایجاد حرارتی شدید در محل اتصال قطعات می شود که باعث ذوب شدن قسمت های مورد نظر می شود. در ادامه، با توقف جریان الکتریکی و خنک شدن قسمت ها، جامد شدن و اتصال دائمی بین قطعات ایجاد می شود.
جوشکاری برق به دلیل سرعت و کارآیی بالا، امکان جوشکاری قطعات باضخامت های مختلف، قابلیت اتصال مواد فلزی مختلف و قدرت اتصال بالا، در صنایع مختلف استفاده می شود. این فرایند در صنایع خودرو سازی، ساخت و ساز، صنایع فلزی، صنعت نفت و گاز، صنایع الکترونیکی و بسیاری از صنایع دیگر به عنوان یکی از روش های اتصال مورد استفاده قرار می گیرد.
مقاله جوشکاری برق چیست؟ در سایت باملو به بررسی جوشکاری برق میپردازد، که یکی از روشهای مهم و پرکاربرد در صنعت جوشکاری است. در این مقاله ، به معرفی اصول اساسی و فنون مختلف جوشکاری برق میپردازیم. ابتدا با اهمیت جوشکاری برق در انواع صنایع، از جمله صنعت خودروسازی، هوافضا، نفت و گاز، ساختمانسازی و صنایع فلزی آشنا میشوید.
در این مقاله، نحوهی کارکرد جوشکاری برق به عنوان یک فرآیند حرارتی و فشاری بررسی میشود. همچنین، انواع الکترودهای جوشکاری برق، مزایا و معایب هر یک، و استفاده مناسب آنها در صنایع مختلف به تفصیل شرح داده میشود.
در جریان مقاله، به اهمیت استفاده از دستگاهها و تجهیزات مدرن در جوشکاری برق تا افزایش کیفیت جوشکاری و کاهش هزینهها پرداخته میشود. همچنین، مسائل ایمنی مرتبط با جوشکاری برق و نیازمندیهای استفاده از تجهیزات ایمنی بهطور جدی مورد تاکید قرار میگیرد.
از این مقاله برای کسانی که به دنبال اطلاعات کامل و معتبر دربارهی جوشکاری برق هستند، استفاده کنند و امیدواریم که مطالب ارائه شده، به دانش و فهم بهتر این فرآیند کمک کند.
مزایای جوشکاری برق
جوشکاری برق یکی از روشهای اتصال و یا تعمیر قطعات فلزی است و دارای بسیاری از مزایا است که عبارت اند از:
اتصال قوی: جوشکاری برق به وسیله اعمال جرقه های الکتریکی بین قطعات فلزی، اتصال قوی و محکمی را ایجاد میکند. این نوع اتصال به طور عمده برای قطعاتی که نیاز به استحکام بالا دارند، مانند سازههای فلزی و وسایل نقلیه، مناسب است.
تنوع وسایل قابل جوشکاری: با استفاده از جوشکاری برق می توان مجموعهای گسترده از فلزات را جوشکاری کرد، از جمله فولاد، آلومینیوم، استیل و بسیاری دیگر. همچنین، میتوان قطعات فلزی را با قطعات غیر فلزی مثل پلاستیک و سرامیک نیز جوشکاری کرد.
سرعت اجرا: جوشکاری برق از نظر سرعت اجرا مقرون به صرفه است و میتوان در زمان کوتاهی قطعات را جوشکاری کرد. این امر می تواند در تولید انبوه و صنعتی بسیار مفید باشد.
عملکرد در شرایط مختلف: جوشکاری برق قابلیت عملکرد در شرایط مختلفی را دارد. به عنوان مثال، می توان در محیط های با دما و فشار بالا، زیر آب، در فضا و حتی در محیط های خطرناک جوشکاری برق انجام داد.
قابلیت تعمیر: در صورت لزوم تعمیر قطعات جوشکاری شده، میتوان آن ها را با استفاده از جوشکاری برق دوباره تعمیر کرد یا اتصالات جدیدی بر روی قطعات ایجاد کرد.
کاربرد های وسیع: جوشکاری برق در صنایع مختلفی مانند خودرو سازی، ساختمان سازی، تولید لوازم خانگی، صنایع دریایی، هوا و فضا و بسیاری از صنایع دیگر کاربرد دارد.
کنترل قابلیت: با استفاده از تجهیزات و تکنولوژی های پیشرفته در جوشکاری برق، می توان عملکرد و کیفیت اتصالات را بهبود بخشید و به طور دقیق کنترل کرد.
سخن پایانی
در این مقاله با انواع جوشکاری ها آشنا شدید و دانستید هر کدام چه مزایایی دارند. همچنین با تجهیزات هر یک از این جوشکاری ها آشنا شدید. امید است این مطلب برای شما مفید واقع شده باشد و بتوانید از آن نهایت استفاده را ببرید.